That's a little tougher.
The hardest part or should I say most dangerous part is removing/installing the Coil spring. Again, I am not sure what size all the bolts are.
Tools:
Jack & Jack Stands
Assorted metric send wrenches
Assorted metric sockets and ratchets with breaker bars - air tools if you got them.
Ball Joint separator - pickle fork.
Tie rod seperator tool. May be able to rent/borrow one from AutoZone or Checker
Coil Spring compressors?
Hammer with a drift punch
Various pliers and other hand tools.
Ball Joint Press
Chain
Long pry bar
Since you have to separate the spindle from the A Arms, it's a good time to replace the upper and lower ball joints. Also a good idea to replace inner and outer tie rod ends and rack boots. Look at the bushing on the right side of the rack - replace if worn. If you install new bushings but do not install new ball joints, tire rods, etc. the alignment shop may not do the work due to worn parts. Best practice is to replace everything.
Jack up the car and place the jack stands under the car on the frame and lower the car allowing the suspension to hang.
Remove the tire and use the PB Blaster generously on all the bolts. 2 in the upper a arm on the frame/crossmember. 2 on the lower a arm at the frame/crossmember. 1 on each ball joint - clean the dirt and grease off of these first and 1 on the tie rod at the spindle. again, amount of rust will determine the amount of PB Balster required. Another good practice is to get new bolts for the upper and lower a arms and new paddle nuts for the upper a arms (depends on how rusted they are). There is a nut on the top of the shock and 2 bolts on the bottom that need PB Blaster too! Also the bolts for the sway bar are usually rusted bad and will break when taking them off. Naother thing you may want to d oat this time is new sway bar mount bushings and links. I use RD's zero lash sway bar links and love them. Some of the full poly kits will come with new bolts and sleeves with poly link bushings.
Here's the parts I used on the last 88 I did:
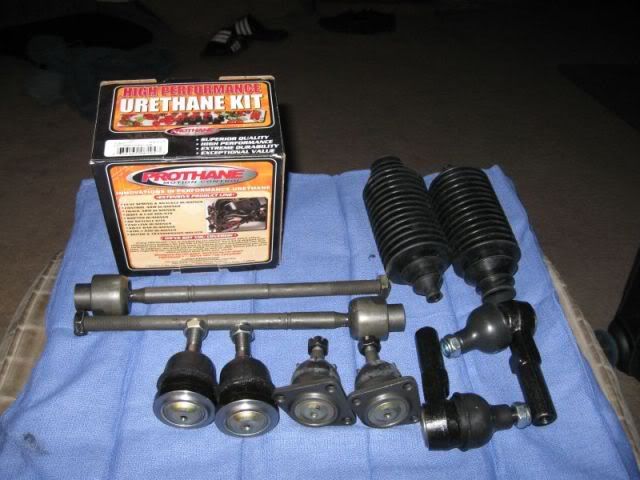
Not pictured is Rodney Dickman's brass rack bushing and zero lash sway bar links.
Start by placing the jack under the ball joint on the lower a arm and put some "weight" of the car on the jack/suspension. Remove the nut from the top of the shock. Sometimes these can be rusted and may require the destruction of the shock to get it out. Remove the 2 bolts under the lower a arm that holds the shock in place and remove the shock.
Remove the tie rod nut and seperate the tie rod from the spindle.
Remove the upper ball joint nut - there should be a cotter pin too. Using the pickle fork, seperate the ball joint from the spindle. Remove the 2 top a arm bolts at the frame/crossmember and remove the upper a arm.
Remove the nut from the lower ball joint. Use the pickle fork to seperate the spindle from the lower ball joint/a arm. Use care here as the spindle is heavy and awkward. Have some bailing wire or a bungee cord close by so that you can "hang" the spindle/rotor/caliper from the car - use care not to put too much pressure/weight on the brake line.
