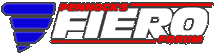

 |
Anyone know about brake lathe's? (Page 1/1) |
|
boysatt
|
FEB 11, 12:37 PM
|
|
I have a Ammco 4000 Brake lathe with the disc dual cutter. I have finally used up all the cutting bits that came with the machine and need to order more. Thing is there are so many different types of bits out there now and Ammco has different bit holders now too. So my question is whats the best to have now? My machine has negative rake bit holders now. I see you can convert to positive rake standard bits or positive rake round bits now. So which is better?
|
|
|
cmechmann
|
FEB 19, 11:23 PM
|
|
Sorry for editing again. I wasn't aware they had different rakes. I was only aware they they had different bit holder angles depending on what type of bits you are using. The slightly downward holder for the bits you can flip over, for the bits that don't have a vertical angle. The other bit holders are for the bits that have a vertical angle and can only be used on one side. I can only assume that type would be the negative rake. I don't have the model numbers memorized. But I have used the separated disc and drum and the combination disc/drum Ammco lathes over 20 years. Can't stand the on car lathes. And I prefer Ammco. A lot of the newer rotors are what I consider throw aways. I like the round corner bits. Make a better cut and can be rotated more. 12 as apposed to 6 times with the pointed. However if you are attempting to cut a lot of composite rotors with very hard disc surface, the pointed tips chatter less. On drums rounded. The pointed tips will "dig' under the hard surface with less pressure. Also with the pointed tips you should use a finishing grinder/sander to get the fine lines out completely. This would also be taking into account you have the arbor adapters for composite. I like the large adapter that looks like a machinist lathe 3 jawed chuck. Makes it much easier to get it straight the first time and the extra weight keeps noise down. Iv'e also found what wears the tips the most is the rust. Knock off as much as you can. Sometimes I will take an old crappy large flat screwdriver and use it on top of the bit holder to knock off some of the rust before turning/machining the rotor. Use common sense there. This can almost double your tip life. We order our tips through our company. They have so much Ammco equipment, they order direct. Our managers tend to try to order the cheap bits. They have cheap and good bits. In the long run the more expensive bits last longer. If I don't forget(getting old) I'll look at the boxes we have to get the article number.[This message has been edited by cmechmann (edited 02-19-2014).]
|
|
|
cmechmann
|
FEB 21, 08:56 PM
|
|
OK I was able to go over a few numbers. I assumed earlier and I was wrong. The rotor lathe we have is an Ammco 7000. The biggest difference I see between that one and yours is the cross feed controls. The bits we use have the number 1614-10. Shown as negative rack. But have rounded tips and are flippable. You have to keep in mind what I see as rounded are still the triangular tips, but the points are rounded. The other bits that I have seen, the points are pointed. Also the ones we use, if you sit them on a flat surface, the points are 90 degrees from the horizontal plane. Which make them flippable. The non flippable ones have an angle slightly out to the top of the bit point.
|
|

 |
|