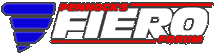

 |
Best long lasting exhaust manifold gaskets (Page 2/3) |
|
MaxxPower1968
|
OCT 28, 06:09 PM
|
|
quote | Originally posted by A_Lonely_Potato:
I wound up taking off my A/C bracket, but i do not remember if it was in the way for anything. There are only those 3 bolts. |
|
I decided to remove the bracket, too. I figured since this is my first time doing this job, I should get as much out of the way as possible. It will make it easier to assess every option to any problem (hopefully none) that might arise. Thanks.
|
|
|
MaxxPower1968
|
OCT 28, 06:16 PM
|
|
quote | Originally posted by Patrick:
Other than not having the luxury of a garage, this sounds very much like my adventure several years ago, posted Here. It was by far the worst experience I have ever had in over 50 years of working on my vehicles. |
|
Hey Spoon and Patrick, thanks for sharing your horror stories with me. I'm hoping to avoid the same issues but at least I know that if I do run into prolems, I can reference all your previous solutions. Oh, and now I'm petrified to even get started with the header removal, lol (and shaking in my boots).
I'll let you guys know how it goes. I'm waiting for a few things to get delivered so it may not be until next week.
|
|
|
MaxxPower1968
|
NOV 02, 11:46 AM
|
|
Here's a quick update... (actually pretty long)
I was able to remove both manifolds without breaking any of the bolts. That's the quick part.
The long part: I noticed most threads on removing the bolts only suggested spraying PB Blaster multiple times for a few days and letting it soak in with a few hopes and prayers that none of them would snap. Well, I decided to do whatever I could to give myself any advantage over just crossing my fingers.
A Little Backstory: A while back I was rebuilding the suspension on my Ram truck. It's an '04 and I bought it new. The ball joints were shot and needed to be changed out. That means the rotors and hubs, and spindles had to come off. I knew that the brake rotors had never been removed because when it finally came time to do the brake jobs, I could never remove the rotors , they were welded in place from all the rust that accumulated for 18 yrs. I fought them, hammered them, heated them, and cursed at them but nothing worked. I was just about to give up and go to a shop when I came across this video.
https://www.youtube.com/watch?v=StGnq7vMV5A
I already had a cheap air chisel from HF that I used to changed some A-arm bushings on my camaro, so all I needed was the hammer head and the HF water sprayer. A quick search on Amazon and they were delivered in a couple of days. The driver side was the toughest and took about 10-15 min but it finally came off. The others were a little easier. That video is the real deal.
Back to the Fiero: I decided to try this method out on the manifold bolts. I had already sprayed penetrating oil for about 4 days. It could have possibly been the reason I didn't snap any but I wasn't going to leave it up to chance at the time. Besides, I had already broken two off at the manifold to Y-pipe flange using just the oil. So I grabbed my air chisel and started going to work on the trunk side bolts being really careful not to damage the tubing. After about 20 min of quick hammer pulls and water spraying, I decided to check the bolts. THEY WERE LOOSE. It took no force to spin them by hand with just a socket on an extension. I thought to myself, either this method really works or they were loose to begin with and that's why I had an exhaust leak. I really should have checked them first. Anyway, I chose to believe that it worked and went ahead and started planning my attack on the firewall manifold.
First a Disclaimer: This is by no means a tutorial or "How to". This is only a "this is how I did it and probably got lucky".
You can cause major damage to your manifolds, scratches, dents, or even holes.You could break off a bolt head if you don't hammer them squarely. The bolt heads will get deformed and you might not be able to get a socket or wrench on them. I had to use all my arsenal, 6-pt, 12-pt, and even spline sockets to be able to grab onto some of the heads. I also had rounded nut removers ready just in case but lukcily I didn't need them.
Here we go: The first thing I did was get some protection for the manifold. It was tough to stay square to the bolt head and not slip off. I knew that I was going to be in awkward positions and would not be able to secure the air hammer confidently with two hands. I went to Lowe's and got a couple of steel plates from the construction area, I only used one of them though. Next time I might just get one the length of the header and maybe 1 inch or so less on the width. I wrapped it in duct tape so it wouldn't scratch anything too much. It seemed to work out ok. Zip ties were used to secure the plate in place.
