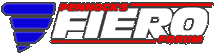

 |
What is a good Dodge 318 Small block for racing? (Page 1/2) |
|
AL87
|
OCT 24, 06:03 PM
|
|
Im looking for a 4 bolt main, with thick cylinder walls. stock, not aftermarket. 1 piece rear main seal. and if possible a serpentine drive belt system.
engine will be prepped as a street/strip car. seeking to make about 1hp per cubic inch of displacement.
|
|
|
weaselbeak
|
OCT 25, 06:45 PM
|
|
I always liked the 318. Oil pan is flat surfaced all the way around, and in my old van you could pull it down to access the crank without having to raise the engine. You can pull the intake without pulling the distributor. They made decent power and mileage. I never thought it was a great candidate for high performance, as I've seen quite a few lose the lower end. I've been told the crank seats are suspect for strength, by dirt track racers explaining why they aren't run there. But the several I've had in stock form I've really liked.
|
|
|
Tony Kania
|
OCT 25, 07:48 PM
|
|
So not knocking you, but damn, you ask some of the strangest question. 
Tony
|
|
|
weaselbeak
|
OCT 26, 09:34 AM
|
|
Mopar 318 Engine - Cheap as Dirt 415 hp from a Street 318 From the January, 2007 issue of Popular Hot Rodding By Steve Dulcich
One man's trash is another's treasure, and when it comes to bottom feeding in the world of Mopar engines the 318 seems like the biggest bargain in town. Know for efficient grocery getting in modest transportation, the musclecar aura never kissed the 318. Though the 318's long production run began in 1968, poised perfectly to participate in the height of the musclecar era, it was only available as a two-barrel economy until the deep dark days of the smog era in 1978. Without the cool reputation as a powerhouse like the bigger 340, 318s are routinely plucked from all manner of Chrysler products, and are practically handed out for haulage in Mopar circles. Be that as it may, there are some true 318 devotees in the Mopar world, impressed by the efficiency and long service this loyal mill provides.
So what's wrong with the 318? Obviously, it's a little light on displacement, but not compared to some more highly revered engines of the past-302 Chevys or Boss Fords, for instance. The most commonly heard objection is that the bore is small, creating shrouding that hurts flow and makes big power impossible, since at 3.91-inches it's not quite at the "magic" 4.000-inch mark. Yeah right-tell it to the LS1 crowd. Those engines are known for their breathing despite an even smaller bore. With Mopar's factory 18 degree valve angle, this is pretty much a moot point for most street builds. The fact is a 318 can be the basis for a nice small-displacement, high-rpm powerplant. With its short 3.31-inch stroke, high rpm are natural. A case can be made for a small-displacement street engine that's fuel efficient by virtue of its modest size, but piles on the power on demand when needed, by winding the revs up the scale. With the 318 Mopar as a base, such an engine can be built for a ridiculously low price. Better still, you will always be the underdog, and there is nothing like talking smack when putting the hurt on the big boys with a "lowly" 318.
Our goal was to build a hot street engine, using the attributes of the factory package to its best advantage, keeping the build as cheap as practical. All 318s use long 6.123-inch rods, though the 1973 and later engines had the stronger but heavier 340/360 forgings, which are better. These later rods are stout from the factory, and toy with engine speeds on the order of 6,500 rpm, and even a little more. Nearly all 318s came with cast cranks, and here again the factory stuff can take 6,500 rpm handily. In fact there is nothing in the stock engine that can't work exceptionally well in that rpm range, including the lubrication system, electronic ignition, and even the production valvetrain. I guess you can fairly say that these engines are all 6,500-plus-rpm screamers just waiting to be unleashed; here's how we did it.
The Build Low compression is a drawback of any 318, with all of the factory pistons dwelling deep in the hole at TDC. The low-cost remedy here is a set of KB 167 flat-top pistons, which allow for a zero deck with minimal milling. We had the guys at Precision Speed and Machine, in Bakersfield, California, punch our virgin 318 block 0.040-inch over, to 3.950-inch (getting close to 4.000-inch there, aren't we?), and then zero deck the block. With this overbore, the 318 grows to 324 cid. This minimal level of machining prep will usually be all that is required to build a hot street 318. We used a 273 steel crank in our engine, only because we found it in the dirt at the local boneyard, but any of the factory cast cranks are more than up to the job. To complete the short-block, we had the rods reconditioned with new Pioneer bolts, and used a factory windage tray, as well as a homemade sheetmetal baffle in the pan to prevent oil slosh. A summery of bottom-end mods is a pretty short list, basically all we did was put the flat top pistons in, milled for zero deck, balanced it, and put it back together with all re-conned factory stock stuff. Moving on to the top-end, here is where you might expect to find the secrets to making the big power put down by this little engine. Well, normally a really trick set of heads can work wonders, but here we just used a boneyard set of plain old 360 Mopar smog heads. After all, few guys will cap a $500 short with a $1,500 set of heads. All of those '70s-80s 360 heads essentially carry the same port layout of the high performance 340, and as far as run-of-the-mill production iron of the era, they are about as good as it gets. In fact, these old-school heads have a big advantage over the later castings. The pushrod constriction is much less intrusive than that found on engines spawned in the hydraulic roller era, far less than even the Magnum heads of the '90s. The bottom line is that these 360 heads have plenty of intake port for a very stout 318.
