Many of you know I am clearing out my excess inventory of Fiero cars and parts so I thought it be a good idea to document the process for posterity. In each thread I will share my tricks and ideas. Some you may already know, others hopefully will be
Eureka! moments for some of you. My first thread is removing the V-6 engine.
If you are in need of a new engine for your Fiero the first obvious step is to take out the old one. There are several ways to do this and you should feel free to post your own experiences here as well. The method I am going to show you is the easiest and fastest for those of you with limited tools on hand. I did this in 2 hours and 10 minutes including time taken to photograph the procedure. In fact, it took longer to write this thread than to do the job.

You do NOT need a car lift, special tools, or any particular skills. If you understand the 'righty tighty, lefty loosey' concept then you know enough. Read on!
STEP 1:Gather the tools. Obviously air tools and car lifts make life easier. I have both. However, I am doing this the old fashioned way for the benefit of those of you with nothing more than a typical tool box. You will need the following hand tools:
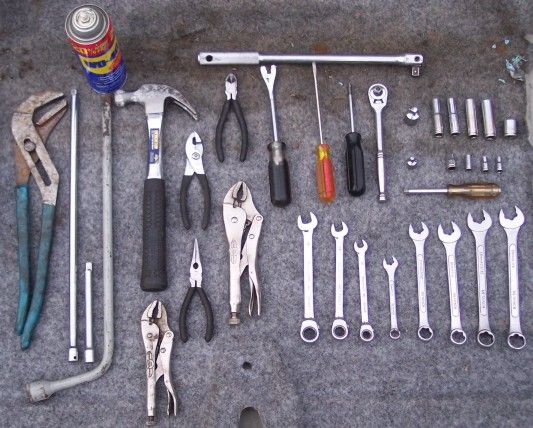
(1) large pair of channel locks
(1) 18 inch 3/8 inch extension
(1) 6 inch 3/8 inch extension
(1) Fiero Tire Iron
(1) Spray can of penetrating lube or WD-40
(1) Hammer
(2) Vise Grip Style Pliers
(1) Standard pliers
(1) Needle Nose Pliers
(1) Wire Cutters (for cutting zip ties, etc.)
(1) 1/2 inch Breaker Bar
(1) Plastic Push Pin Removal Tool
(1) Standard Screw Driver (long thin electrical style)
(1) Philips Screw Driver
(1) 3/8 inch Ratchet
(1) 1/2 inch to 3/8 inch adaptor
(1) 3/8 inch to 1/4 inch adaptor
(1) 6mm 1/4 inch socket
(1) 7mm 1/4 inch socket
(1) 8mm 1/4 inch socket
(1) 10mm 3/8 inch socket (shorty)
(1) 10mm 3/8 inch socket (long)
(1) 11mm 3/8 inch socket (long)
(1) 13mm 3/8 inch socket (long)
(1) 15mm 3/8 inch socket (long)
(1) 18mm 3/8 inch socket (shorty)
(1) 1/4 inch socket screw driver
(1) 10mm Box Wrench (ratchet style if available)
(1) 11mm Box Wrench
(1) 13mm Box Wrench (ratchet style if available)
(1) 15mm Box Wrench (Standard AND ratchet style if available)
(1) 16mm Box Wrench
(1) 18mm Box Wrench
(1) 19mm Box Wrench
BIG TIP #1: I use Metrinch Brand tools which work on either Metric or SAE nuts and bolts. Since a few of the Fiero nuts, mostly in the electrical system, are SAE, these tools make it much easier to work on everything without having to keep extra tools on hand.
BIG TIP #2: A rolling ‘crash cart’ is a convenient way to keep the tools handy and accessible when you are standing in the trunkIn addition to the above mentioned hand tools you will need the following items:
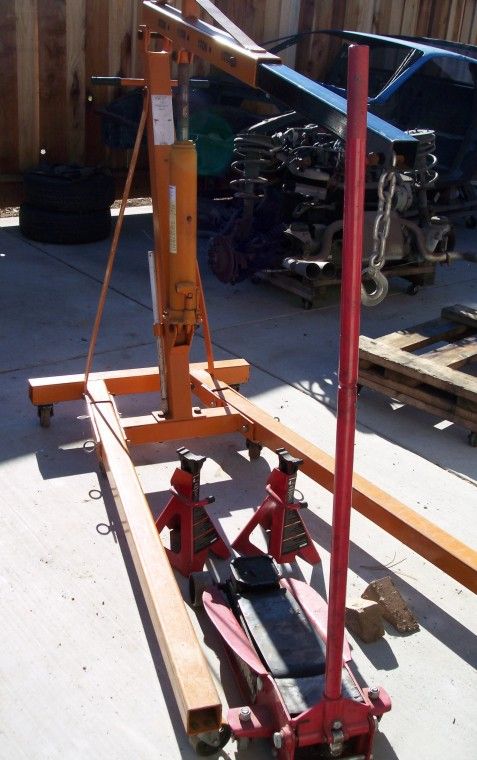
(1) Set of Jack Stands
(1) Cherry Picker
(1) Set of wheel chocks
(1) 2 ton or larger Floor Jack
(1) Engine Dolly
Most of these items are available for purchase at your local Auto Parts store and the prices are surprisingly affordable. If you are on a really tight budget I might suggest looking for used tools on Craig's List or borrow from a friend.
