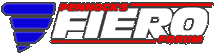

 |
Removing Broken off Bleeder Valve on 88 Rear Caliper (Page 2/3) |
|
fieroguru
|
SEP 19, 05:19 PM
|
|
quote | Originally posted by reinhart: The bleeder breakoff is below the surface so I imagine the weld is going to contact the aluminum housing as well. Would this be a problem? |
|
No issue. Aluminum and steel are dissimilar metals so the molten steel will not stick to the aluminum. I do this quite often with 88 brake bleeders, exhaust bolts in aluminum heads, and severely rusted bolds in cast steel manfolds.
|
|
|
Patrick
|
SEP 19, 05:44 PM
|
|
quote | Originally posted by Dennis LaGrua:
The way to get the old bleeder out is to remove the piston then drill it out and tap for 1/8" NPT.
Try Dorman 13915, about $7 on Amazon.
|
|
Does this require a bottoming tap, or is a taper tap sufficient?
|
|
|
Dennis LaGrua
|
SEP 19, 06:06 PM
|
|
quote | Originally posted by Patrick:
Does this require a bottoming tap, or is a taper tap sufficient?
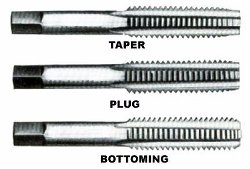 |
|
I just use a std 1/8" NPT tap in a hole drilled by an R size drill bit. You can try 5/16" but it will be tight. I guess you would call the tap I use as a plug tap. The fitting is tapered so with sealant on the threads no leaks will result. ------------------ " THE BLACK PARALYZER" -87GT 3800SC Series III engine, custom ZZP /Frozen Boost Intercooler setup, 3.4" Pulley, Northstar TB, LS1 MAF, 3" Spintech/Hedman Exhaust, P-log Manifold, Autolite 104's, MSD wires, Custom CAI, 4T65eHD w. custom axles, Champion Radiator, S10 Brake Booster, HP Tuners VCM Suite. "THE COLUSSUS" 87GT - ALL OUT 3.4L Turbocharged engine, Garrett Hybrid Turbo, MSD ign., modified TH125H " ON THE LOOSE WITHOUT THE JUICE "
|
|
|
Craig71188
|
SEP 20, 08:15 AM
|
|
If you look at an NPT tap, they are (more or less) Plug or bottoming taps. Pipe threads are tapered, so the entire tap is slightly cone shaped. I have just grabbed one at the local hardware and never really looked to confirm there were different "types".
|
|
|
DimeMachine
|
SEP 20, 09:01 PM
|
|
I have had great luck welding on a nub. Expands the steel quickly and breaks itself free, then spin it out.
That having been said, as we all know, 88 calipers are getting so scarce so be careful!! screwing one up would be a shame...
|
|
|
reinhart
|
SEP 22, 03:03 AM
|
|
Thanks for all the advice. I'll try welding first. If that fails I'll freeze it. If that fails I can try to drill it out, although I'm still confused as doesn't the bleeder need to be out to drill?
|
|
|
Craig71188
|
SEP 22, 07:40 AM
|
|
quote | Originally posted by reinhart:
Thanks for all the advice. I'll try welding first. If that fails I'll freeze it. If that fails I can try to drill it out, although I'm still confused as doesn't the bleeder need to be out to drill? |
|
Yes and no! Drill a small hole through the bleeder. Drill progressively larger till the harder bleeder material is all but gone, then drill your "final" hole to tap for the insert. You can try the larger drill for your tap right away, but the harder bleeder will tend to push it off to one side and make a bigger mess (and junk the caliper)
|
|
|
Mike in Sydney
|
SEP 22, 09:08 PM
|
|
quote | Originally posted by Craig71188:
Yes and no! Drill a small hole through the bleeder. Drill progressively larger till the harder bleeder material is all but gone, then drill your "final" hole to tap for the insert. You can try the larger drill for your tap right away, but the harder bleeder will tend to push it off to one side and make a bigger mess (and junk the caliper) |
|
I've found that if you can get a relatively large hole in the bleeder that the often come out with the aid of an easy-out. Take care not to break the easy-out because then it's a job for a spark erosion machine (https://www.youtube.com/watch?v=yEwR9ECSmSo).