All of the 360 Mopar heads came from the factory with 1.88-inch intake valves, 1.600-inch valves at the exhaust, and big open chambers, at 72cc. To step things up, we started by having the heads machined for 2.02-inch intake valves. Some weird urban legend has it that 2.02-inch intake valves will not fit a 318, or that bore notches are required. Actually, even a standard-bore 318 will swallow valves of this size, so no problemo for our 0.040-over mill. After the seat machining, the heads received a little porting, consisting of a basic bowl blend, and some work at the pushrod area. Far from an all-out effort, these heads got little more than a swizzle of the carbide cutter-not even the ugly guide bosses were cut. These modifications may not seem like much, but it was enough to tap well into the potential of the castings, and produce respectable flow (See: Flow Chart). To reduce the chamber volume for our small displacement engine, the heads were milled fairly heavily to 60cc.
Tallying up so far we had a stock short with flat-tops, and a set of milled junkyard heads with bigger intake valves and very modest porting. It may not sound like much, but this is good stuff for a 318 build. The next consideration was the camshaft. Here we gravitated towards a hydraulic flat tappet, which may not be romantic, but is certainly budget conscious. A solid flat tappet certainly would have offered even more rpm potential, but a hydraulic allows us to use the factory valvetrain. While the OEM valvetrain is non-adjustable, and looks as low-tech as it gets, it is extraordinarily lightweight, and being a shaft system, it's as stable as it comes. With a hydraulic cam, the ugly stock stuff will out-rpm virtually anything from the aftermarket.So what's wrong with the 318? Obviously, it's a little light on displacement, but not compared to some more highly revered engines of the past-302 Chevys or Boss Fords, for instance. The most commonly heard objection is that the bore is small, creating shrouding that hurts flow and makes big power impossible, since at 3.91-inches it's not quite at the "magic" 4.000-inch mark. Yeah right-tell it to the LS1 crowd. Those engines are known for their breathing despite an even smaller bore. With Mopar's factory 18 degree valve angle, this is pretty much a moot point for most street builds. The fact is a 318 can be the basis for a nice small-displacement, high-rpm powerplant. With its short 3.31-inch stroke, high rpm are natural. A case can be made for a small-displacement street engine that's fuel efficient by virtue of its modest size, but piles on the power on demand when needed, by winding the revs up the scale. With the 318 Mopar as a base, such an engine can be built for a ridiculously low price. Better still, you will always be the underdog, and there is nothing like talking smack when putting the hurt on the big boys with a "lowly" 318.
Our goal was to build a hot street engine, using the attributes of the factory package to its best advantage, keeping the build as cheap as practical. All 318s use long 6.123-inch rods, though the 1973 and later engines had the stronger but heavier 340/360 forgings, which are better. These later rods are stout from the factory, and toy with engine speeds on the order of 6,500 rpm, and even a little more. Nearly all 318s came with cast cranks, and here again the factory stuff can take 6,500 rpm handily. In fact there is nothing in the stock engine that can't work exceptionally well in that rpm range, including the lubrication system, electronic ignition, and even the production valvetrain. I guess you can fairly say that these engines are all 6,500-plus-rpm screamers just waiting to be unleashed; here's how we did it.
Mopars have another advantage, and that is the 0.904-inch tappet diameter, which translates to about 8 percent more intensity at the valve with a cam designed to make use of the large lifter diameter. COMP has just the cams for the job, with their Mopar-only XEHL series. This is a variation of the popular Xtreme Energy cam series, but built to provide the additional intensity the 0.904-inch lifters allow. We went with the smallest of this series, the XE275HL, specing out at 231/237-degrees duration at 0.050, and 0.525-inch lift, on a 110 degree lobe separation angle. This duration level is enough to give a noticeable chop at idle, but not temperamental enough to make you insane in day-to-day driving. To cope with the aggressive rate of this cam, we used a fairly significant level of spring load for a flat tappet, deciding on a set of COMP 972 single springs installed at 1.750-inch, for 140 lbs on the seat and 310 lbs over the nose.