The engine dolly is the one item not available over the counter in the size you will want. It is best to build your own. The measurements are 28x36. This is how to build your own:
Parts List:
(16) 5/16 T-Nuts
(16) 5/16 4" bolts
(4) heavy duty wheel casters
(3) 8' lengths of 2x6 #2 (minimum, #1 is better) Douglas Fir (make sure they are unwarped!) Each board will make (2) 28" lengths and (1) 36" length with 4 inches to spare.
(1) Box of 4" wood screws
(1) Box of 2.5" or 3" wood screws
Assembly:
1) take (2) 28" lengths of 2x6 wood and double them up with a couple of 2.5 or 3" wood screws to create one 4x6x28 block. repeat this step to end up with two blocks.
2) place wheel casters rated to 150 lbs each or better about 2 inches from the ends and centered. Drill through holes.
3) place bolts through and tighten using t-nuts. cut off excess threads flush with boards
4) Take (3) 36" lengths and use (2) 4" wood screws per board to mount them between the two blocks (predrill 1/16" pilot holes to avoid splitting the wood)
5) take (2) 28" lengths and secure them to the top of the dolly with (2) 4" wood screws per board (be sure they are out of synch with the previous 2 wood screws on the lower level)
See reference picture below:
STEP 2:Place the car on a level solid surface. Make sure that you have plenty of space around the rear and sides and chock the front wheels
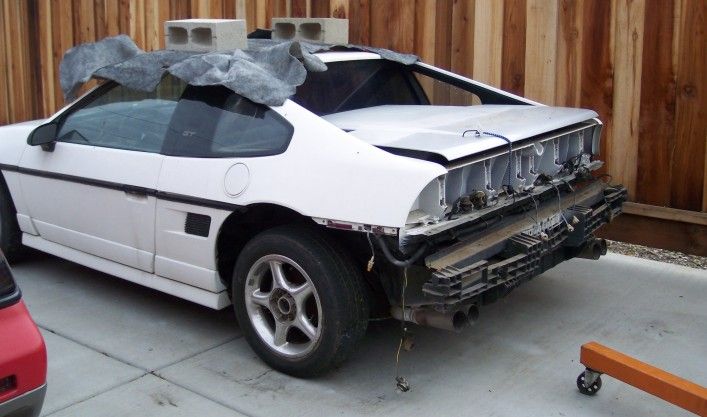
STEP 3:Remove the passenger side vent then disconnect the battery and remove it. Using an 8mm (5/16th actually) socket remove the side post terminals starting with the NEGATIVE terminal first. Then using a 13mm socket remove the battery hold down bolt and rubber mount.
BIG TIP #3: Bolts, screws, and nuts are easy to find if you put them back in the hole you took them out of. For the rest of the odds and ends, bag and tag. Take pictures too for later reference. BIG TIP #4: A battery post wrench with an insulated rubber grip is a good cheap investment. 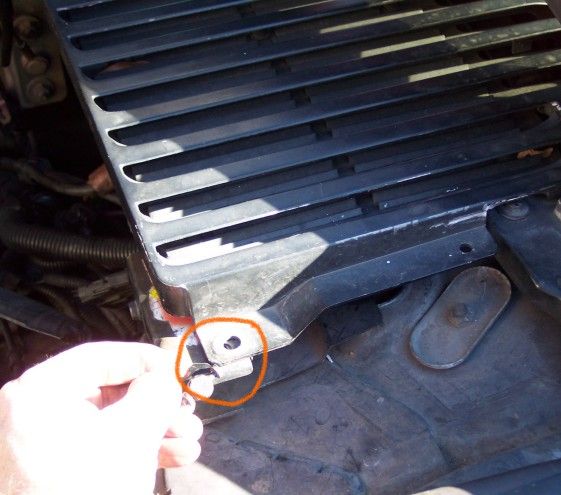
STEP 4:Now move to the interior of the car before you start getting greasy. Remove the 2 long screws holding the center console in place with your 7mm socket.
STEP 5:Remove the ash trays and using your screw driver to pry out the retainer clip holding the shifter in place (for manual trannys, just unscrew the shifter knob). The auto shifter will now pull straight off with a good tug.
STEP 6:Using the 7mm socket unscrew the 4 small screws holding the shift surround in place. The surround will lift off easily. Set it aside with the installation hardware.
STEP 7:Using the 7mm socket remove the 2 screws with the large washers holding the front of the center console in place.
STEP 8:Pull the center console up and turn it to expose the cigarette lighter assembly. Using the screw driver pry the tabs connecting the electrical connectors from the cigarette lighter then twist and pull out the light. Alternatively, you can use a Philips head screw driver to unscrew the lighter from the console and simply slide the entire unit out.
STEP 9:Next, you need to use the 7mm socket to remove the ALDL connector. Then use the screwdriver to pry apart the two connectors to the ECM and the two plugs from the EGI to main harness (plug # C200 in your manual). Do this bysqueezing the metal tabs on the ECM side while prying up on the plug side. It should pull right out. Although not necessary, you may want to remove the ECM to make removal easier, just loosen the four 10mm nuts on the sides. You do not need to remove the nuts completely. Finally, slide the firewall retainer clip to the left to loosen the harness.