Now here is the dangerous part and I am not sure there is a "good" way to do this. I use a short piece of chain and loop it around the coil spring and through the lower a arm - loose enough to have some slack but tight enough to prevent the spring from jumping out at you. I have heard of folks using some type of spring compressor but I have been unable to find any that will fit in the tight space of the Fiero. Others will tie or strap the spring in a compressed state. For me, the chain thing has worked everytime without fail. Once you have the chain in place of use some type of spring compressor, get yourself off to the side of the car and slowly lower the jack. Sometimes, this will not allow you to remove the spring due to the a arm not traveling downward enough. Use extreme caution when dealing with the spring. For me, once I have the pressure off the jack, the a arm is pointing almost straight down and the spring is just sitting in the spring cup enough to keep it from falling out. Using a long pry bar, I pry the spring out fo the cup and remove the spring. I can't strees the use of caution here. That spring can cause a lot of damage should it come flying out of there. Others may chime in here and have better idea. The chain will keep it from flying around.
Once the spring is out, you can remove the 2 lower a arm bolts and remove the a arm.
If you are replacing the tie rod ends, now is the time. Remove the rack boots. On the rack side of the tie rod, there should be a swedged spot on the end of the tie rod. This "locks" the tie rod from spining as it is threaded onto the rack. Some will grind the swedge down and others will just get a big ass wrench in there and spin the rod off. Once the tie rods are off, you can inspect the rack bushing on the right side - some were plastic and some were metal. Grab the rack rod and see how much play there is in the bushing. I have not seen a plastic one that was not worn out. If it's worn out, you will want to replace it. If you planned ahead, you will have one of RD's bushings in hand. Follow his enclosed instructions to install it. Pay close attention to the part about cleaning all the rust off the rack rod before installing the new bushing. Clean and smooth is the key here. Both on the rack rod and the inside of the rack case where the bushing will fit into. The plastic bushing is a PITA to get out. I took the rack completely out - and paid a big price for doing it because 3 of the 4 bolts that hold the rack in the car broke. It took me more time to fix those 3 broke bolts than it did to rebuild the whole front end. Anyway, Once the rack bushing is in, you can install the new tie rods. Thread them on and tighten them down then "swedge" the lip to lock it in place.
Now you should note that I did not say to remove the old outer tie rod from the old inner tie rod. You can use the old parts as a gauge to set the length of your new ones - this will get you close enough to being aligned to get you to the alignment shop when you are done.
Once the new inner tie rod is installed and locked down, you can slide the new boots on. Some boots come with plastic zip ties to hold them in place. I went to the speed shop and picked up some stainless steel zip ties used for header wrap. Before you tie the boots down, thread the lock nut and the new outer tie rod onto the inner tie rod. Use the old tie rod as a gauge to set the length of the new tie rod(s). Now you can tie the boot in place. You may want to add some lithium grease to the rack rod - turn the steering wheel from side to side so you can coat as much of the rack rod as possible.
Now you can remove the old bushings. Same as above - your choice. Just remember that you will need to leave the outer shell of the bushing in place on the a arm. Too much heat and you can melt these because they are thin. Concentrate the heat to the center of the bushing/inner sleeve. Also, on the upper a arm, the control rod will remain in pace because you are not removing the outer shell. You should be able to slide the rod to one side while you heat the opposite side bushing - these are small bushings and do not take too much heat to burn them out. With one side out, you can slide the rod the other way and get the other one out. This rod may be rusted solid in side the sleeve and can be a little tought to get apart. You just have to work at it.
Now it's time to take out the old ball joints. The bottom one can be "pressed" out with a hammer and some wood blocks or a press. Easy way is to take it to a shop and let them do it for you. Press the old one out and the new one in. Otherwise you will need to rent/borrow or purchase a ball joint press and it can be a pain to get it to go straight. The upper ball joint, if it's never been changed, will be riveted to the a arm. Simply grind the heads off of each (3) rivets and drive the rivet out with a punch. The new ball joint will bolt back in place. Obviously if they have been changed before, they may be bolted in and that makes it a little easier. Once you have the new ball joints installed, you can claen and paint the a arms and make sure that the inside of the shells where the new poly will be installed is clean and smooth.