The final aspect of the build to consider is the induction, and here past experience has taught us that there is no beating an Edelbrock Performer RPM AirGap in the street range up to 6,500 rpm. That much was a given, but motivated by ultimate cheapness we bolted-on a TransDapt adapter plate, which allowed us to mount a factory Mopar ThermoQuad carb. The TQ carb is actually a fine unit, and the one we used is the larger version rated at 850 cfm of airflow, though an 800-cfm unit was also OEM equipment. That may seem like a huge amount of carb for a 318, but an odd characteristic of the TQ is that it allows monstrous capacity to work on seemingly impossibly small combinations. Finally a set of TTI headers with 1 5/8- to 1 3/4-inch primaries were obtained to handle the exhaust, and we had our combo. On paper, it seemed pretty tame, a flat-top piston 318, with mildly reworked iron 360 smog heads, a hydraulic flat tappet, an Edelbrock two plane, a stock four barrel, and headers. We knew better.
Running The Numbers When we brought our 318 to Westech Performance Group for testing, the attractively detailed 318 Mopar drew some interest, and naturally a few questions about the combination. We revealed it was a 318, basically a factory short-block put together with KB flat-tops and a hydraulic flat tappet, mildly ported ordinary factory 360 heads, and the four-barrel setup with the ThermoQuad visible to all. By the specs, it didn't seem like much, especially being "only a 318", so there was some serious doubt when we confidently stated that it should make over 400 hp. After all, mildly reworked 318s don't make that kind of power, especially with some junkyard heads. Well, it didn't take long to silence the skeptics, when the engine was broken in and then loaded against the brake for the first power pulls. With out baseline combination, the engine zinged-up the rpm scale to make 400 hp at 6,200-6,300 rpm.
We could see that the 318 was doing exactly what we expected-making lots of power and rpm. We could also see from the dyno sheets that the factory ThermoQuad carburetor was running at least a point too rich, and it was time to make a decision. There were a few things we wanted to try while on the dyno, and we only had one day reserved for testing, and about half of that was already eaten just setting the Mopar mill up on the dyno, and getting our baseline figures. Experience has taught us that playing with the ThermoQuad could easily soak the rest of the day in tuning, so we decided to substitute a Mighty Demon 750-cfm carb, primarily for its easy tuning changes. A 1-inch open spacer was used to mimic the 1-inch adapter that had been necessary with the ThermoQuad. With some quick jet changes of the Demon to get our mixture in the bullseye, we had 406 hp showing at the same 6,200-6,300 rpm peak.
Inside, the engine still had its fill of 20-50 conventional diesel oil used for break-in. We figured the little Mopar mill had gotten over the critical flat tappet cam break-in period by now. There was the potential for a little more power with the oil change, so we switched to Lucas 5-20 full synthetic oil for our next series of runs. The synthetic offers a lower viscosity, and presumably lower friction, which we hoped would result in some additional power by a reduction of parasitic drag. The oil change proved to be a positive step, with output now reaching 412 hp at the exact same power peak.
Dyno operator Steve Brule suggested we might gain some additional power by swapping the 1-inch open spacer for a tapered combination spacer. We grabbed a 4150-sized HVH SuperSucker spacer from our shelf, and made the change. The SuperSucker provides a tapered entry from the carb into the plenum; with some combinations this can add incrementally to the output. It proved to be the case with our 318 Mopar combination, taking peak output to 415 hp at 6,300 rpm, which would prove to be the best numbers of the day.
Our 318 cam delivered a rated 0.525-inch lift with 1.5:1-ratio rockers. Under the valve covers we were running the stock Mopar hydraulic rocker valvetrain, which we just cleaned and re-used, including the stock solid bar 5/16-inch pushrods. Although this non-adjustable valvetrain looks crude, test after test has proven it to be remarkably capable in hydraulic cam applications where adustablility is not strictly required. These stamped-steel rockers are lighter than anything from the aftermarket, and the ingenious shaft-mount system lets the rockers ride with virtually no clearance on broad bearing surface at the lower half of the rocker, sliding on a film of oil much like a main bearing. Friction at the shaft is virtually nil, and the stability is excellent. Still, we wanted to see if a little more lift could be added with a higher rocker ratio, so we swapped to a set of aluminum 1.6:1 roller rockers. This would get us to 0.560-inch lift.