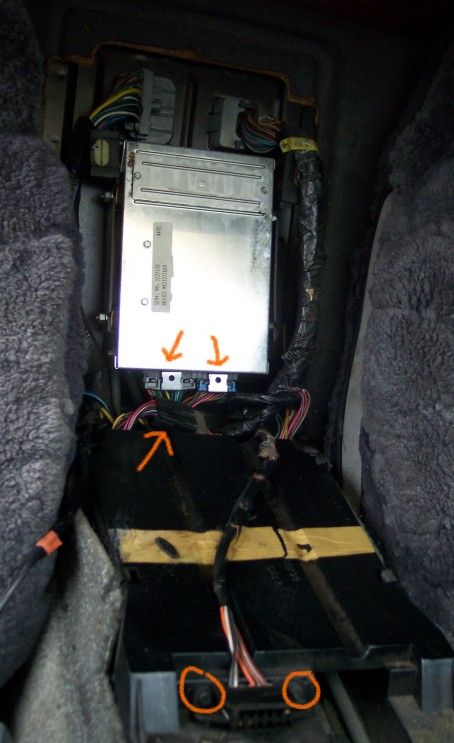
STEP 10:The entire assembly is now ready to push through the firewall. Move around to the engine bay to finish-up.
STEP 11:From the driver side of the engine bay remove the vent with a standard screw driver.
STEP 12:Remove the air cleaner by first unplugging the Air Intake Temperature (AIT) sensor on the side of your air cleaner. Then remove the 13mm nut on top of the air cleaner and unscrew the air inlet hose from the Throttle body and remove the entire assembly and set aside. Then remove the two 7mm screws holding the fuel relay in place against the firewall.
STEP 13:Now loosen the 10mm screw holding the wiring harness to the firewall. You can now pull the harness through the hole and lay the wiring on top of the engine. Now remove the radio suppression wire from the clip on the decklid and remove the two 13mm screws shown on both sides of the decklid.
STEP 14:Now on the passenger side remove the two 13mm bolts from the decklid as you did for the driver side. Also, remove the 13mm nut holding the engine grounding strap to the decklid hinge (replace the nut but just finger tighten it) and unplug the 4-pin decklid connector. Now, standing in the trunk, grab the decklid from under each side and lift straight up. If you have a helper then each of you standing on either side of the car can do the same and set it aside.
STEP 15:Staying on the passenger side let's begin with the battery wires. Use a 10mm socket to remove the top nut and an 11mm socket to remove the lower nut on the power distribution box. These are SAE nuts but you can get by with your metric set. Next use your 6mm socket to remove the plug hold-down screw and use a screw driver to pry up the tabs while you are unscrewing the screw. Now pull the plug off.
STEP 16:Now remove the battery splash guard by loosening the 7mm screw under the decklid hinge and the 7mm screw in front of the water pump. Remove the 10mm screw holding the chassis ground wire and pull the entire wiring assembly over the engine to keep out of the way. Now using your 16mm and 19mm box wrenches loosen the fuel inlet and return line connectors. It is a good idea to plug the ends with some old bottle caps or plugs to keep debris out. Pull the little vacuum hose off the end of the EGR solenoid too.
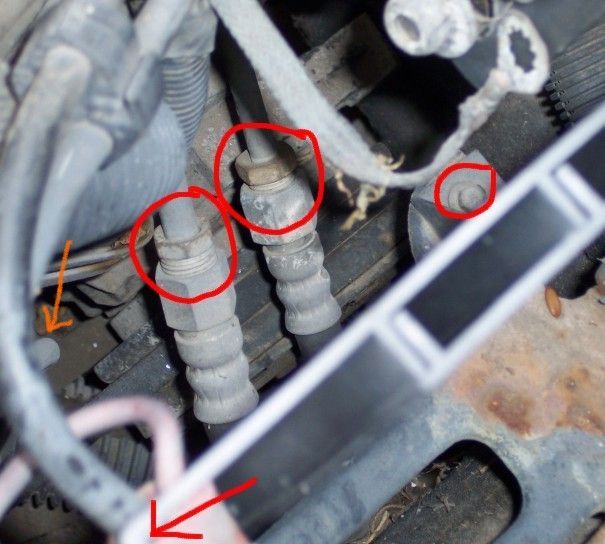
STEP 17:Now loosen the four (3 on top 1 under the vent bracket) 13mm nuts on the strut tower and remove the washers and vent hold down bracket. Now replace one of the three screws to finger tight for the time being, as in the second picture.
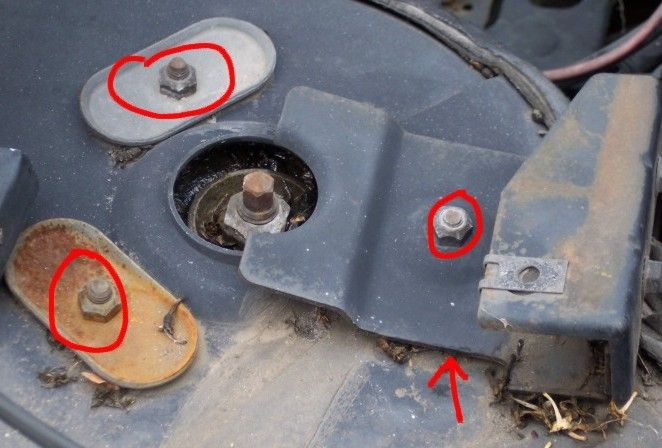
STEP 18:Now remove the 8mm hose clamp screw and remove the heater core return hose from the water pump (Note: this step is not necessary if you have a 1988 model Fiero as the heater core hose is connected to the coolant pipe under the battery and can remain connected for engine removal).