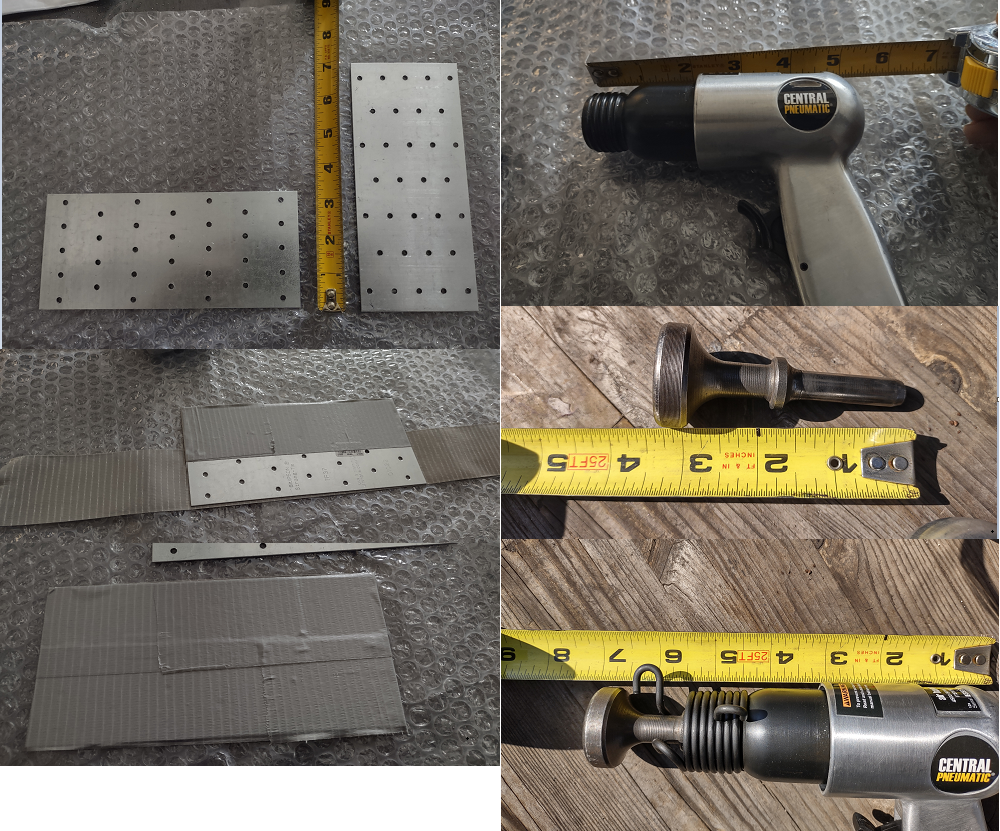
I also needed a short barrel air chisel/hammer(could be called either) due to the tight space between the firewall and engine. I ordred a Cambell hammer from ebay but I got antsy and didn't want to wait 2 more days so I took a shot at HF and they had a one for like 15 bucks with a coupon. It ended up being the same length (5.25") as the Cambell. I also used my shortest hammer head. Total length was just hair above 7 inches, which was just barely short enough to get in there. One more inch shorter or one more inch of space would have been way better. Cylinder #2 bolts were the most difficult followed by the top stud on #6 due to the added length. I had to use a small squirt bottle to spray. Another set of hands would have been really nice so they can spray the water for me. Having to get my hands and arms in and out every couple of minutes to spray, hammer, spray, and then hammer again was very tiresome. I ended up with a ton of scratches on my wrists and forearms.
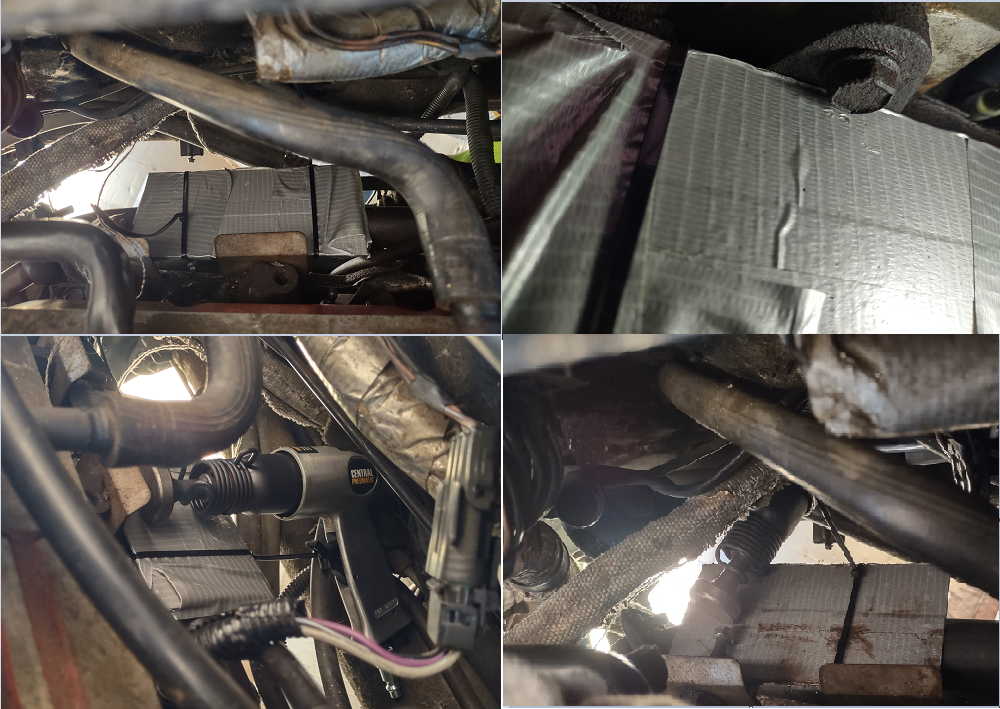
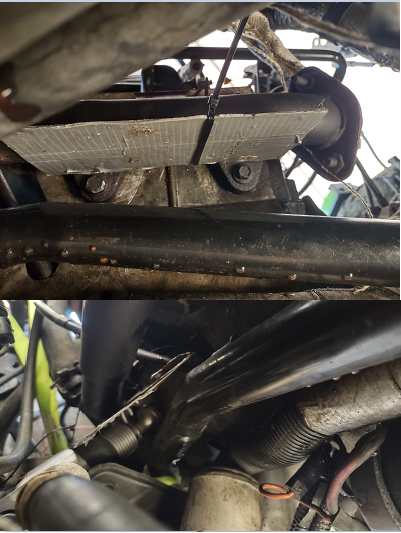
The Findings: All kinds of bad found on the heat shield. I don't see why anyone would install this, especially without gaskets on both sides. Horrible design IMO.
