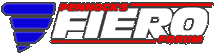

 |
Europeen style 3800 turbo swap - what do you think ? (Page 2/14) |
|
Darth Fiero
|
FEB 24, 03:45 AM
|
|
quote | Originally posted by Joseph Upson:

|
|
I would never mount an IC like that. I think you are asking for trouble (the real possibility of something hitting and damaging it). Did you have electric fans mounting on this IC that you had hanging on there like that?
Here's how I've set them up in my builds:

This one in particular had 2 electric fans mounted on it (on the topside) and a tall air deflector, the bottom of which originally sat about 1 inch off the ground. This forced the air coming under the car up into the intercooler because there really wasn’t any other way for the bulk of that air to go under it nor around the sides (because the sides of the deflector were relatively close to the tires). However, with the bottom of that deflector only 1" off the ground it did have a tendency to scrape the ground during normal driving so I trimmed an inch off of it to give a little more clearance. The deflector was mounted to its own bar which was mounted to the cradle so even if something hit the deflector, it would not have a chance of damaging the IC core unless it bounced up into the IC. In all the years I’ve run my (smaller) IC under my Fiero I’ve never had anything bounce up and damage the core in it. If I remember correctly, I think I got that air deflector off an 80's GM RWD car.
With a little more modification, an air-to-air IC with a larger core could probably be fitted in the same location. Is it the best location for one on a car? No. The best location would be up in front of the radiator, but there is no room to run charge air piping up to it on a Fiero unless you want to make some serious modifications to the chassis. The second problem is with the radiator and a/c condenser being up there already, it is crowded so there really isn't room for an air-to-air IC; nor a heat exchanger core for a water-to-air system…at least not enough to work as effectively as they can anyway.
Working with any Fiero is always going to be compromise. There isn’t as much room in these cars as most of us would like to be able to do the things we would like to do to them. Sure you can delete the A/C system and give yourself more room but I don’t consider that to be a viable option since I (and many other people) want working A/C. Even if you deleted the A/C, you still have an inherent airflow problem thru the radiator area due to the stock design of the front-end of the Fiero (which you cannot easy change without doing some rather radical body mods).
quote | Originally posted by Justinbart:
I never get more than a 16* temp rise with my air to water. That is unheard of with an air to air.
|
|
I would be curious to know exactly how you took your temperature measurements (what you used to take them and where these sensors were located) and if you also took inlet and outlet pressure readings so you could get an overall efficiency rating of the IC system you were using. Simply saying you only had a "16 deg" temp rise doesn't really tell us much. I do not doubt what you are saying but more data is needed to draw accurate conclusions.
quote | Originally posted by darkhorizon:
The plastic L36 intake has been proven to be a great performing intake... and pressure tests to well over 100PSI without issue.
I have ran a plastic intake on multiple turbo cars for years now without a single issue, and dyno proven power.... I dont see why these wannabees are coming into this thread saying you need to have an aluminum one. |
|
I don't know if I would trust an original factory L36 plastic intake. They like to crack on stock non-boosted engines, and when they do, they can dump coolant into the intake (albeit from EGR operation). Granted, an updated design plastic intake was made available later that was supposed to fix this problem but the chance of finding one in a junkyard is going to be slim and it is difficult to distingush between the two designs just looking at them. I would be concerned about the durability of that plastic when it is heat cycled + sees the wild pressure swings it is going to see in a turbocharged application. Given how many problems GM had with this plastic intake makes me question how DURABLE it will be in the long run when used with a turbo. Besides that, they don't look the greatest. If someone is going to use a FWD N/A intake, I would recommend they at least use the all-aluminum L26 intake which looks better. But the Camaro/Firebird intake looks the best, in my opinion - and it works good too. Bottom line here is you are never going to need to worry about an all-aluminum intake manifold cracking. So which one is best? That's always going to be a subject for debate since nobody wants to spend the time or money to do all the testing that would be required to prove one better than the others for every possible engine operating scenario.
quote | Originally posted by Englishrafe:
Good input from all of you. However, I'm a couple of months away from buying any of the intake system - so we'll talk plastic, aluminium, left/right facing, air/water, air/air, mounting position etc... once the engine is back on the subframe (cradle).