BIG TIP #5: For removing the hose use the large channel locks to break the seal. But to keep from maring the hose wrap a small piece of rubber hose or a cloth around the end where the jaws will clamp on.
STEP 19:Remove the brake booster vacuum line with a pair of pliers. Simply squeeze the spring clip together and slide the clamp back a few inches and remove the hose.
STEP 20:OK, we are done with the upper passenger side for the time being. Let's move to the rear and climb into the trunk. Use your 15mm socket and wrench to loosen the engine side Dog Bone bolt and pull it back out of the way. Pull off the two vacuum hoses below the dog bone.
STEP 21:If you have a 1988 Fiero then you can skip this step but for those of you with earlier GTs and SEs you will have the infamous blower assembly to deal with. Although it is possible to pull the engine out without completely removing the tubes it is not recommended. You have very little room and are likely to tear or scratch something for no reason. Start by removing the Cruise Control Vacuum Canister. It is held in by just one 10mm screw. Just twist it out of the way. You don’t need to disconnect the hoses unless you want to. Then remove the three 10mm nuts and screws holding the blower tube. Then remove the three 10mm screws holding the heat shield in place. Then remove the two 10mm screws holding the Alternator blower tube in place and set aside.
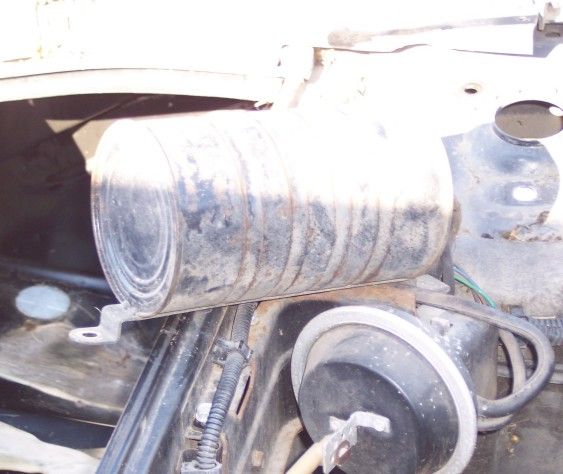
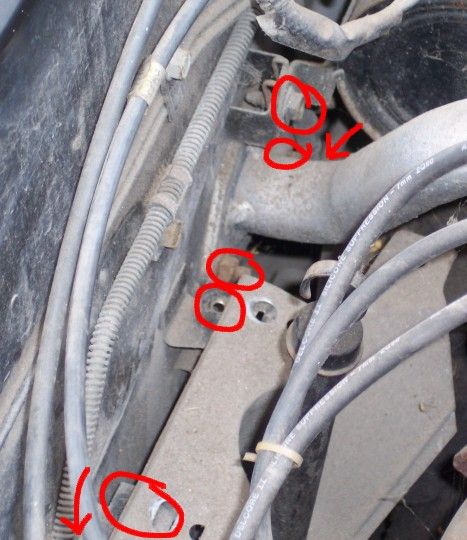
STEP 22:For AUTOMATIC TRANSMISSIONSNext you will want to remove the 10mm Cruise Control cable screw from the rear firewall and disconnect the transmission cable by pulling up on the c-clip with your pliers and using a screw driver to pry up the cable from the selector arm.
For MANUAL TRANSMISSIONS4-Speeds and 5-Speeds are not that very different but the pictures below are of a Getrag 5-Speed. You need to remove the 15mm nut from the gear selector switch and the 15mm nut from the shift selector arm. You also need to remove the c-clips from each and pull the cables out of the way (behind the deck lid hinge is a good place). Remove the two 13mm nuts holding the Clutch Slave Cylinder in place.
STEP 23:As we move around the car to the driver side we want to disconnect the tranny to chassis ground wire. It is held to the frame rail under the air cleaner by a 10mm screw. Remove it and pull the wire out of the way. If you prefer you can just loosen the 15mm nut on the block end of the wire; your call.
STEP 24:Remove the strut tower nuts and brackets as you did for the passenger side leaving one nut and washer behind finger tight for the time being.
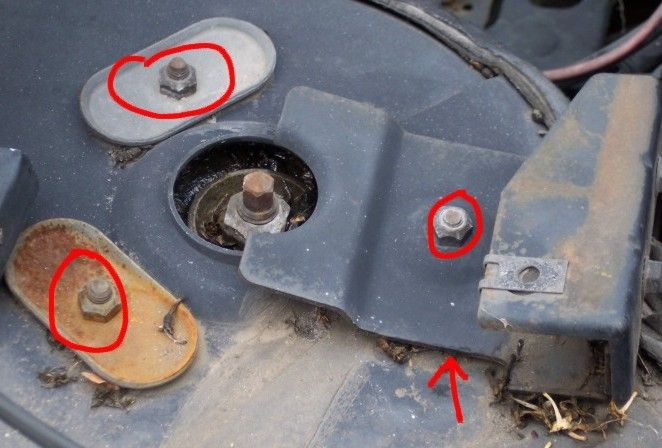
STEP 25:Disconnect the accelerator cable from the Throttle Body by pressing the plastic tabs together and sliding the cable through the bracket hole. Then pull the small metal clip off the tab allowing you to slide the cable off. Do the same with the cruise control cable if you have Cruise Control. You can leave the transmission kick-down cable alone. Be sure to slide the other cables up out of the clip on the coolant fill pipe.