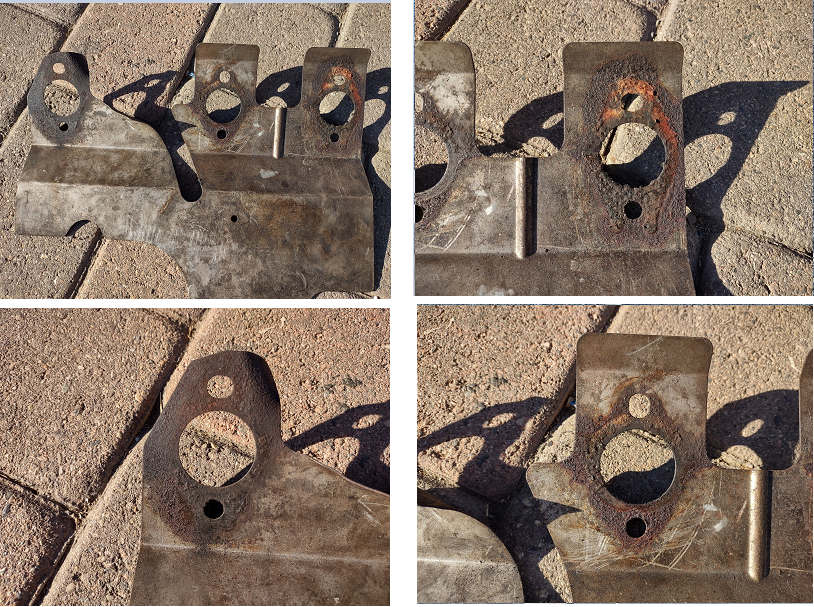
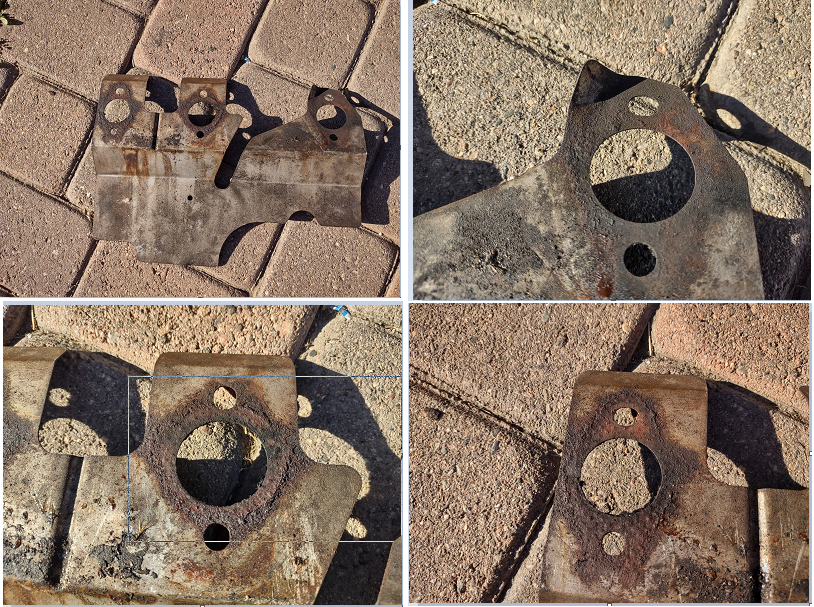
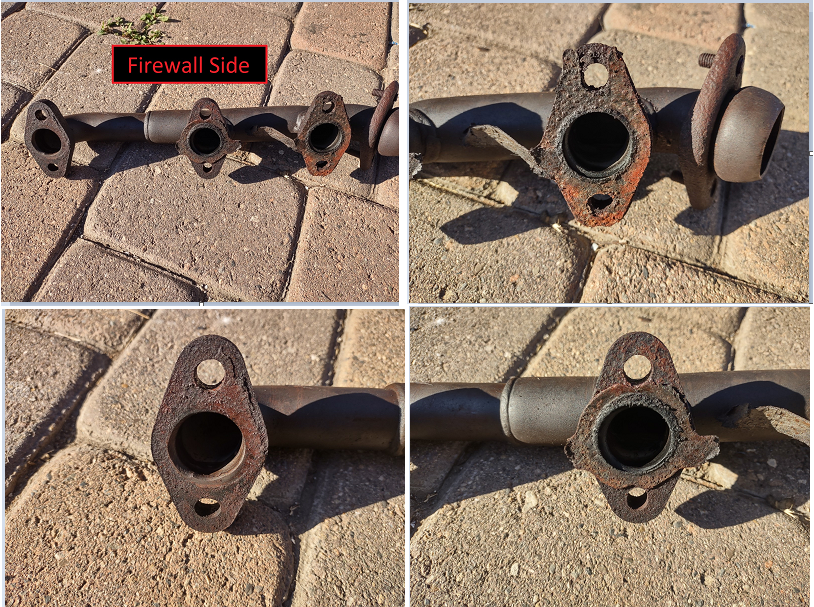
The bolts were in pretty bad shape. A few of them had a lot of rust and one of from the trunk side was even missing some threads. I feel some probably would have broken off if I had left it up to chance. Again, maybe it was just luck and not the hammering but I would definately use the hammer again if I felt the need.
