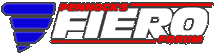

 |
Fabricating Custom Knuckles with plate steel (Page 2/7) |
|
Will
|
JAN 21, 12:56 PM
|
|
quote | Originally posted by zkhennings:
I have been looking into building a CNC and might do so in the near future, this would be a fun first project to run on the mill. Almost all of the CNCs I have seen for home use have no coolant setup, have you seen any that do? Seems to make endmills last a lot longer than just using compressed air.
I will most likely make knuckles in the near future with plate steel and I will make them customizable as Will was suggesting. Then I will know the ideal geometry and if I am unhappy with the unsprung weight I can machine them from aluminum.
|
|
The customizable design lets you set the geometry where you want it. In addition to kingpin inclination, caster angle, etc. there are many things to tune. For example, Fiero steering is very slow. Shorter steering arms would speed the steering up. If you bolt on a shorter steering arm and find that the tires scrub in tight turns, you can then just shim the steering arm to get the ackerman right... If you'd machined the knuckle, you'd have to make another new part every time you wanted to change something.
What I'd *REALLY* like to play with is a low steering offset and shallow kingpin angle combined with a high caster angle to give caster induced camber gain to help with grip in tight corners. The larger caster angle would result in a large mechanical trail, high steering effort and poor steering feel. To negate these, cut a main plate with some forlauf (leading pin) geometry to reduce the mechanical trail.
If you're a smidge smart about the steel plate design and include shims under the ball joint bosses from the beginning, then you can simply ditch the shims and install water jet cut 5/8" or 3/4" aluminum plate in place of the 1/2" steel plate.
|
|
|
FieroReinke
|
JAN 21, 01:28 PM
|
|
People over on Locostusa.com build spindle/knuckles for the locost cars quite often. Some even post plans. I have plans for a rear knuckle but I don't think I have anything for a front spindle. You might be better off finding a spindle from another car that meets your requirements and fabing new arms to that spindle. There are multiple suspension calculators for checking different spindle and pick up point combinations. The Locost guys usually use a program called "Wishbone" that is available for download. You plug in all your pivot points and dimensions and it outputs camber gain charts, roll centers, etc for differnet amounts of bound and rebound. All of this is extremely important to the design of suspension.
|
|
|
zkhennings
|
JAN 21, 01:42 PM
|
|
quote | Originally posted by FieroReinke:
People over on Locostusa.com build spindle/knuckles for the locost cars quite often. Some even post plans. I have plans for a rear knuckle but I don't think I have anything for a front spindle. You might be better off finding a spindle from another car that meets your requirements and fabing new arms to that spindle. There are multiple suspension calculators for checking different spindle and pick up point combinations. The Locost guys usually use a program called "Wishbone" that is available for download. You plug in all your pivot points and dimensions and it outputs camber gain charts, roll centers, etc for differnet amounts of bound and rebound. All of this is extremely important to the design of suspension. |
|
I have wishbone right from the locost site. I had not seen ones with custom knuckles however I will check them out
|
|
|
dobey
|
JAN 21, 02:05 PM
|
|
quote | Originally posted by zkhennings: I have been looking into building a CNC and might do so in the near future, this would be a fun first project to run on the mill. Almost all of the CNCs I have seen for home use have no coolant setup, have you seen any that do? Seems to make endmills last a lot longer than just using compressed air.
|
|
I've seen various cooling set ups on the mini mills/lathes that have been converted to CNC. I'll probably build a fogger for mine. You don't really need coolant for aluminum and other softer metals though; only really for steel and harder metals. And I plan to hook up a small shop vac to pull the chips out of the way, and bucket them for recycling.
|
|
|
zkhennings
|
JAN 21, 02:08 PM
|
|
quote | Originally posted by Will:
What I'd *REALLY* like to play with is a low steering offset and shallow kingpin angle combined with a high caster angle to give caster induced camber gain to help with grip in tight corners. The larger caster angle would result in a large mechanical trail, high steering effort and poor steering feel. To negate these, cut a main plate with some forlauf (leading pin) geometry to reduce the mechanical trail.
|
|
I have had very similar ideas to lower the offset (kingpin angle) and decrease steering arm length but I had not considered bumping the caster to gain camber. Would you then decrease camber gain from suspension compression to gain better straight line braking performance?
Also, I can see vorlauf geometry making for extremely fast steering but would the downside be crazy kickback on bumps around turns? In a straight line it would track very well and with a low offset not be disturbed by bumps very much, but when turning that must create a decent moment, how far back from the center of the wheel would the kingpin axis have to be moved?
At 8* of caster say and stock wheel tire diameter is 24.69"
Then (12.35)sin(8) = 1.719" as a rough mechanical trail length.
So would you figure if stock steering feel is fine at caster of 5* then
(12.35)sin(5) = 1.076" --> 1.719 - 1.076 = 0.643" of offset to lower steering effort to that of stock?
So I figure in a straight line this will behave similarly to 5* of caster, but around turns you get the camber gains of 8* of caster
I know the trail lengths are not exact since I used the adjacent length (tire radius) as the hypotenuse but close enough to get the idea
|
|
|
zkhennings
|
JAN 21, 02:14 PM
|
|
quote | Originally posted by dobey:
I've seen various cooling set ups on the mini mills/lathes that have been converted to CNC. I'll probably build a fogger for mine. You don't really need coolant for aluminum and other softer metals though; only really for steel and harder metals. And I plan to hook up a small shop vac to pull the chips out of the way, and bucket them for recycling. |
|
Without coolant I have gotten tons of chatter in tight radius corners where there is a lot of flute engagement (milling around 1 inch deep into 6061) and I wrecked a few parts until I went with a machine with coolant, a HAAS minimill. It also helped to use a tool path in those tight corners that did not follow the wall profile until the finishing pass
|
|
|
dobey
|
JAN 21, 03:07 PM
|
|
quote | Originally posted by zkhennings: Without coolant I have gotten tons of chatter in tight radius corners where there is a lot of flute engagement (milling around 1 inch deep into 6061) and I wrecked a few parts until I went with a machine with coolant, a HAAS minimill. It also helped to use a tool path in those tight corners that did not follow the wall profile until the finishing pass |
|
You were taking a full inch deep of material out of a 6061 block at once? You should take lighter cuts. 
The biggest problem with the cheap mini mills isn't the lack of coolant systems, but the fact that they are small and have less stability than larger and heavier mills do. If you get chatter on one, something is loose somewhere, you're hitting backlash, or taking too big a cut. Adding coolant probably wouldn't help. It might dampen the chatter noise, but it won't increase stability. Anyway, there's lots of videos on YouTube, and plenty of discussion on hobby machinist forums and such, if you want to learn more about CNC conversions for the cheap mini mills/lathes. We're starting to get a bit too off topic with it. 
When I get my machines set up and CNCed though, I'll be making some parts for Fieros, for sure.
|
|
|
zkhennings
|
JAN 21, 05:28 PM
|
|
quote | Originally posted by dobey:
You were taking a full inch deep of material out of a 6061 block at once? You should take lighter cuts. 
The biggest problem with the cheap mini mills isn't the lack of coolant systems, but the fact that they are small and have less stability than larger and heavier mills do. If you get chatter on one, something is loose somewhere, you're hitting backlash, or taking too big a cut. Adding coolant probably wouldn't help. It might dampen the chatter noise, but it won't increase stability. Anyway, there's lots of videos on YouTube, and plenty of discussion on hobby machinist forums and such, if you want to learn more about CNC conversions for the cheap mini mills/lathes. We're starting to get a bit too off topic with it. 
When I get my machines set up and CNCed though, I'll be making some parts for Fieros, for sure.
|
|