STEP 26: If your AC is not discharged and you do not wish to discharge it you will need to disconnect the AC compressor from the engine. Skip Step 26 in this case.Well, you may not believe it but you are almost done with the top side of the car. You have to disconnect the AC next. This can be done in two ways and the method you choose has more to do with environmental concerns than convenience. If your AC is discharged already then this is the easiest method: using your 18" extension, remove the 10mm screw holding the AC compressor hose to the lineal chassis hose bib and pull the hose over to the engine and out of the way.
STEP 27:Loosen the rear wheel lug nuts just enough to break them free. Place the jack under the rear cross member of the K-frame and jack the car up as high as your jack will go. Place jack stands under the notched area of the floor pan jacking points. Let the car rest on the jack stands but LEAVE THE JACK UNDER THE CROSS MEMBER BEFORE GETTING UNDER THE CAR! Never take your safety for granted when working under a car. Chocks, jack stands, and a jack in combination are a good support system. Loosen the lug nuts all the way now and remove the rear wheels.
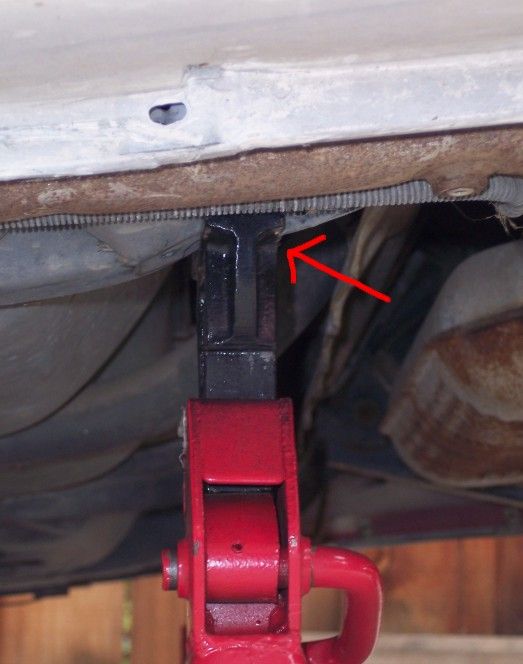
STEP 28:If you skipped Step 26 then you will need to crawl under the passenger side of the car and remove the AC compressor from the engine. To do this you must first remove the two 10mm screws holding the AC heat shield in place above the exhaust hanger springs and set the heat shield aside. Now unplug the compressor wire and using your 15mm socket and 15mm box wrench you need to remove the three bolts holding the compressor to the brackets. Once removed you will not have enough room to lift it aside so for now just use a bungy cord or rope or a wire hanger to hold it against the firewall (I hang it on the passenger deck lid hinge).
STEP 29:Now you want to get a bucket or pan because you need to remove the coolant hoses and drain the coolant. Remove the coolant fill cap the use your 8mm socket and loosen the hose clamp on the lineal tube end. Do this on both sides of the car. (Note: I have removed the wheel wells to make photographs easier but you do not need to do this)
STEP 30:Now you need to separate the mud skirts from the K-frame. They are held in by plastic rivets which don’t like being removed. If you have the "pop-pin" style rivets then just use your removal tool to pull the centers out then the entire rivet will pull out easily. If you have the type with the phillips head center pin then use your screwdriver to slowly turn the center screw out. This is more of an art than a science to you might want to work the bas of the pin with the removal tool or a screwdriver with one hand while working the screw with the other. You don't need to remove them all but take out enough to make sure that anything coming through the skirts like axles and so on can drop away. Personally, I usually remove the whole thing because if gives better access to other bolts and I can remove years of caked-up mud more easily while it is out. Again, Its your call.
STEP 31:Now disconnect the transmission cooler lines. The best way to do this is to disconnect the lower line from the tranny side and the upper line from the frame side. NOW (to keep fluid from leaking everywhere) take the upper line that you disconnected from the frame side and just shove it on the lower tranny side tube. Then take the lower tube and connect the free end to the upper frame side tube. Don't tighten the clamps. This is how you will know which goes where. You will have two loops, one on the frame and one on the tranny. The loose ends just swap with each other when you re-install.
STEP 32:Now for the brakes. I prefer to simply remove the bleeder cable since most cars I pull the engines from need a good hydraulic fluid bleed anyway so first use your 13mm box wrench to remove the hose from the strut bracket indicated by the arrow. Then use your 11mm box wrench to loosen the hose nut from the caliper. There are two compressed brass washers on either end of the hose end that you will want to replace. Now set the hose aside. There is a great hole in the frame rail that is perfect for this if you removed your wheel well. If not, just loop it behind itself.
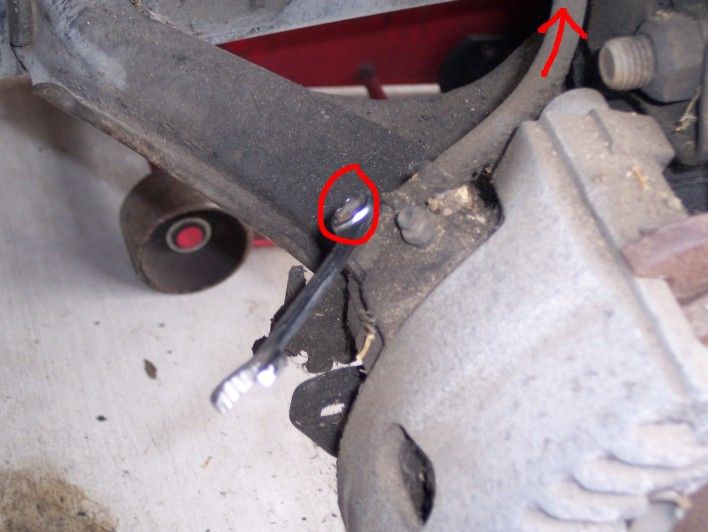
BIG TIP #6: If you can, get yourself a set of hose clamps to keep the fluid from leaking out. If you don't have any clamps, use your vise grips with some rubber tips or cloth to keep from marring the hose. Also, an old set of brake hoses make a GREAT temporary plug to keep debris out while cleaning. 