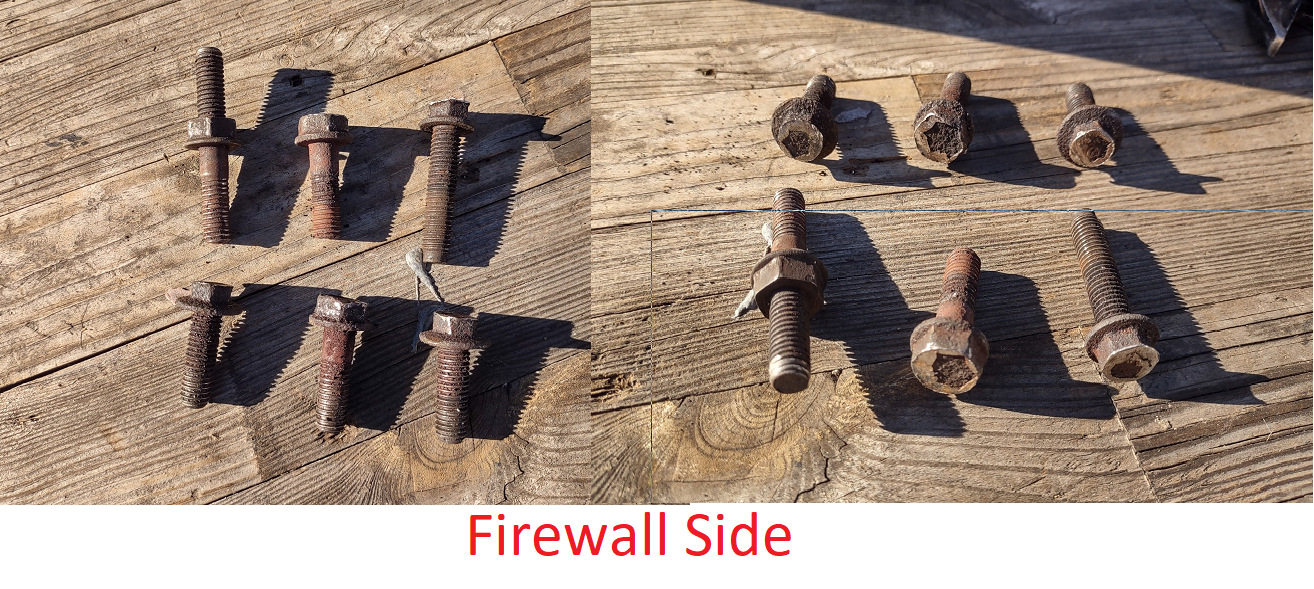
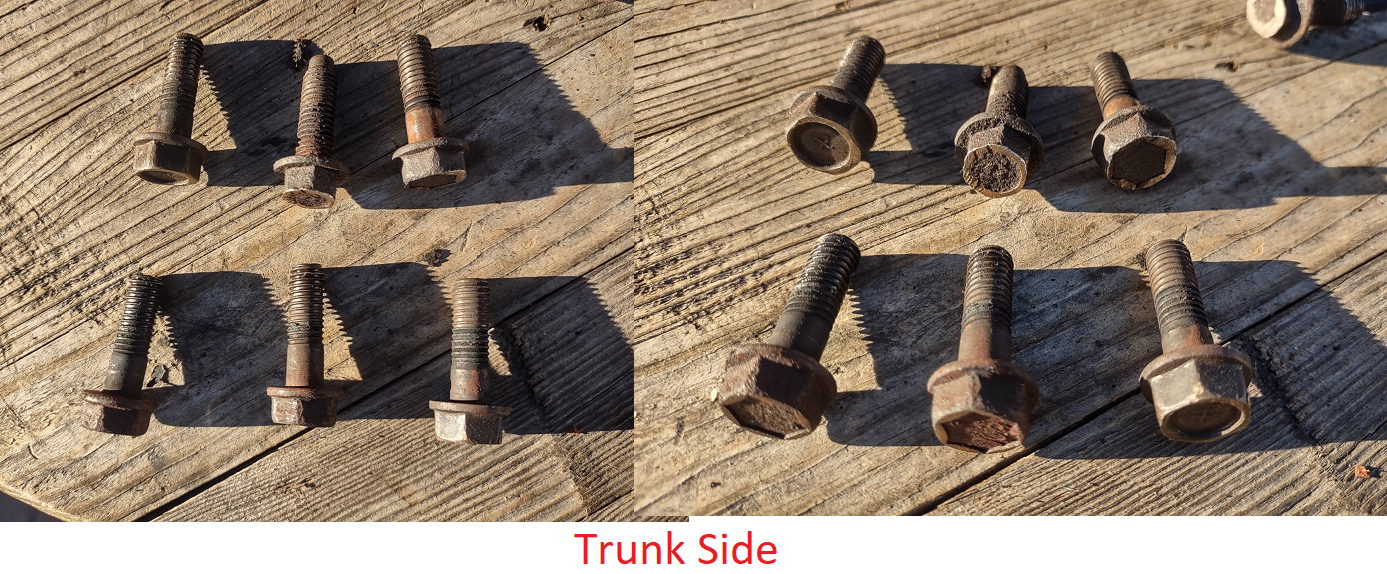
|
|
|
A_Lonely_Potato
|
NOV 02, 01:13 PM
|
|
check those logs for cracks!
