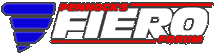

 |
Spark plugs in aluminum head (Page 2/2) |
|
crashyoung
|
JUL 25, 03:13 PM
|
|
Tighten till stripped, back off a quarter turn There are many torque wrenches, get the right one for the job.
|
|
|
Monkeyman
|
JUL 26, 03:41 AM
|
|
Like most everyone else said, bottomed out plus another 1/8th turn. If it makes you nervous, recheck it every once in a while. I don't think I've ever used a torque wrench on ANY spark plugs in any car/truck/motorhome/bike I've ever had. Haven't had one come lose yet.
|
|
|
jaskispyder
|
JUL 26, 07:49 AM
|
|
yup, I am just keeping an eye on it, as I normally don't torque spark plugs, but these alum. heads... well, I really don't want to strip it out.
|
|
|
Marvin McInnis
|
JUL 26, 02:19 PM
|
|
quote | Originally posted by jaskispyder:
Anyone have tips on installing sparkplugs in aluminum heads?
|
|
Tip #1 - Use anti-seize (good advice for any threaded connections involving dissimilar metals and/or metals subject to corrosion)
Tip #2 - Use a torque wrench (even if you have to spend $20 for a low range, 1/4 inch drive model at Harbor Freight)
Tip #3 - Most important! Derate (reduce) the amount of torque you apply to allow for lubrication of the threads by the anti-seize. The "book" torque value is for clean and dry threads unless stated otherwise. Each anti-seize is slightly different, but the one I use (NeverSeez) is typical and the manufacturer says to reduce fastener torque up to ~35%*. That means, for example, if the clean-and-dry torque value is 10 ft-lb (120 in-lb), with their anti-seize you could obtain the same results using as little as 6.5 ft-lb (78 in-lb). This derating is especially important when working with aluminum threads, which have substantially less shear strength than steel.
When tightening by hand, almost everybody applies too much torque rather than undertorquing, especially at low torque values.
FWIW ... I, too, don't trust most torque wrenches at the low end of their adjustment range, where errors can be as high as 100% of the setting.
* The fastener torque coefficient or 'K' factor is the parameter of interest here. The K factor varies with different materials, their surface finish, condition, cleanliness, and lubrication, but a typical K value for clean, dry steel fasteners is ~0.2. The NeverSeez data sheet indicates a K value of only 0.13 when it is applied ... thus indicating that a reduction in torque of up to ~35% is appropriate when using their product. (0.13 / 0.2 = 65%) Why do I say "up to"? Unfortunately, thread friction is only one factor to consider; there is also substantial friction between the face of the fastener (i.e. the face of the bolt head or nut) and the part, where anti-seize may or may not be present. What to do? I usually just derate published torque values by a semi-arbitrary 20% for steel-on-steel when using NeverSeez. When it's a steel/aluminum situation, I tend to use a more conservative 30% reduction in torque. It works for me, but YMMV.[This message has been edited by Marvin McInnis (edited 07-26-2012).]
|
|
|
crashyoung
|
JUL 29, 03:45 PM
|
|
I have had three boat engines over the years, and each one had a spark plug hole repaired with heli-coil. I use heli-coil in many applications with aluminum, as the resulting threaded hole is stronger and resists stripping or galling. But the proper torque is always preferred.
|
|

 |
|