STEP 33:Now comes one the easiest yet most complained about steps of all, disconnecting the brake cable. The pictures below describe the 85-87 cable. 1988 Fiero owners skip to the description below. First, make sure the parking brake is OFF. Then pull the cable off the support clips shown:
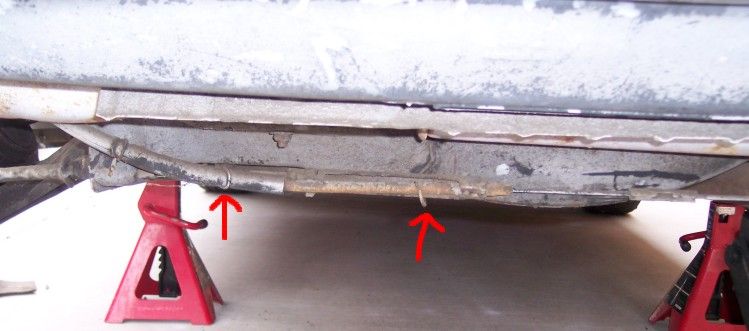
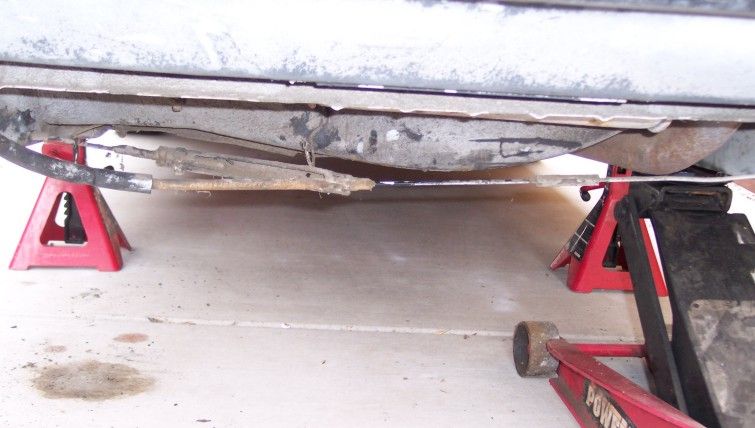
Now for my favorite trick to easy removal, grab the cable on the passenger side and pull it until it is fully extended, then clamp one of your vise grips onto the cable at the end of the tube so that it remains in tension.
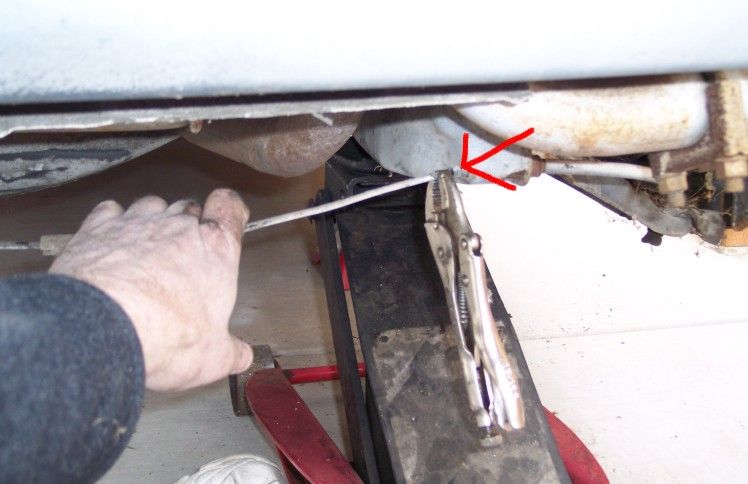
Do the same on the driver side.
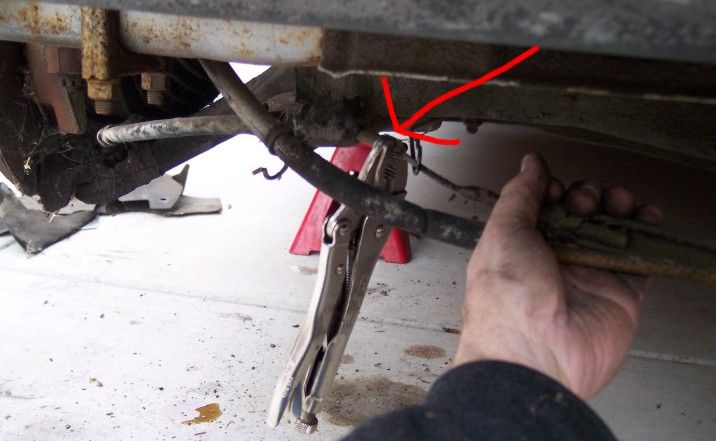
Now rotate the cable splice around to reveal a small tab that holds the cable ends in place. Use your thin screw driver to pry up VERY VERY slightly. Too much will snap it off, not that that matters too much since under tension it won't come apart on you down the road. But I hate breaking things and you don't need to bend the tab much at all to make the cable end slide free. Now just slide the cable end out!