|
|
|
MaxxPower1968
|
NOV 04, 01:58 PM
|
|
Thanks A_Lonely_Potato. I checked over the manifolds. The trunk side header looked pretty good.I didn't see any signs of leaks or cracks. The flange seal areas didn't show any obvious signs of leakage.
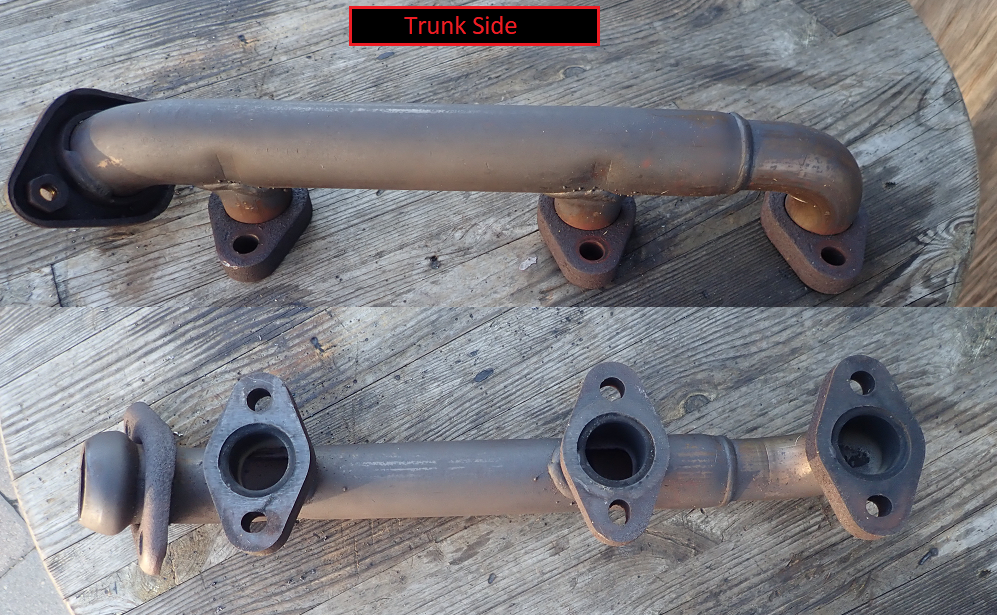
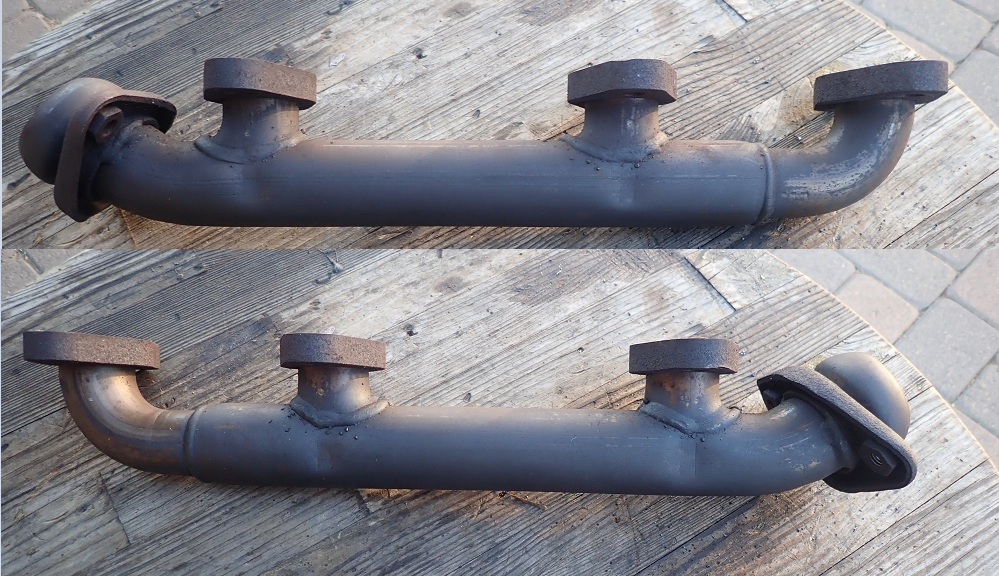
The firewall side, on the other hand, wasn't as pretty. There's a really ugly previous repair that I'm going to have to grind off. It's just too ugly. t doesn't look like it's leaking but it's possible that all pressure was already exiting from the heat shield areas. You can see the crack on the inner flange weld. My plan is to grind off the ugly weld, weld all the flanges and then port the insides. I'm still waiting for Rodney's header jig so I'll have to play the waiting game for a few more days before I can get started.