The rocker change didn't work out, and in fact, the engine's effective rpm range dropped dramatically, down to 6,100 rpm, as compared to the easy and clean 6,700 rpm ceiling (the limit of our test range, not the engine's rpm capabilities) with the factory stock 1.5:1 rockers. We tried setting the lash to zero, to curb lifter pump-up, but it didn't help. What went wrong? In my experience, there are definite limits to how much intensity can be used with a hydraulic lifter, be it a flat tappet or roller. We were over that line with our overall combination.
With the super-quick 0.904-inch cam lobe profile, even with the 1.5:1 rockers we were already reaching a very high lift when considering the overall duration. As previously noted, these "0.904-profile" lobes are about 8 percent faster than high intensity 0.842-profile lobes, and the high-ratio rockers add another 7 percent. At the resultant 0.560-inch lift on a 231 @ 0.050 lobe, with only 275 rated seat duration, the valve action is well into the range of a very aggressive solid roller, far faster, in fact, through the early stages of the valve event. The result is valvetrain instability, which the hydraulic mechanism of the lifter cannot cope with. We've been through it before, and increased spring load will do little to help the situation. Besides, with longevity in mind, our COMP No. 972 springs were at the limit of loads we'd run in a street flat tappet application. If hunting for the far reaches of hydraulic cam intensity and rpm, the direction has to be mass reduction throughout the valvetrain, including lightweight valves. The 3/8-stem street valves and now heavier rockers just weren't gong to cut it with this combination.
Should we be disappointed that the higher ratio rockers didn't work? Maybe not, since it told us that the factory stuff, when combined with the fast COMP lobe profiles, is in the upper range of the potential available. While more would definitely be possible with trick lightweight components like valves, these items are somewhat out of the budget nature of this build. It also reinforces the value of the stock Mopar valvetrain. It represents a significant cost savings compared to other makes of engines where a valvetrain swap is virtually mandatory for survival with a high performance cam. Thinking about the results, we were pretty happy with the 415 streetable hp and 6,500-plus rpm capabilities we got from Chrysler's neglected 318, especially considering how much of this engine consists of nothing more than mundane factory production parts.[This message has been edited by weaselbeak (edited 10-26-2012).]
|
|
|
rogergarrison
|
OCT 28, 10:16 AM
|
|
Being a Mopar guy mostly, Id tell you to find a 340 or 360 instead. You can get good performance and wide selection of aftermarket with 318, but same stuff fits them too. 340s can terrorize even big block cars pretty easily. The Little Red Express pickups had a mild 360 and they were screamingly fast stock.
|
|
|
Old Lar
|
OCT 28, 02:10 PM
|
|
The last 318 I had was in a 59 Plymouth Belevedere convertible which had a 4bbl and push button auto. It has a great first gear 55 mph in 1st, 95 mpg in second and ??? for 3rd. That was in 1966.
|
|
|
rogergarrison
|
OCT 28, 07:02 PM
|
|
That was the 'old' 318 Polysphere head motor. It bears absolutely no resemblence to a post 67 318 except the size. There are NO aftermarket or factory performance parts for it either. I spent 3 years looking for a single 4 bbl intake for one I had and never found one. The only performance stuff I ever found was a set of headers (NOS) that the guy wanted $2000 for. The only thing the factory ever made for them was chrome valve covers and they go for over $500 if you can find a set. If you find an old (pre 66) Dodge or Plymouth police cruiser in a junkyard, you might find a dual 4 bbl manifold.
|
|
|
AL87
|
OCT 30, 09:44 PM
|
|
Dad's 318 in his 84 van is still going after 300,000 miles. 
now my question is, the 80's were part of the fuel crisis, and I know for a fact GM cut some corners during that time and manufactured thier blocks with thinner cylinder walls to save on how much iron they used per cast, I have no idea if dodge did the same thing or not. and I also dont know which vehicles had a 4-bolt main during which years.
|
|
|
rpro
|
NOV 13, 06:51 AM
|
|
There is a company named Hughes that makes a main cap girdle for small block mopars. Chrysler never cast a four bolt main block to my knowledge. There was simply no need for it. The girdles were created in the aftermarket for the 4" stroker cranks, and even those guys admit it's a waste of money.
Why not use a 340 or 360 to begin with?
|
|
|
fierofool
|
NOV 13, 01:02 PM
|
|
Email or PM ThaDriver. He specializes in Mopar, especially the pre-computer Mopars.
|
|

 |
|