You may want to try spark erosion instead of trying to drill out the broken bleeder. I used it to get rid of a broken bolt in an aluminium head on an old motorbike. Bolt was eroded away and the threads remained. Just had to clean them up with a thread chaser.------------------ Mike in Sydney
|
|
|
reinhart
|
SEP 26, 08:07 PM
|
|
There was no center bleeding hole or at least I could never get the drill to find it. I tried hitting it 3 more times with hot/cold and that didn't do anything. I tried the welding a nut on trick. The nuts broke off four times in a row at the base. The fifth I cranked up the welder to max with a really high flow. It blew out the side of the nut it was so hot. But, the nut finally held and I was able to turn it out with a wrench! I guess I needed that sucker extra hot to get the weld attached to the stub real good. I was expecting the bleeder to be easy to turn out after it started turning but it was a difficult turn until it was nearly out. The caliper survived relatively unscathed. Just a small indentation on the outside lip which won't affect the bleeder.
Thanks for all the help.
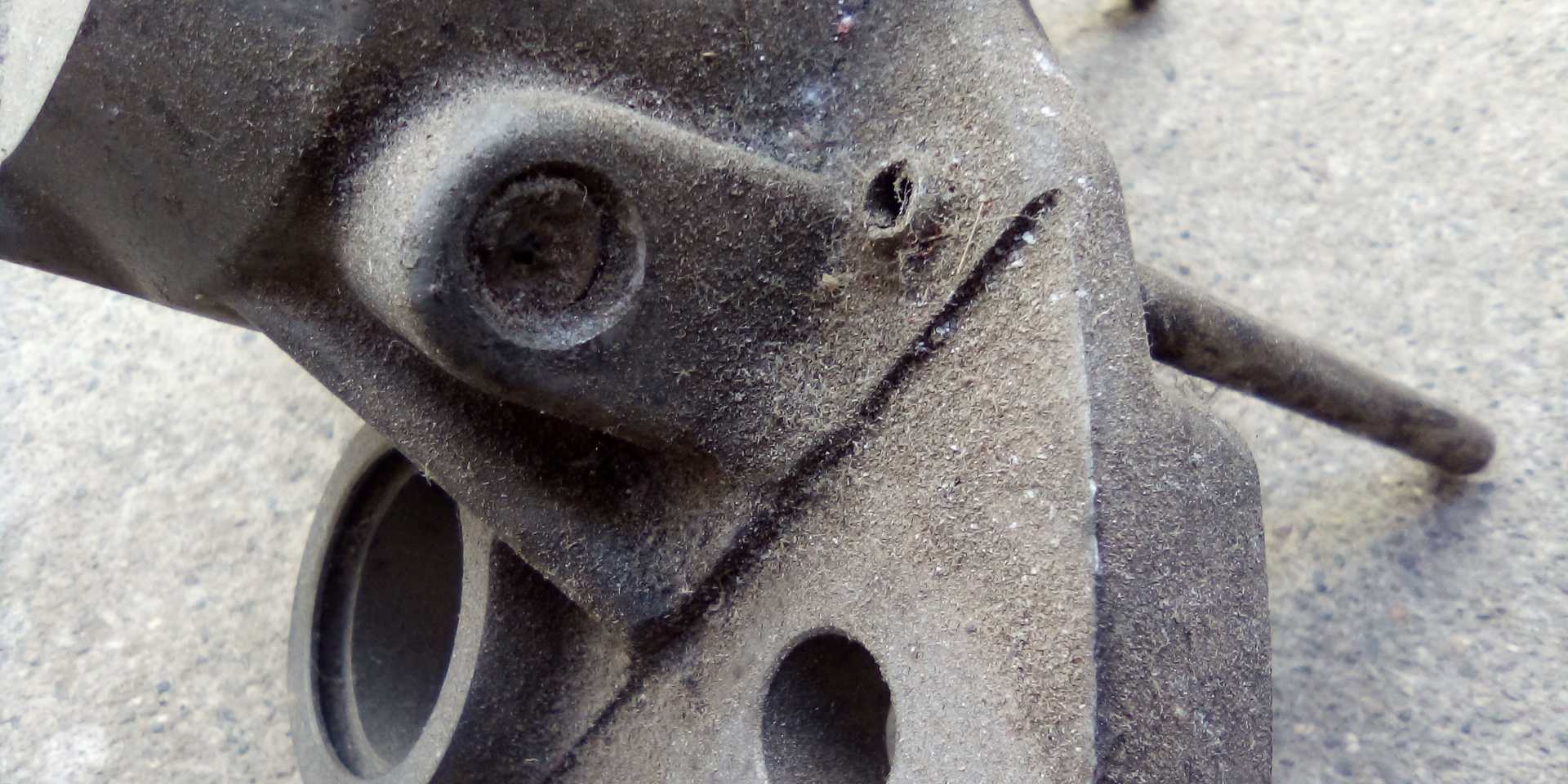
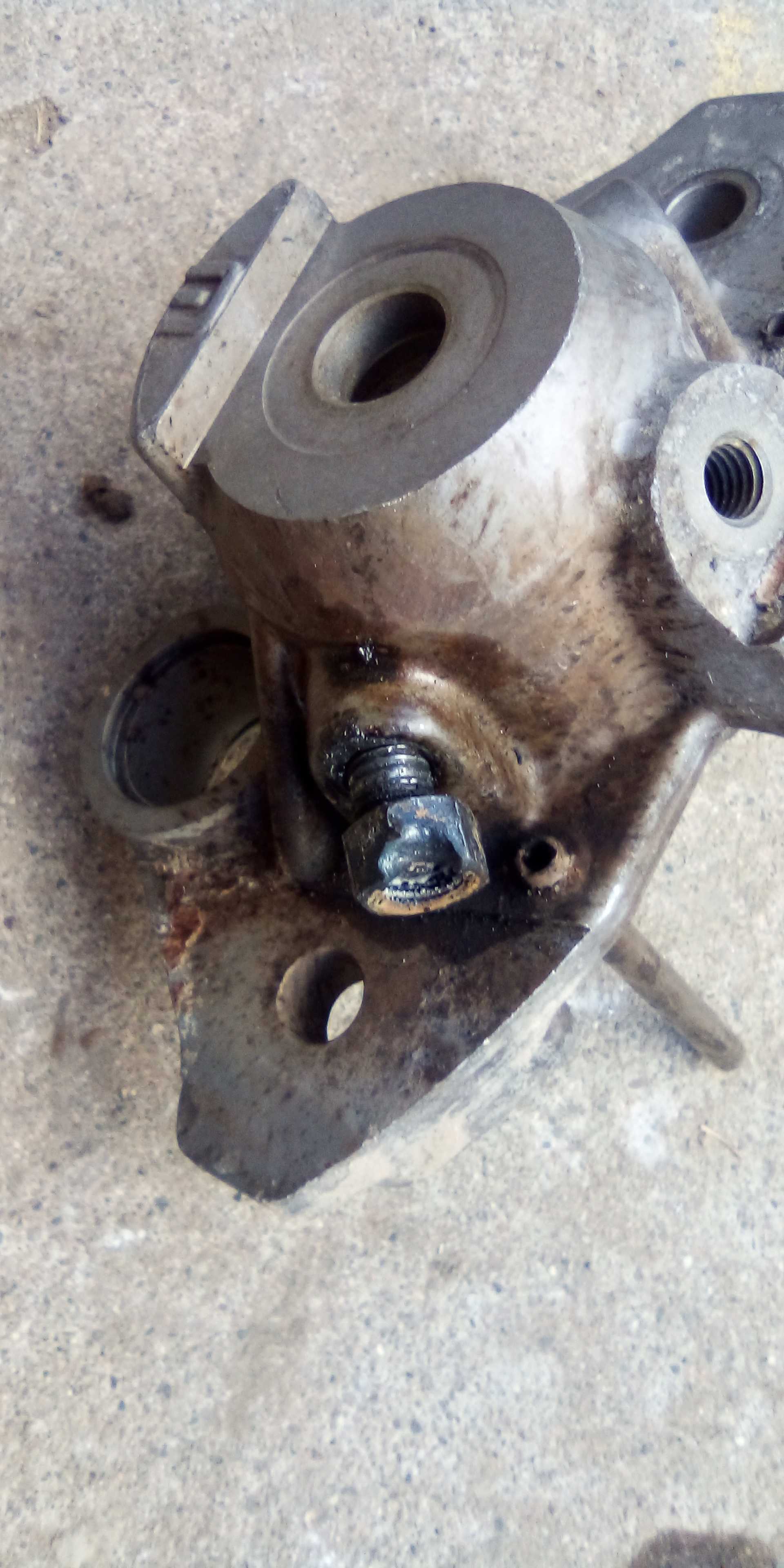
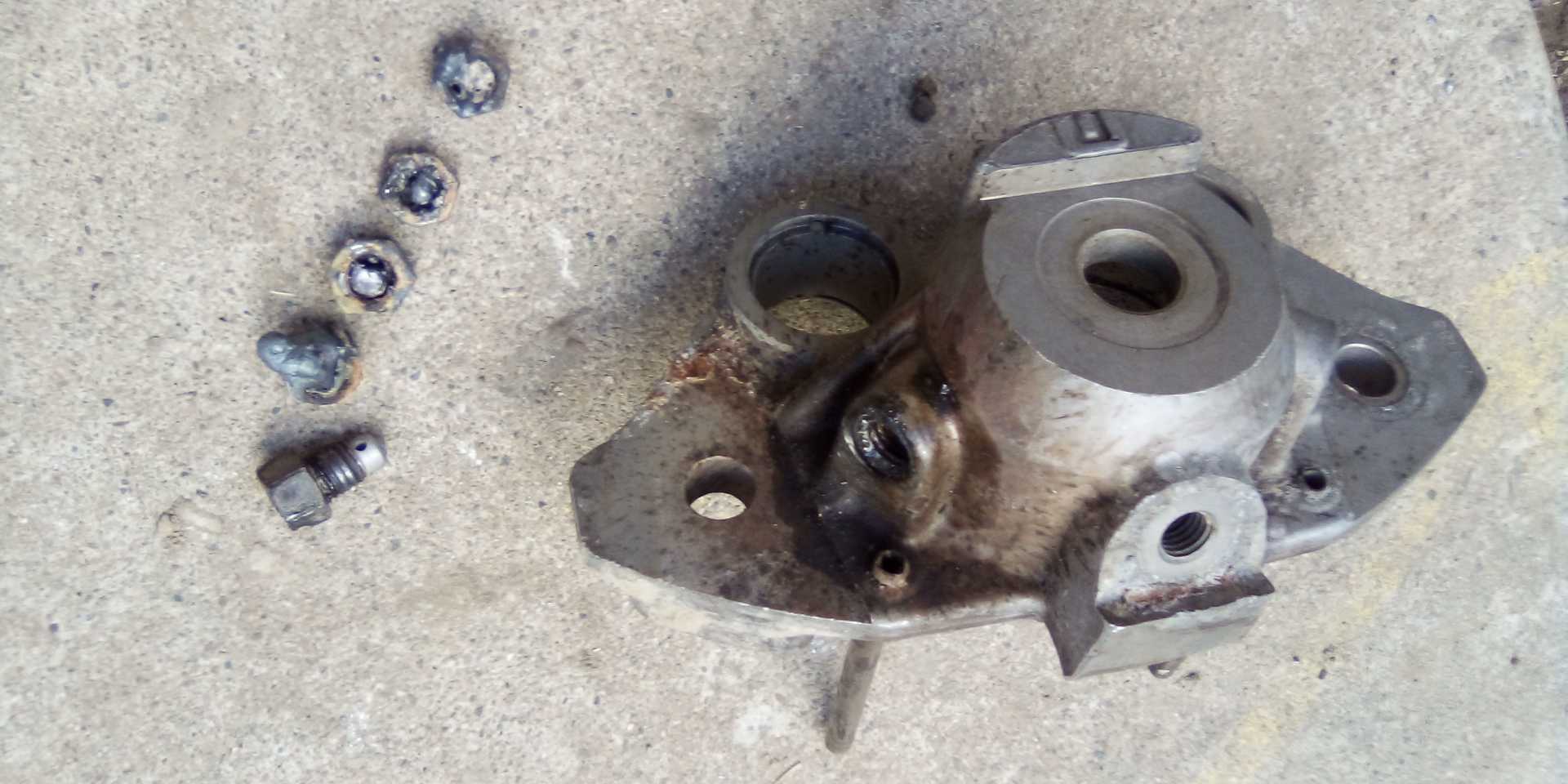
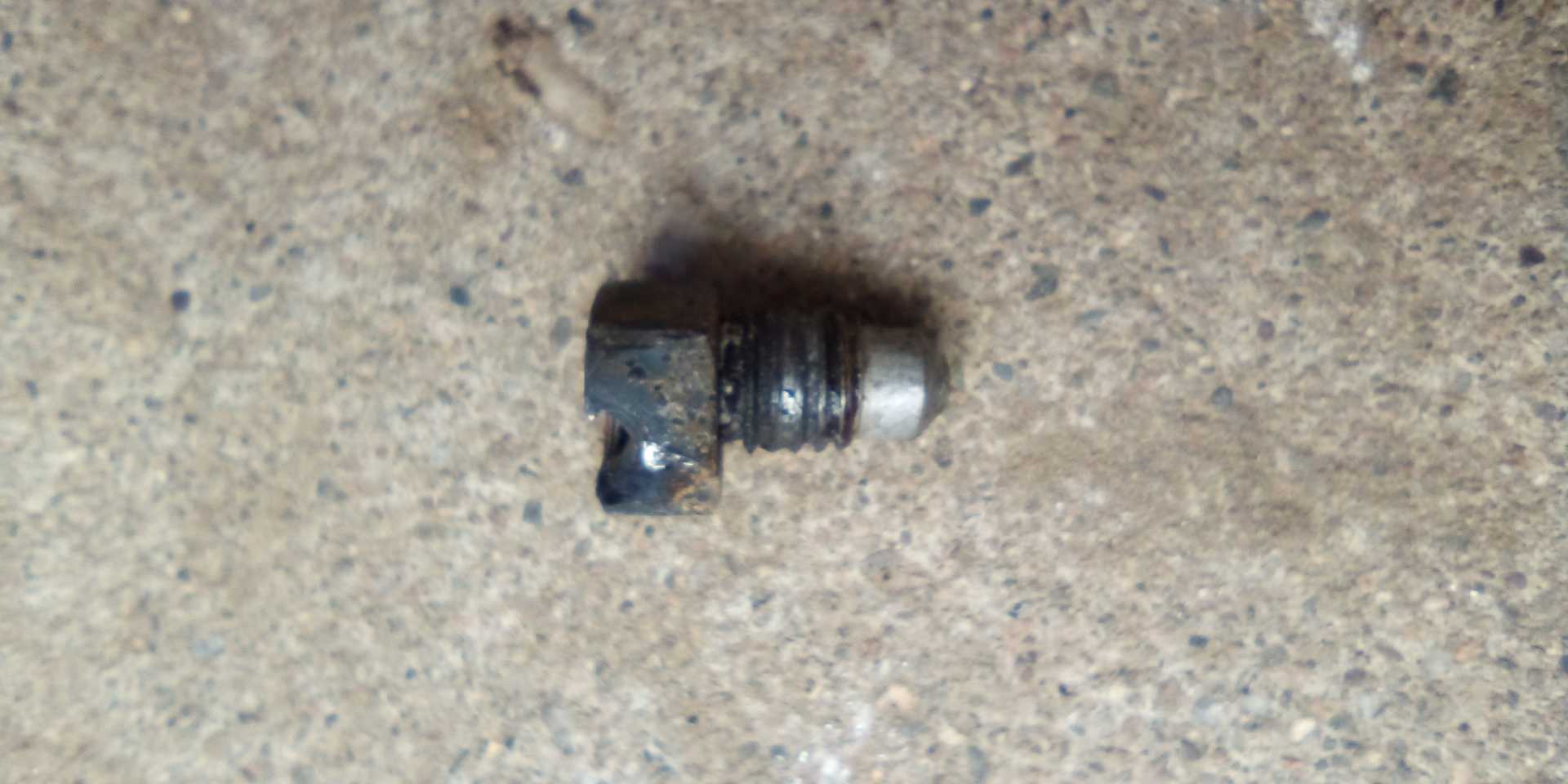
|
|
|
pmbrunelle
|
SEP 26, 08:29 PM
|
|
Good job OP, that's how it's done 
None of that easy-out stuff that gets people further into doo-doo.
quote | Originally posted by Patrick:
Does this require a bottoming tap, or is a taper tap sufficient?
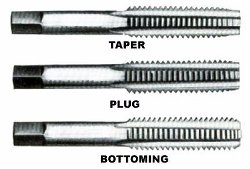 |
|
A little bit unrelated, but I generally only purchase new taper taps.
When a taper tap is used, most of the wear occurs on the tapered section that does most of the cutting. The edges on the straight section remain sharp.
Therefore, when I have a worn-out taper tap, rather than throwing it away, I cut off the tapered tip (with an abrasive cut-off wheel), leaving me with an almost brand-new bottoming tap. I touch up the end on the bench grinder. Less waste, and it allows me to have a more complete tool collection, with little extra cost.
Sometimes, on a single job, I started the threads with a taper tap, then I chopped off the end to complete the holes.
|
|

 |
|