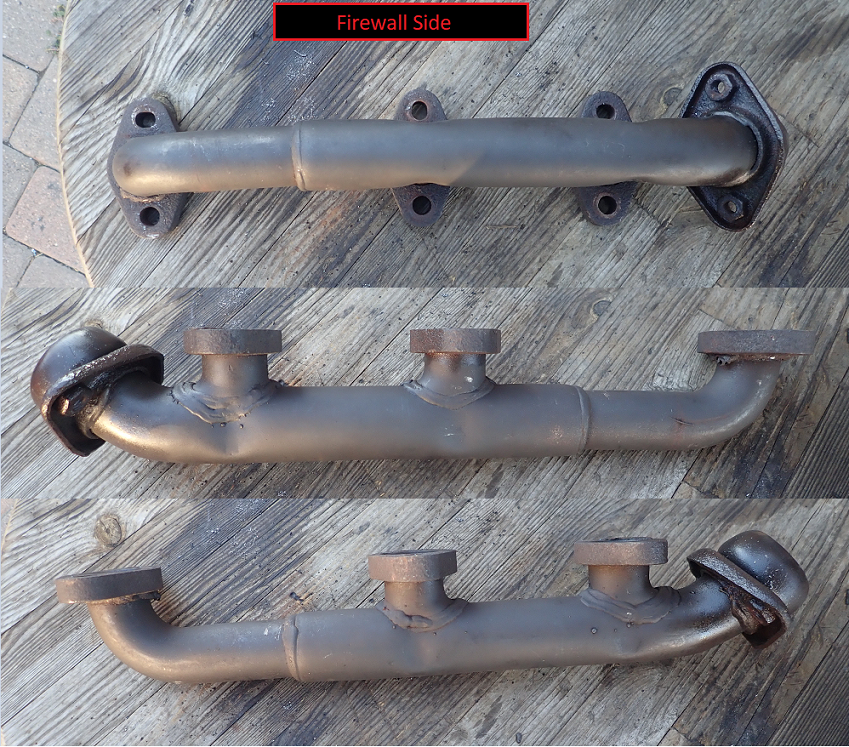
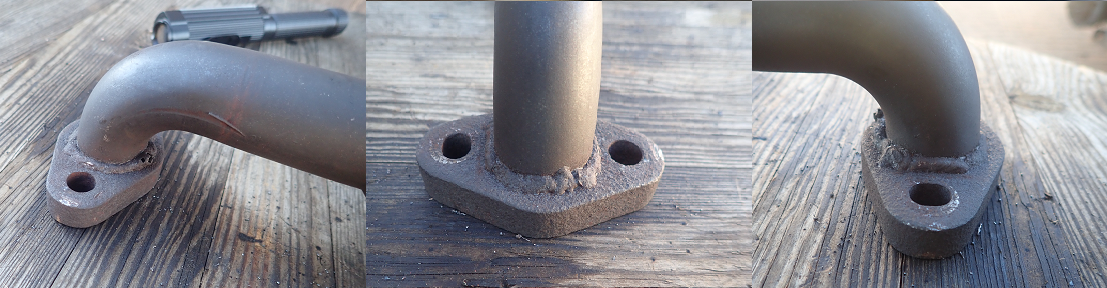
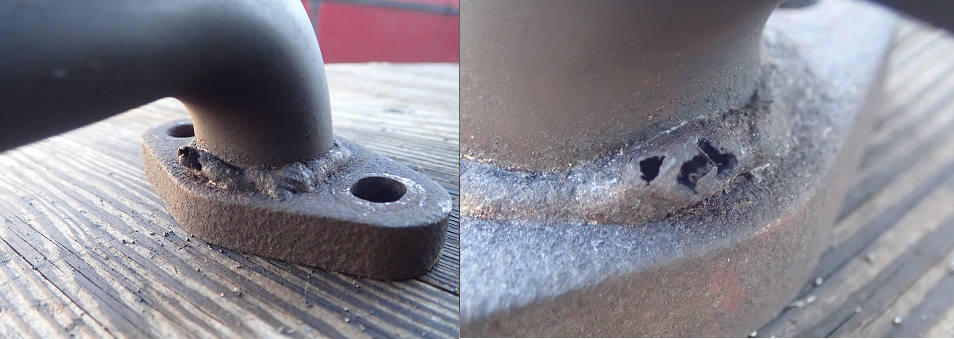
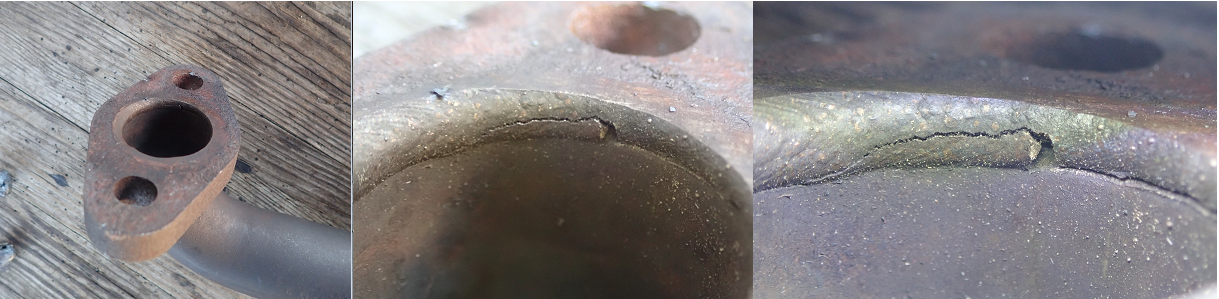
quote | Originally posted by A_Lonely_Potato:
check those logs for cracks! |
|
Is there anything else I should be looking for? Any common areas that are notorious for cracking?
|
|
|
pmbrunelle
|
NOV 04, 06:29 PM
|
|
|
|
MaxxPower1968
|
NOV 11, 11:26 AM
|
|
quote | Originally posted by pmbrunelle:
Exhaust manifold with bellows on car:
|
|
Hey pmbrunelle, yeah the bellows are pretty nice and they do a great job at absorbing vibration. I work at a big rocket company in Hawthorne and we use bellows on many tubing