What are your ideas about compression ratio? Bearing in mind that in Europe I can fill my car with 95 or 98 grade fuel, should I consider going to the highest comp ratio pistons available? The 9.5:1 ones. Is this pushing it a bit with iron heads ? What are you running ? 8:1? 8.5:1? 9.5:1? Yes I know we'll come back to the inter-cooler question, but lets just say that there will be good inter-cooling.
I do have a little experience with turbo engines having raced a Renault 5 Gordini Turbo in the past. This car was not inter-cooled (draw through carburettor) and in order to boost higher, we used to decompress the engine with a thicker head gasket down to about 7.5:1. However, this made bottom end response rather sluggish. But wow did that thing fly once the engine hit 3500 rpm and the turbo really started to boost! For the Fiero, I would like to avoid burning out my tires in 4th gear at 110km/h because the turbo kicks in super hard and uncontrollably! (I remember Justin's write-up of a similar experience.)
I think that keeping a reasonably good atmospheric phase of the motor with higher compression is the way to go. Not exploding my Getrag with shock loading would also come into the equation!
Rafe
|
|
It depends on what you want to do with your car and what kind of fuel you are going to be running. The stock 3800 SC 8.5:1 static compression ratio seems to work good with the fuels we can get here in the States. You can run a decent amount of boost on 93 octane (our rating) pump gas (with an intercooled turbo setup) and then really crank it up when you dump some 110 octane fuel in. A higher static compression ratio will give your engine better off-boost performance, but this can limit the amount of maximum boost you will be able to run for a given octane of fuel which will ultimately limit the amount of total power your engine can make.
-ryan[This message has been edited by Darth Fiero (edited 02-24-2012).]
|
|
|
Joseph Upson
|
FEB 24, 06:28 AM
|
|
quote | Originally posted by Darth Fiero: I would never mount an IC like that. I think you are asking for trouble (the real possibility of something hitting and damaging it). Did you have electric fans mounting on this IC that you had hanging on there like that?
-ryan
|
|
I put the intercooler in that position to test the validity of having an intercooler in that location, after driving nearly 500 miles with more than 90% of it on the hwy between FL and GA and seeing pretty much the same inlet temps (with my IAT sensor mounted just before the throttlebody) I saw no reason to have it on the car at all as it was a greater contribution to increased weight than intercooling. If at 70 mph there's not enough air moving underneath the car to make a significant difference, how much more moderate city driving. That 6" tall core is hanging more than 2" in the expected air stream, it's more like 4". the core is 3.5" thick and 18" long.
The core facing the expected air stream is the most effective positioning and wouldn't require fans at all which would only be effective at speeds low enough to allow them to pull more air through the core than is already flowing, after that there is a risk that they may impede flow if a speed is reached where air is attempting to pass through the core faster than the fan can pull it.
Your intercooler arrangement as well as one other I saw with the intercooler angled is what inspired me to test the arrangement. If hardly enough air is moving under the car to make an impact with the intercooler hanging directly in the theoretical air stream, I can't see where an air dam in the same location will make any difference attempting to direct already non existent air 90 degrees upward into an intercooler which is a less favorable position than what I setup temporarily and so far no one has come forward with any proof (data or experience) to the contrary.
It appears I'm the only person with an IAT sensor placed just before the throttlebody and after the intercooler in order to know for sure if such an arrangement is productive. When I mounted the intercooler up front my inlet temps dropped by at least 100 deg, I posted before and after logs of those results in my 3900 build thread. I didn't post any logs on the above arrangement because I have no reason to lie about it and the fact I removed it from the car altogether should be proof enough it was worthless in that location.
There should be liquid radiator cores in appropriate dimensions available to do a great job up front depending on how much boost you intend to run and once again the heat transfer in this system should be very good even with small cores if the performance of the cars heater core mentioned earlier is any indication. I believe the fact that engines are water cooled instead of air cooled is a good indication as to how effective liquid to air cooling is as well. Ever lay on a cold water bed? I bet it'll kill you you from hypothermia if you can manage to fall asleep on one
It will be some time before I get the intended kit, install and report what I find.[This message has been edited by Joseph Upson (edited 02-24-2012).]
|
|
|
1fatcat
|
FEB 24, 10:13 AM
|
|
. [This message has been edited by 1fatcat (edited 02-24-2012).]
|
|
|
Justinbart
|
FEB 24, 10:16 AM
|
|
