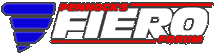

 |
Upgrade 84-86 2.5s w/ newer 87 belt system, possible? (Page 3/3) |
|
Dennis LaGrua
|
OCT 14, 02:02 AM
|
|
quote | Originally posted by 82-T/A [At Work]:
Ok, so, I never updated this thread, and figured I would do it now, while also asking a question (next post).
I was able to upgrade to pretty much everything on the 87-88 engine... this is what I did (I'll update this later with more detail when I have time):
- Kept the upper and lower alternator bracket for the 1985-1986. That's because I cannot install the 87-88 belt tensioner on an 84-86 block. So... the alternator becomes the belt tensioner.
- I used the waterpump pulley from a 1987-1988 (6-groove serpentine pulley)
- I swapped out the pulley on the alternator with a 6-groove serpentine pulley from an 87-88. (I actually upgraded to a CS130 and installed a decoupler pulley)
- I replaced the crank pulley and hub with a brand new General Motors harmonic balancer for a 1989-1991 Iron Duke, which I was able to find online. (but you can just swap over the 87-88 6-groove pulley and hub.
- I used 1987-1988 A/C compressor brackets, and installed an 86+ L4 A/C compressor with a 6-groove serpentine pulley.
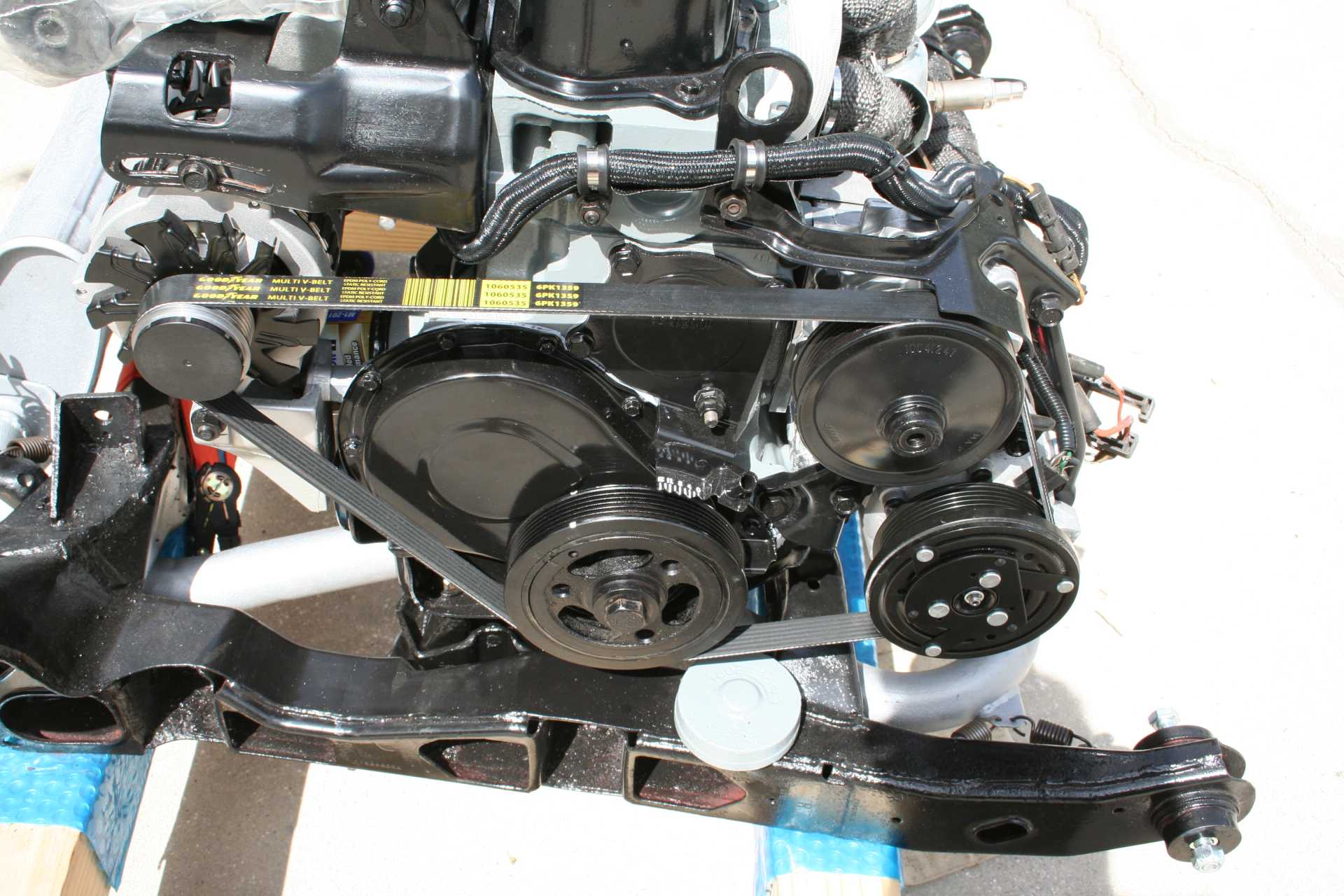
Although it looks bad, it's actually the same surface area as the previous V-belt system had. I'm looking for a solution to install some kind of idler pulley to give me a little bit more surface area on the crank. |
|
I don't believe in this picture there is insufficient belt wrapped around the crankshaft pulley to prevent slippage under heavy load. IIRC there must be a minimum of 50% wrap to be effective.------------------ " THE BLACK PARALYZER" -87GT 3800SC Series III engine, custom ZZP /Frozen Boost Intercooler setup, 3.4" Pulley, Northstar TB, LS1 MAF, 3" Spintech/Hedman Exhaust, P-log Manifold, Autolite 104's, MSD wires, Custom CAI, 4T65eHD w. custom axles, Champion Radiator, S10 Brake Booster, HP Tuners VCM Suite. "THE COLUSSUS" 87GT - ALL OUT 3.4L Turbocharged engine, Garrett Hybrid Turbo, MSD ign., modified TH125H " ON THE LOOSE WITHOUT THE JUICE "
|
|
|
cartercarbaficionado
|
OCT 17, 02:53 AM
|
|
quote | Originally posted by Dennis LaGrua:
I don't believe in this picture there is insufficient belt wrapped around the crankshaft pulley to prevent slippage under heavy load. IIRC there must be a minimum of 50% wrap to be effective.
|
|
looking at this the only thing that would need to be done is to make an idler that attaches to the block off plate to wrap it around the crank and ac more if needed I would probably make a new plate since it's pretty easy to fab and could be made much thicker for modifications
|
|
|
82-T/A [At Work]
|
OCT 17, 09:06 AM
|
|
quote | Originally posted by cartercarbaficionado:
looking at this the only thing that would need to be done is to make an idler that attaches to the block off plate to wrap it around the crank and ac more if needed I would probably make a new plate since it's pretty easy to fab and could be made much thicker for modifications |
|
You and I think a lot a like... I was looking at some alternator brackets on eBay the other day... and discovered some bracket that allows you to add a second (or third) alternator to a Tahoe or something... and it occurred to me, bolting it to the block-off plate area MIGHT just work.
The biggest problem I see is that the bolt holes for the block-off plate are much, much smaller diameter than what was used in the 87-88 for the actual tensioner. The difference of course is that it's three bolts (87-88) compared to 4 bolts (84-86). My concern is the tension that might be put on these bolts, or even still, the plate underneath it, and the holes that the bolts go into. These bolt holes are not well supported, and I don't think they were originally designed to take any kind of real tension, rather... just to support a block-off plate. But I could be wrong... because I think in F/R applications (like the Chevy S-10), it supported a front-mounted water pump, which most certainly was under tension... so I don't see how that would be any different then (I apologize, I'm thinking out loud here).
My only concern is the top two bolts, and potential clearance needed for a plate to go on that. If I had a metal break or bending system, I could probably make a bracket that would sit on top / above that.
How hard would it be to then simply weld a nut on the underside of a plate to hold an idler pulley?
You might be right Sleek... I am really thinking this is the answer, and possibly the easiest to do. I'll have to hit harbor freight, as I don't have a metal cutting band saw either... I really think this might work...
EDIT: I just bought a spare 1984 Fiero 2m4 coolant block-off plate from eBay, so I don't have to mess too much with the one already on the motor. I should get it in a week, and by that point, I'll have everything else I need. Harbor freight actually has several breaks on display... so I may sneaky go in there and just use one while I'm there, hahaha...
EDIT #2: I just bought two 1/8th inch steel plates (8" x 10") which I'll use as the bracket.
Have I told you recently how much I love you, man?[This message has been edited by 82-T/A [At Work] (edited 10-17-2024).]
|
|
|
cartercarbaficionado
|
OCT 17, 08:56 PM
|
|
quote | Originally posted by 82-T/A [At Work]: You and I think a lot a like... I was looking at some alternator brackets on eBay the other day... and discovered some bracket that allows you to add a second (or third) alternator to a Tahoe or something... and it occurred to me, bolting it to the block-off plate area MIGHT just work.