HAAS mini mill very expensive
and no I think it was doing 0.15" steps not an inch at once, but at those corners once you are in the final passes it chatters because it is close enough that the chatter at the bottom since the endmill has to have decent stick out, it causes it to chatter along the whole length.
Ive used manual lathes with no coolant on aluminum but cut depth is quite shallow
Regardless it's all moot because you wouldn't run into those conditions milling knuckles[This message has been edited by zkhennings (edited 01-21-2015).]
|
|
|
Will
|
JAN 21, 09:37 PM
|
|
quote | Originally posted by zkhennings:
I have had very similar ideas to lower the offset (kingpin angle) and decrease steering arm length but I had not considered bumping the caster to gain camber. Would you then decrease camber gain from suspension compression to gain better straight line braking performance?
Also, I can see vorlauf geometry making for extremely fast steering but would the downside be crazy kickback on bumps around turns? In a straight line it would track very well and with a low offset not be disturbed by bumps very much, but when turning that must create a decent moment, how far back from the center of the wheel would the kingpin axis have to be moved?
At 8* of caster say and stock wheel tire diameter is 24.69"
Then (12.35)sin(8) = 1.719" as a rough mechanical trail length.
So would you figure if stock steering feel is fine at caster of 5* then
(12.35)sin(5) = 1.076" --> 1.719 - 1.076 = 0.643" of offset to lower steering effort to that of stock?
So I figure in a straight line this will behave similarly to 5* of caster, but around turns you get the camber gains of 8* of caster
I know the trail lengths are not exact since I used the adjacent length (tire radius) as the hypotenuse but close enough to get the idea |
|
Caster induced camber gain only occurs when caster is greater than kingpin inclination and is only effective when there is a large steering angle... it doesn't affect more or less straight line performance like braking.
Because the center of force of the contact patch still has a lever arm equal to the mechanical trail, this is what pavement forces use to work on the steering... so I don't think it gives more kickback on bumps. BMW uses vorlauf geometry on older M3's, which run more caster than normal 3 series cars.
When a tire is generating grip but not sliding, the center of force of the contact patch is behind the geometric center of the contact patch. When the tire starts to slide, the center of force of the contact moves forward to the geometric center. If the migration of the center of force is a large enough component of pure mechanical trail (30%? 50%?), then there will be a significant reduction of steering effort when the tire starts to slide. The overall result is good "contact patch feel" and steering feedback.
|
|
|
zkhennings
|
JAN 22, 10:01 AM
|
|
quote | Originally posted by Will:
Caster induced camber gain only occurs when caster is greater than kingpin inclination and is only effective when there is a large steering angle... it doesn't affect more or less straight line performance like braking.
|
|
Yes what I meant was because you will gain more camber on turns, would you design the suspension to not gain as much camber on compression, and that would result in better braking since when the front end squats under braking the tire will remain perpendicular or close to it.
And I will check out the M3 suspension
|
|

 |
|