quote | I would be curious to know exactly how you took your temperature measurements (what you used to take them and where these sensors were located) and if you also took inlet and outlet pressure readings so you could get an overall efficiency rating of the IC system you were using. Simply saying you only had a "16 deg" temp rise doesn't really tell us much. I do not doubt what you are saying but more data is needed to draw accurate conclusions. |
|
I have the IAT sensor half way between the intercooler and the TB. After several miles of driving it will read 10-12* over ambient then an additional 16* during a long run under high boost. So if its 70* outside it will say 70* and eventually clime to 82* while cruising and 98* under boost. Then it falls back to 82* after 20-30 seconds. I'm not sure if scott has any scans of the IAT. I just watch it on the Scanmaster. I don't have an IAT sensor before the intercooler but FWIW I can tell you that the hot side is too hot to touch and post intercooler is cool to the touch.
If you are only going to be running 88 (R+M)/2) octane then I wouldn't go over stock compression. I loved having 9.4:1 in the L26 engine but I was also running E85 which is 105-110 octane. ------------------ Turbo 3800 E85 5spd spec5 11.54@132.7[This message has been edited by Justinbart (edited 02-24-2012).]
|
|
|
1fatcat
|
FEB 24, 10:24 AM
|
|
quote | Originally posted by Darth Fiero: Granted, an updated design plastic intake was made available later that was supposed to fix this problem but the chance of finding one in a junkyard is going to be slim and it is difficult to distingush between the two designs just looking at them.
|
|
Actually, it was the lower intake manifold that was redesigned. It had a smaller diameter stove pipe for the egr. The smaller pipe allowed for a larger air gap between the pipe and it's recieving bore hole in the plastic upper manifold. This hole is where the manifold would get brittle, break open to a water passage behind the throttle body and induce coolant into the intake. In some cases, this would hydro-lock the engine on start-up and bend connecting rods. The larger air gap kept the hot egr stove pipe from deteriorating the plastic upper manifold.
|
|
|
Tweeter
|
FEB 24, 10:56 AM
|
|
here on Base the fuel pumps show the Germany octane rating and the US rating. German 98 octane = US 92 Octane. I'll double check this next time i fill up my tank.
|
|
|
ckrummy
|
FEB 24, 12:26 PM
|
|
It's cost more but why not top mount like a rx7 or a Subaru, it's not ideal but it should work better than putting it under the car. you would have to modify your deck lid but it would be sweet.
 and forgive me it's an mr2 photo
|
|
|
Racing_Master
|
FEB 24, 12:40 PM
|
|
quote | Originally posted by ckrummy:
It's cost more but why not top mount like a rx7 or a Subaru, it's not ideal but it should work better than putting it under the car. you would have to modify your deck lid but it would be sweet.
 and forgive me it's an mr2 photo |
|
SHUN! :P
I was thinking an efficient way to use an intercooler would be to change the way air flows through the engine compartment. it goes from bottom up, taking out the heat via the decklid vents. Instead of having air come out the vents, pump air into them via side scoops or roof scoops. Also for this to work, you must modify the rear of the car to include air vents to create a suction on your engine compartment. If you design them right, you have constant airflow through the engine compartment, and some cool looks! You however might lose some trunk space. Then you can position the intercooler(s) under the scoops to have ram air into them.
Only downside is, if you do not design the outlet vents right, you overpressure your engine compartment and underside of the rear of the car, producing some lift and also minimalizing airflow inside of the engine compartment, leading to... lots of heat.[This message has been edited by Racing_Master (edited 02-24-2012).]
|
|
|
Englishrafe
|
FEB 24, 04:15 PM
|
|
That looks cool (no pun intended!) the high mount IC. However, in France my car needs to stay fairly original looking in order not to attract too much "cop" (Gendarme) attention. I know of a '79 Firebird that got impounded during a car meeting because of it's huge hood scoop! The guy had to thumb a lift home as the Gendarmes took all the papers and imobilised the car - no way you can talk your way round a determined (mean!?) Gendarme !!
For Tweeter: Do you know of the military base near Torgelow in norhern Germany? Apparently, that's where my motor came from.
|
|
|
Englishrafe
|
FEB 26, 05:59 PM
|
|
Here's the progress for this weekend:
Balance shaft removal

Marking up for the extra oil drain holes

Centre punching for drilling

Drilling pilot holes diameter 5mm

I forgot to take photos of the final drilling. Heres the finished valley area with it's 8mm holes. This is copied from what I've seen on the net concerning the preparation of these types of engines.

After which, I gave the block a "five minute" grind over to remove sharp edges, casting flashing and generally smooth out all internal areas for oil flow and the exterior just to make it look nice !


Still have to plug the balance shaft oil hole. I will probably do it with a small grub screw tapped into the block. Something for later on...
|
|

 |
|