assemblies to deal with expansion, vibration, and variations with extreme temperature changes. Unfortunately, with living in California, I wouldn't be able to get away with a modification like that on a smog required car.
A quick update on the situation: I grinded off the ugly weld from the firewall side manifold and, just as I suspected, there were leaks in the seal. So I'm going to have to reweld it correctly. I had both manifolds hot tanked at my local machine shop to try to minimize contaminants getting into the welds. Hopefully I can get it done next weekend.
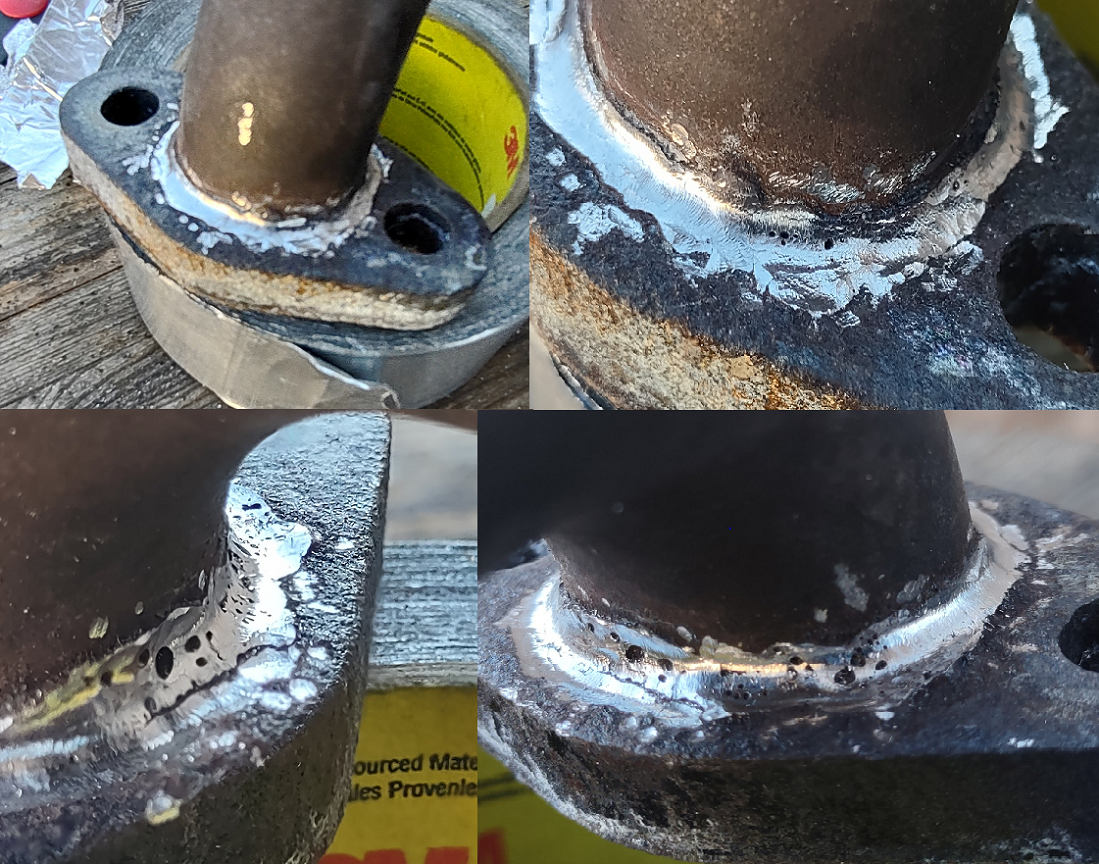 [This message has been edited by MaxxPower1968 (edited 11-11-2022).]