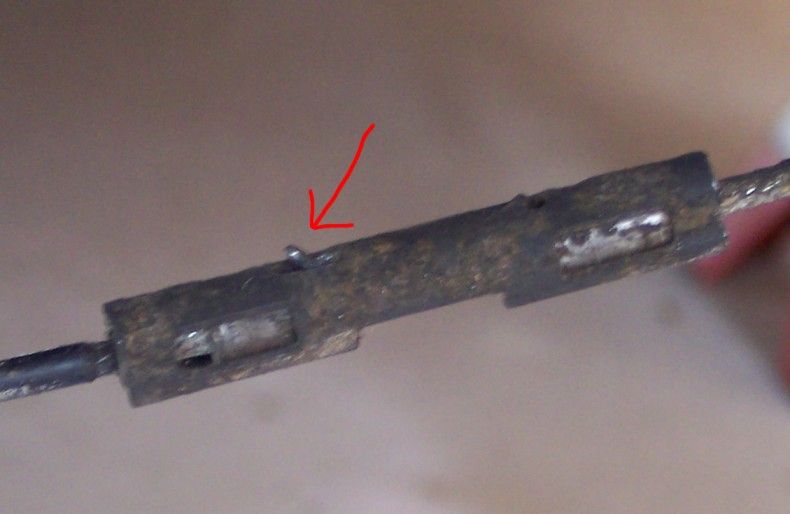
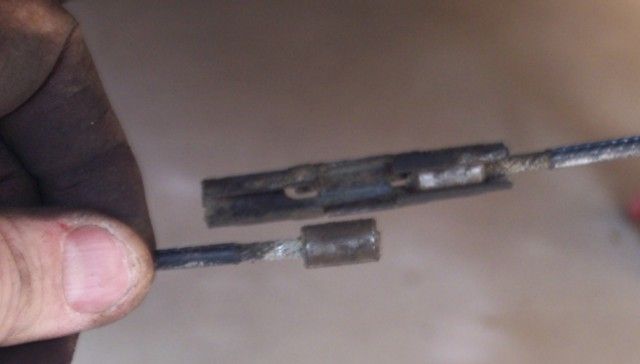
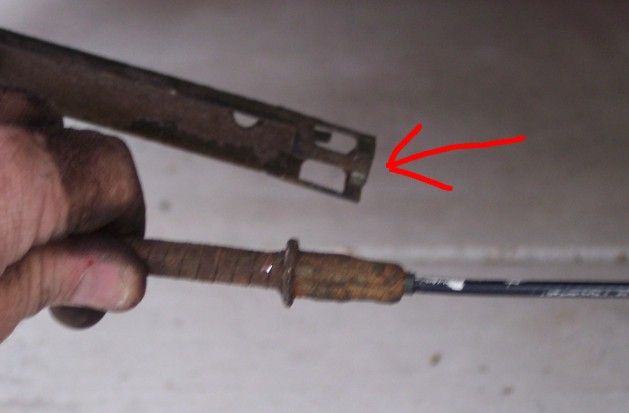
And finally push the whole cable through the adjustment wheel. Remove the vise grips. This method took me just 48 seconds. The beauty of it is that when you put the engine back in you don't have to adjust your brake. It is already set exactly where it was before!
STEP 34:WE ARE CLOSE! Next you want to use your 15mm socket with the breaker bar to loosen the rear cradle bolts. If you live in dry climates you can use a little penetrating lube or WD-40 and you'll be fine. If you live in the rust belt then you may not be able to remove the bolt without breaking the nut loose on the other side. In this case, try SAXMAN's method listed on Page 2 of the thread. Then you want to use your 18mm socket and box wrench to remove the front cradle nuts and tap the bolt through part way. Use plenty of penetrating lube or WD-40 here. This is the part where you are going to wish you had compressed air!
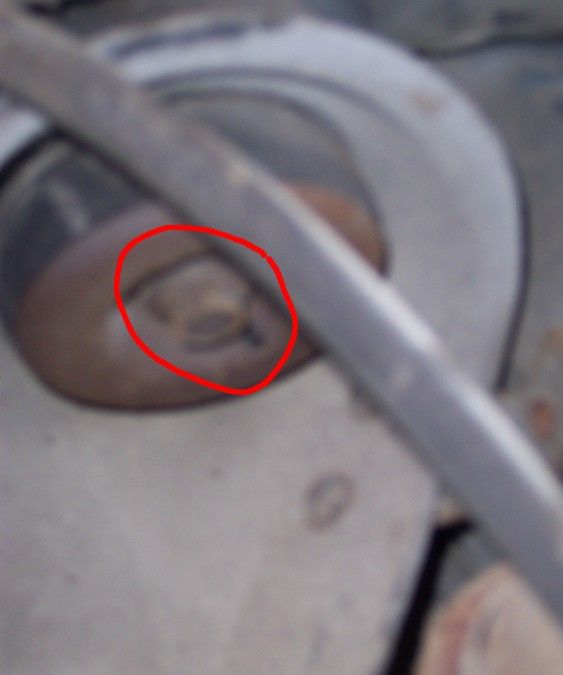
STEP 35:Now you want to place the dolly under the K-frame. Make sure you push it far enough forward to not interfere with the floor jack when you lower it but no further. Now lower the car onto the dolly.