Install the new poly. I have read some discussion about the bushings on the lower a arm - there is a "thrust" washer - it's a cupped shaped poly unit. Some have said that they had to trim it because it would not fit in the mount on the frame/crossmember. I have never experienced this and have never had to trim the thrust washer. I would say that if it does not fit, something in the monut may be bent or the poly bushing is not correctly installed in the a arm. Again use lots of the silicone lube, push the bushings in first then slide the inner sleeve in. It may take a little nudge to get the sleeve in. Reinstall the parts in the reverse order.
When putting the spring back in, again, use extreme caution. The spring sits in the cup a certain way. When you place the spring back in there, make sure that it is lined up with where it will sit. Place the chain around it and then slowly raise the jack raisiing the lower a arm. You may have to coax the spring to sit in the cup. Sometimes you will have to twist it slightly to make sure it is going in the cup in the right place. Take your time and remember that that spring wants to hurt you. Best bet is if you can find some kind of spring compressor that you can get in there and then back out once it's all together? Once you have the spring back in and in place with the weight of the car on the jack, reinstall the spindle on the lower ball joint, install nut finger tight, install the upper a arm and ball joint/nut finger tight. Install the shock. With the wieght of the car on the jack, go around and tighten all the bolts and nuts to spec. Reinstall the sway bar links. Put the wheel on and head for the other side.
