For those of you unfamiliar with the 88 rear suspension "long bolt", here it is in a photo I swiped from FieroCustom:
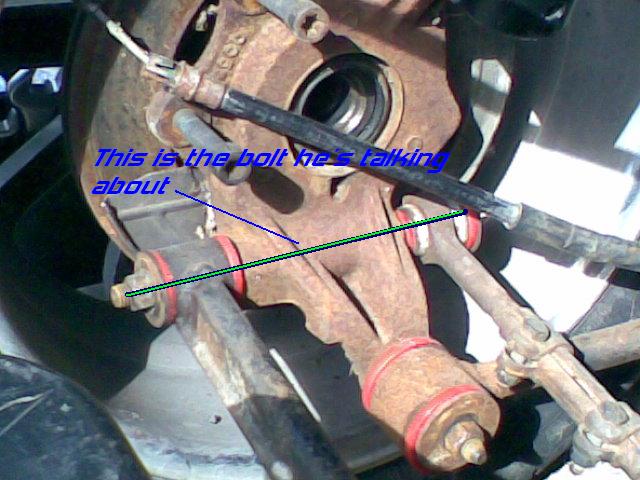
Mine keeps loosening up (as do all 88's with poly in the rear), and I want to fix it by adding a jam nut, as others have done. However, torquing a jam nut is not straightforward or intuitive. The torque spec on the nut for this bolt is 37 ft-lbs + 90°, which works out to about 50 ft-lbs. I've searched the internet for the proper procedure for torquing jam nuts, but apparently the mechanical engineers of the world want to keep this info to themselves. Any ME's here who could shed some light on this?
What I HAVE found is that jam nuts should go under the regular nut, and there should always be tension between the threads of the jam nut and the regular nut. I.e., there should be more torque between the regular nut & jam nut than there is between the jam nut and the assembly being clamped. Otherwise, if the assembly changed dimensions (say, the bushings deformed), the nuts could loosen, which is the problem we have now. The bolt in question is an M12x1.75, and think it's a grade/class 10.9. According to the chart I found, the max torque on this bolt is about 142 ft-lbs, so there's plenty of strength available to increase the torque between the nuts above the 50 ft-lbs needed for the assembly. But... how do you apply, say, 100 ft-lbs of torque between the nuts, and maintain 50 ft-lbs of torque to the assembly? If you torque the jam nut to 50, then the regular nut to 100, the resultant torque to the assembly will be above 50.
Sorry, but I'm just not satisfied with a torque spec of "good 'n tight". I want to determine the right way to do this.
Maybe I just need to dip the whole thing in Loctite.