STEP 36:Place your cherry picker in back of the car and connect it to your trunk latch. Make sure you give yourself enough slack (about 5 or 6 links) because when you lift the car you do not want the boom arm to crack the fiberglass of your rear clip.
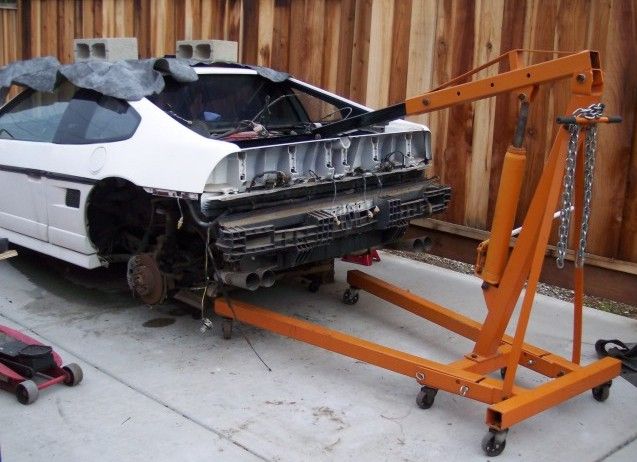
BIG TIP #7: I have heard of only one failure of a latch being ripped out by the weight of the car before, thrid party. So I do not know if it actually happened or not or what the circumstances of the failure might have been. However, aside from the anecdotal evidence that my Golden Gate Fiero Club colleagues and I have collectively done this about 50 times without incident, I did a few calcs and here is the math;
The latch is made of 1/4" round steel with a solid pressed button to the base plate. The shear strength on this piece is not known but it MUST be more that the shear strength of the surrounding sheet metal which is as follows: the shear strength for the average spot weld of .8 mm sheet metal is 900 lbs each. The rear trunk support bracket of the Fiero has no less than 8 spot welds. Then you have the two Grade 8 M6 bolts rated to 1,600 lbs each or 3,200 lbs for a 2,860 pound car. In theory, you could lift the entire car up off the ground by this latch. And with the engine out and the front wheels on the ground the weight you are actually lifting is considerably less. The only ill effects of this procedure are that the latch tends to bend up slightly making the decklid stick up when closed. The solution is quite simply a single hammer blow to the latch. The mounting screws also allow for some adjustment. If you want to do this more than once you can also just do as I do and keep a spare latch that I use just for lifting so I don't care that it is bent.
Further reading for the safety conscious:
http://www.esabna.com/EUWeb...dbook/592mig11_9.htm
http://www.rigging.net/Bolts.html
Now having said all this I should also point out that the world is not a uniform place, if your car has fewer spot welds than my car, rust, latch defect from the factory, or if you are struck by a bolt of lightning I AM NOT RESPONSIBLE!
Any automotive work involves an element of risk and this procedure is no different. You will read some posts by other forum members in the thread who offer alternative lifting procedures and you should treat each one the same as mine, with sober consideration before choosing one and attempting it. And you should exercise all due common sense and safety protocols.STEP 37:Now is the time to remove those two strut tower nuts and washers you left on earlier. Next, remove the cradle bolts. Start with the rear bolts then move to the front. You can start lifting the car with the cherry picker just a few inches to take the weight off the cradle bolts so they come out easily. I often lift the car up with the cherry picker and then grab the notchie or GT roof line and pull down with one hand while twisting the bolt free with vise grips. Be patient. They will come out.
STEP 38:Now you want to lift the car about 1 foot off the engine cradle and remove ONE last hose. In GM's infinite wisdom they placed one hose right under another on the coolant fill pipe making access impossible without removing everything around it. So I prefer to just wait to this stage of the process and disconnect it from the firewall. The arrow points to the impossible to reach location and the circle points to the now easily accessible location. NOW is also a great time to move the AC compressor aside if you removed it earlier. Hoist it up out of the way and strap it off to the deck lid hinge mount.
STEP 39:The last thing to do is double check all of your hoses and wires to make sure nothing is still connected.
STEP 40:Jack that sucker up making occasional checks for clearance and obstructions.
STEP 41:Wheel the engine out the side. Move the jack stands further back along the frame rail and lower the car onto them.
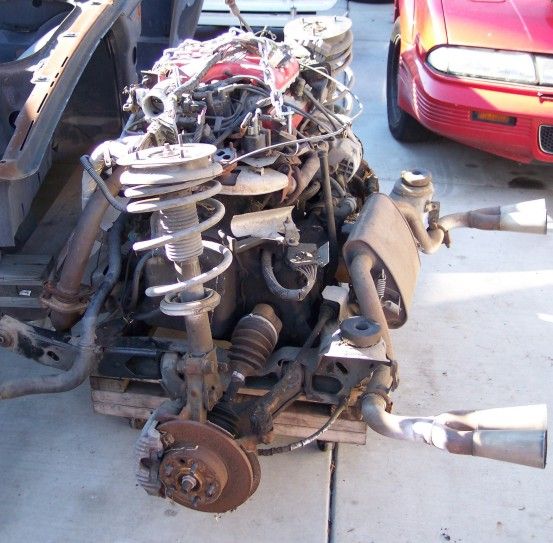
STEP 42:Have a beer!

[This message has been edited by Toddster (edited 09-28-2019).]