One more suggestion. If you are going to do the rear, do the front too or vice versa. Cheaper to pay for one alignment than 2 and if you do the rear and not the front, the shop may refuse to do the alignment due to worn parts up front. Do it all one time.
Here's some pics for the visual:
Starting them young:
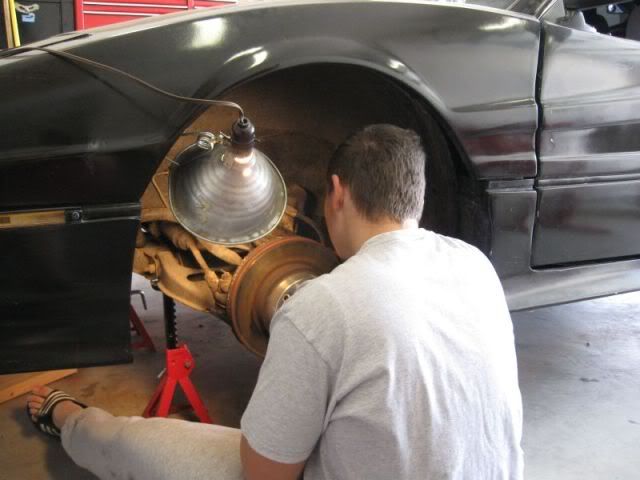
I removed the calipers because I did a brake job at the same time:
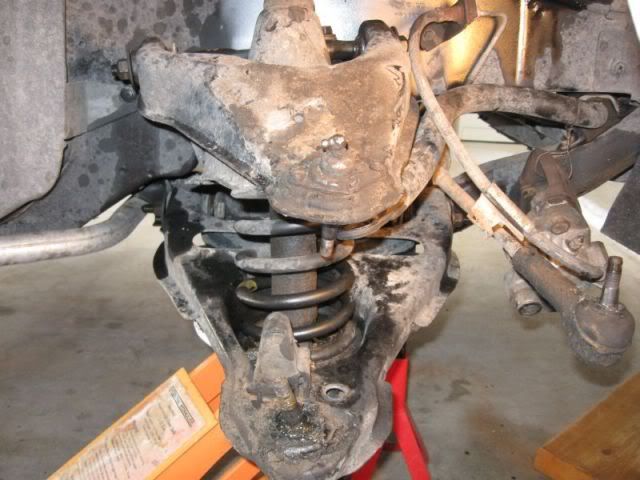
Upper a arm out -- jack in place:
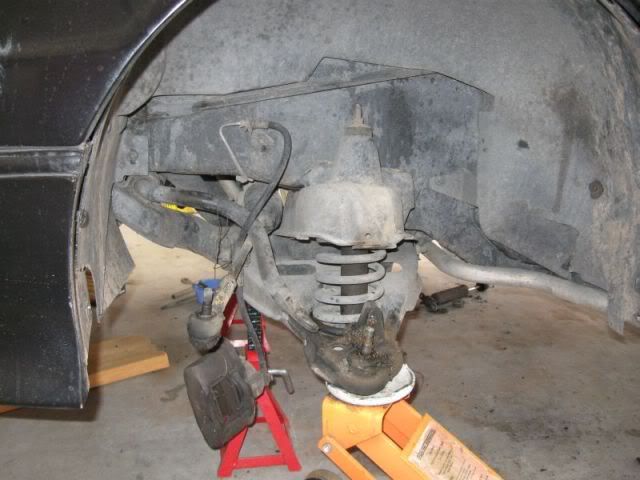
Spring out:
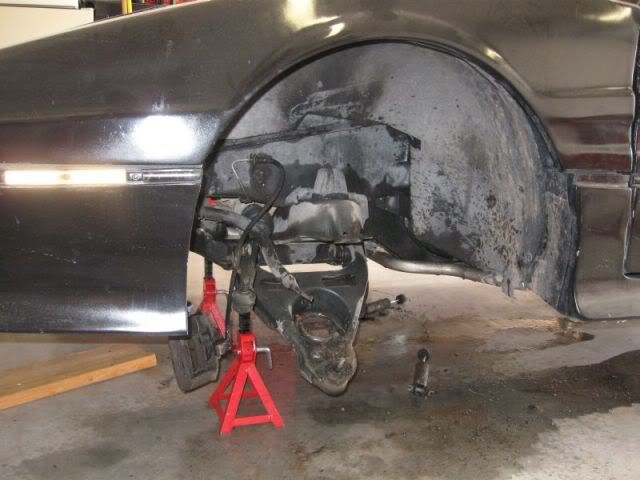
Pressing the new ball joint in:
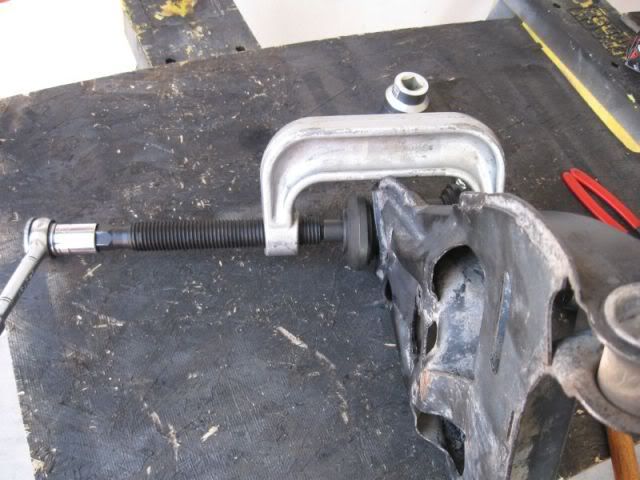
One lower done:
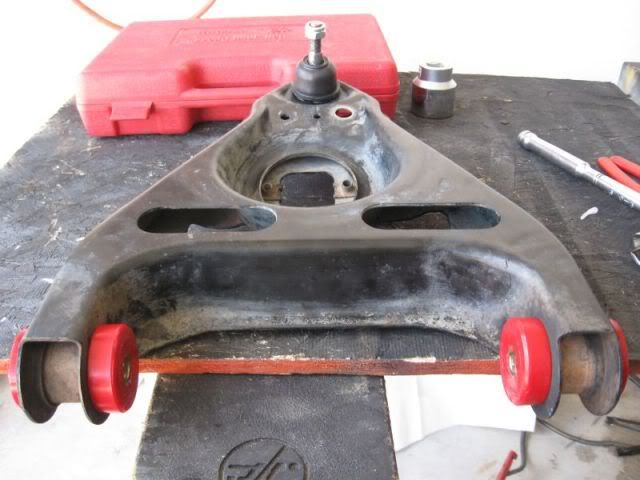
A pair ready:
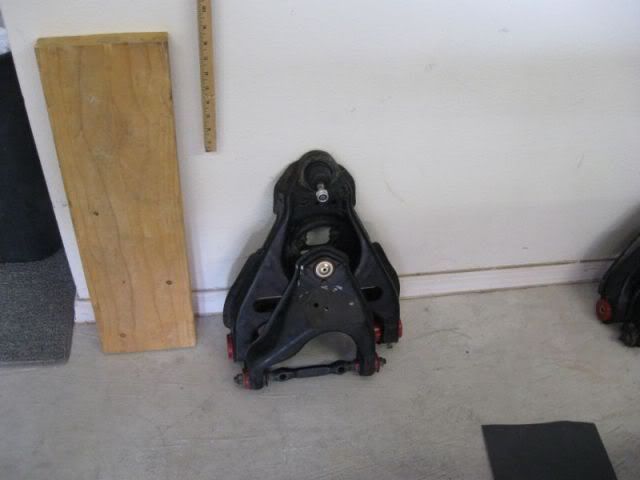
removing the old tie rod. This one had a plastic cover - I removed it and could get to the slots for the wrench:

The dreaded plastic bushing:
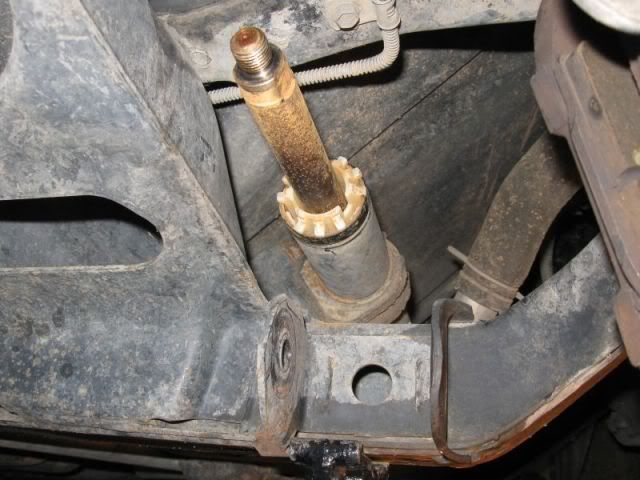
Rack out - RD's bushing installed:
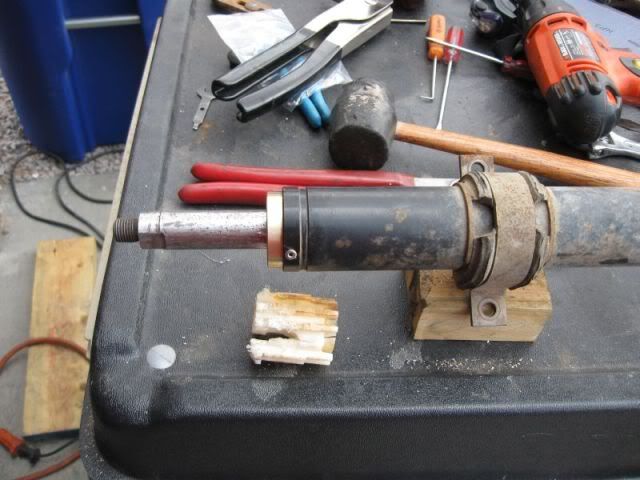
Going back together:
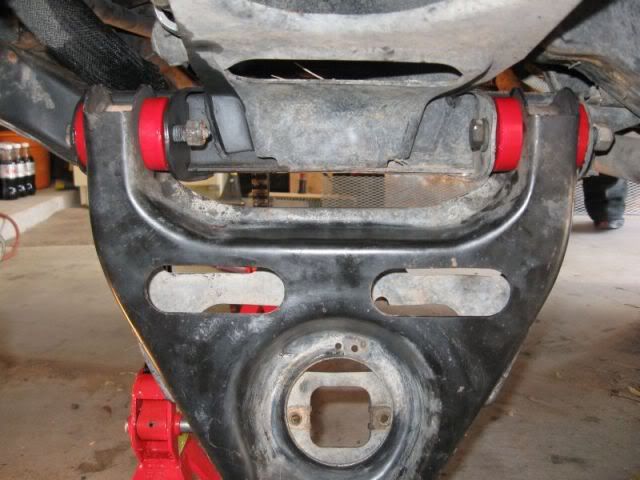
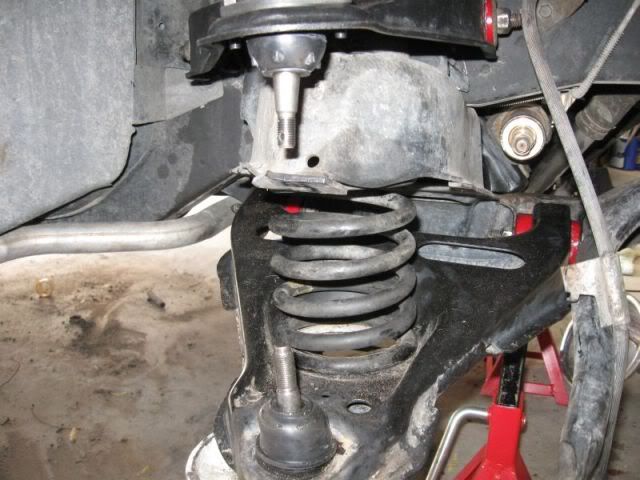
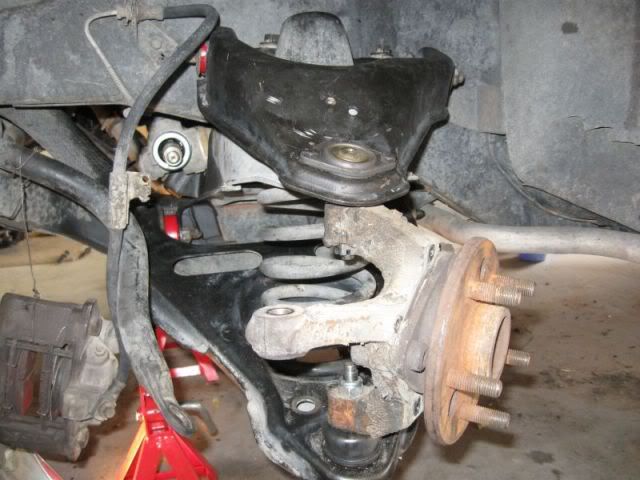
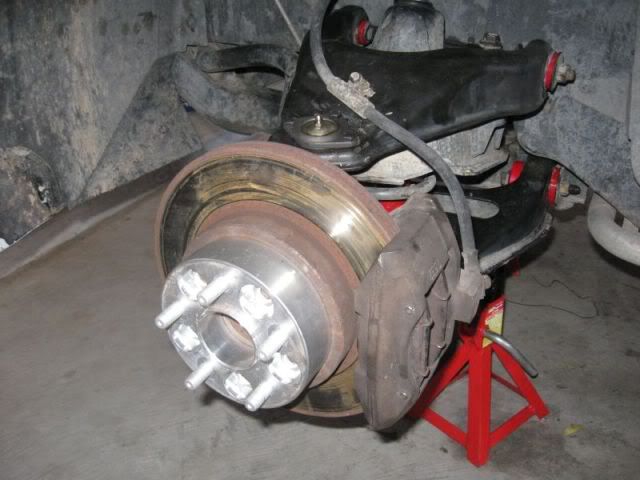
Now it's late and I may have missed something here. I'm sure some will chime in with some better ideas/ways to this. I have just relayed to you how I do it with the tools I have. Just remember to use a lot of caution when dealing with the spring.
Good Luck
Pat