|
|
|
pmbrunelle
|
NOV 11, 11:53 AM
|
|
The flanges are mild steel. The tubes are 400-something ferritic stainless.
What filler metal will you use?
I migged mine with 309LSi wire; it's supposed to work for joining dissimilar metals.
|
|
|
fierosound
|
NOV 11, 12:41 PM
|
|
|
|
MaxxPower1968
|
NOV 11, 02:14 PM
|
|
quote | Originally posted by pmbrunelle:
The flanges are mild steel. The tubes are 400-something ferritic stainless.
What filler metal will you use?
I migged mine with 309LSi wire; it's supposed to work for joining dissimilar metals. |
|
I ordered some 308 stainless TIG rod. Should arrive in a couple more days. That'll give me some time to practice. I haven't TIG'd in close to 10yrs,
I have a set of the FEL-Pro from TFS, a set of MAHLE and a set of VW Empi gaskets. I haven't had a chance to do a comparison inspection yet. I want to see what the differences in materials, thickness, and maybe post compression. I'll post photos if anyone is interested. I still have a ways to go before I can get around to installing. I have to decide what I'm going to do about the heat shield. From what I've read, it's more of a splash guard to keep oil from causing a fire. Anyway, mine is all pitted and damaged from the exhaust leaks. I tried to grind it smooth but it's a little too thin to do both sides.
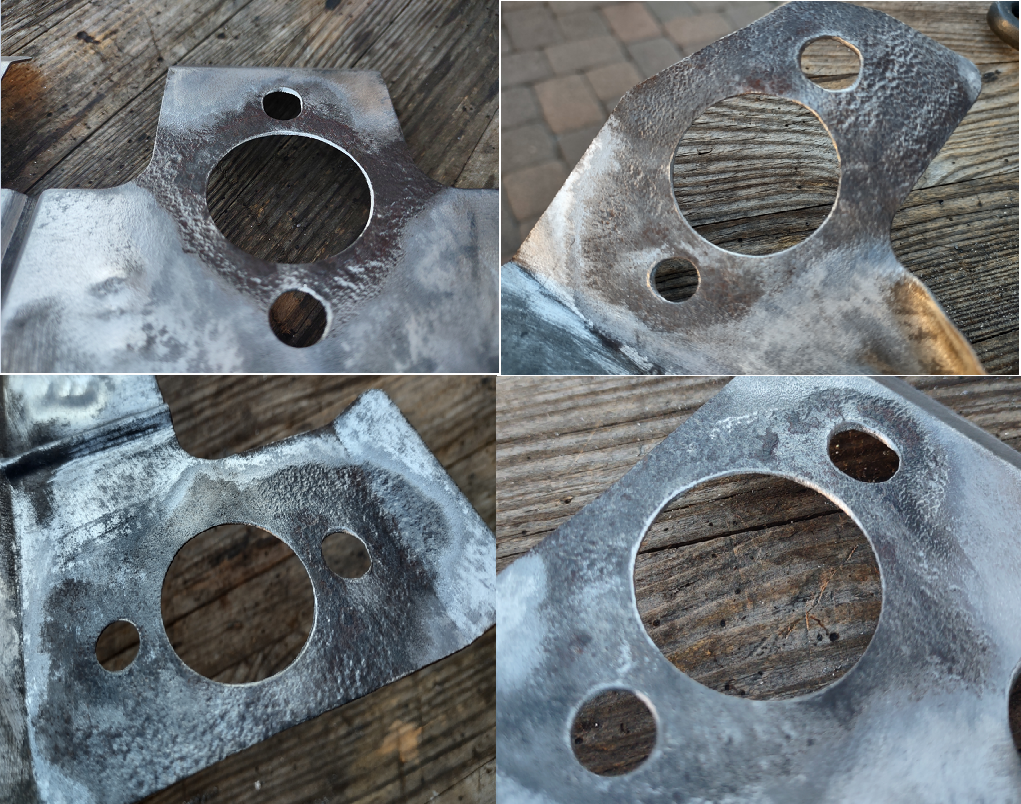 [This message has been edited by MaxxPower1968 (edited 11-11-2022).]
|
|

 |
|