The biggest problem I see is that the bolt holes for the block-off plate are much, much smaller diameter than what was used in the 87-88 for the actual tensioner. The difference of course is that it's three bolts (87-88) compared to 4 bolts (84-86). My concern is the tension that might be put on these bolts, or even still, the plate underneath it, and the holes that the bolts go into. These bolt holes are not well supported, and I don't think they were originally designed to take any kind of real tension, rather... just to support a block-off plate. But I could be wrong... because I think in F/R applications (like the Chevy S-10), it supported a front-mounted water pump, which most certainly was under tension... so I don't see how that would be any different then (I apologize, I'm thinking out loud here).
My only concern is the top two bolts, and potential clearance needed for a plate to go on that. If I had a metal break or bending system, I could probably make a bracket that would sit on top / above that.
How hard would it be to then simply weld a nut on the underside of a plate to hold an idler pulley?
You might be right Sleek... I am really thinking this is the answer, and possibly the easiest to do. I'll have to hit harbor freight, as I don't have a metal cutting band saw either... I really think this might work...
EDIT: I just bought a spare 1984 Fiero 2m4 coolant block-off plate from eBay, so I don't have to mess too much with the one already on the motor. I should get it in a week, and by that point, I'll have everything else I need. Harbor freight actually has several breaks on display... so I may sneaky go in there and just use one while I'm there, hahaha...
EDIT #2: I just bought two 1/8th inch steel plates (8" x 10") which I'll use as the bracket.
Have I told you recently how much I love you, man?
|
|
oh I would have just welded a standoff and used a ranger v6 idler puller to do it since they are generally smaller. them again I'm extremely lazy so yeah.
|
|
|
82-T/A [At Work]
|
OCT 19, 08:31 PM
|
|
quote | Originally posted by cartercarbaficionado:
oh I would have just welded a standoff and used a ranger v6 idler puller to do it since they are generally smaller. them again I'm extremely lazy so yeah. |
|
So, when I looked on eBay right after this... I found an 84 block-off plate.
I was going to use THAT as a guide for the bracket so that I wouldn't have to tear my bracket apart. And then it hit me... I will use THAT block-off plate as the bracket! It's easily 1/8th of an inch thick (if not thicker), and it's very, very strong. I saved all the original bolts for the block-off plate, which as you know, have studs on the ends of them so that you can attach that weird plastic thing where the harness passed through. I removed them and replaced them with normal screws simply because I didn't need the studs. But I'll put those back, and I can literally just mount the duplicate bracket onto that... cut the timing guide on it, drill a hole, weld a nut to the other end, and there I go... I've got my idler pulley!!!
I can then go back to the stock 87 belt, and continue to use the alternator as the tensioner.
Note, I started the car for the first time... just using starting fluid. Started right up, but no belt squealing. I don't think it's horrible, but so un-ideal. The slightest bit of rain, or some spirited driving, and I'm sure it would probably slip unless I go insane with it. And it's probably not good on the bearings to have a belt so ridiculously tensioned. When I have more coverage on the alternator pulley and the crank pulley... it won't need to be insanely tight.
|
|
|
cartercarbaficionado
|
OCT 20, 05:09 PM
|
|
quote | Originally posted by 82-T/A [At Work]: So, when I looked on eBay right after this... I found an 84 block-off plate.
I was going to use THAT as a guide for the bracket so that I wouldn't have to tear my bracket apart. And then it hit me... I will use THAT block-off plate as the bracket! It's easily 1/8th of an inch thick (if not thicker), and it's very, very strong. I saved all the original bolts for the block-off plate, which as you know, have studs on the ends of them so that you can attach that weird plastic thing where the harness passed through. I removed them and replaced them with normal screws simply because I didn't need the studs. But I'll put those back, and I can literally just mount the duplicate bracket onto that... cut the timing guide on it, drill a hole, weld a nut to the other end, and there I go... I've got my idler pulley!!!
I can then go back to the stock 87 belt, and continue to use the alternator as the tensioner.
Note, I started the car for the first time... just using starting fluid. Started right up, but no belt squealing. I don't think it's horrible, but so un-ideal. The slightest bit of rain, or some spirited driving, and I'm sure it would probably slip unless I go insane with it. And it's probably not good on the bearings to have a belt so ridiculously tensioned. When I have more coverage on the alternator pulley and the crank pulley... it won't need to be insanely tight. |
|
making good progress then. maybe I should make you help me with my internationals engine swap lol. your gonna have to make a parts list of what you used so we can replicate this in the future for more dukes especially since they tend to last longer with boost (compared to a 2.8)and the serpentine belt allows a supercharger to be easily mounted[This message has been edited by cartercarbaficionado (edited 10-20-2024).]
|
|

 |
|