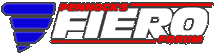

 |
The Turbo 3500 F23 swap (Page 52/79) |
|
pmbrunelle
|
MAR 25, 04:59 PM
|
|
How were you thinking of making this manifold? Cast aluminum with 3D printed positives that burn away when you pour the liquid metal?
quote | Originally posted by ericjon262: I am curious about the gains that could be had by changing the injector angle, but I don't think it would be very much.
|
|
I don't know about hp gains, but anything you do to reduce wall-wetting can only facilitate tuning the transient compensation, leading to better driving manners.[This message has been edited by pmbrunelle (edited 03-25-2020).]
|
|
|
ericjon262
|
MAR 25, 05:41 PM
|
|
quote | Originally posted by pmbrunelle:
How were you thinking of making this manifold? Cast aluminum with 3D printed positives that burn away when you pour the liquid metal?
I don't know about hp gains, but anything you do to reduce wall-wetting can only facilitate tuning the transient compensation, leading to better driving manners.
|
|
as close as injector is to the valve, I don't think wall wetting would present much of a problem, but the only way to tell for sure will be to build it. That being said, I am going to continue to investigate a more well placed injector to get it as good as possible.
Production? Not really sure yet it's very low priority, but prototypes will be 3D printed if I can ever get my Folgertech FT6 put together. Lost print casting definitely an idea I was toying with, but the mass of the print would require the print to be burned out prior to the pour. I think before I get to the point of casting it, I'll get an oven I can dedicate to the process, as well as some kind of shaker table to help settle the casting sand into the print. the other hard part will be machining the cast part, since I don't yet have a mill or lathe, which leads to another part of the puzzle, leaving enough material to machine the parts flat, but not so much to be a burden to machine.
I have even considered just printing the manifold, but I am curious about how well a print would handle the NVH, and heat. especially considering it has water manifolds at the front and rear.
------------------ "I am not what you so glibly call to be a civilized man. I have broken with society for reasons which I alone am able to appreciate. I am therefore not subject to it's stupid laws, and I ask you to never allude to them in my presence again."
cognita semper
http://www.fiero.nl/forum/Forum2/HTML/119122.html
|
|
|
pmbrunelle
|
MAR 25, 07:32 PM
|
|
You're thinking of printing in plastic with your Folger Tech, or outsourcing the printing with metal?
At work, we tried making watertight prototype plastic cases from SLS nylon, but the cases allowed water to go through. We tried painting the parts with heavy coats of paint (rattle can), the idea being to seal the pores, but that didn't work.
With DMLS (my info is a couple years old on this one) the raw print is porous, so they infuse the print with some other metallic stuff to fill the pores. This part didn't need watertightness, so we didn't test it for that. I don't know if the final result is porous though.
When you cast the intake, you should include three bumps on it, opposite the first machined face. This will let you clamp the intake onto the mill table in a steady non-rocking manner for Op 1 of machining. Once you get the first side machined, the other setups become easier to do.
|
|
|
ericjon262
|
MAR 25, 11:20 PM
|
|
quote | Originally posted by pmbrunelle:
You're thinking of printing in plastic with your Folger Tech, or outsourcing the printing with metal?
At work, we tried making watertight prototype plastic cases from SLS nylon, but the cases allowed water to go through. We tried painting the parts with heavy coats of paint (rattle can), the idea being to seal the pores, but that didn't work.
With DMLS (my info is a couple years old on this one) the raw print is porous, so they infuse the print with some other metallic stuff to fill the pores. This part didn't need watertightness, so we didn't test it for that. I don't know if the final result is porous though.
When you cast the intake, you should include three bumps on it, opposite the first machined face. This will let you clamp the intake onto the mill table in a steady non-rocking manner for Op 1 of machining. Once you get the first side machined, the other setups become easier to do. |
|
3d printing in metal would be cost prohibitive, I'll print prototypes in plastic, then use the prints to cast my own intake. I didn't have high confidence that a 3d printed water manifold would be viable.
Thanks for the tip on the casting/machining, I hadn't thought about that. ------------------ "I am not what you so glibly call to be a civilized man. I have broken with society for reasons which I alone am able to appreciate. I am therefore not subject to it's stupid laws, and I ask you to never allude to them in my presence again."
cognita semper
http://www.fiero.nl/forum/Forum2/HTML/119122.html
|
|
|
ericjon262
|
MAR 25, 11:45 PM
|
|
if the intake design wasn't last priority yesterday, it is today! got some toys in!

and these:

(wow that picture looks like crap...)
Precision 6266 CEA (gen 1), and a Turbosmart Compgate 40, along with a bunch of weld els, and some V bands. not pictured, I have a bellows that I plan to install in the hotside from on the pipe that will come from the rear bank, to the turbo. I made a bunch of progress on the front manifold, some of the fitup is pretty rough, and some of the welds are... well they suck, but they're better than my last set of manifolds. I started with the front manifold so that when when I make the rear, which will be way more visible, I can incorporate lessons learned with the front manifold and have one of them looking great. I didn't take any pictures yet, I'll get some tomorrow when I finish it and start the rear...------------------ "I am not what you so glibly call to be a civilized man. I have broken with society for reasons which I alone am able to appreciate. I am therefore not subject to it's stupid laws, and I ask you to never allude to them in my presence again."
cognita semper
http://www.fiero.nl/forum/Forum2/HTML/119122.html
|
|
|
ericjon262
|
MAR 26, 11:45 PM
|
|
Got a ton of work done on the manifolds today, at this point, I'd say I'm about 75% done, I still need to weld the tops of the runners, and a couple of other joints. I started by making the front log, which would be mostly out of sight, that way if I could learn how not to do it for the one that would be visible.
I also ordered a set of long shank carbide burrs, I left the inside of the logs slightly small, as it's easier to grind them out from the inside, than to fill a huge gap with weld.
There were a couple of spot where I let the heat get away from me, but overall I think they're OK. I'm going to finish the welding up in the morning, and then I'll figure out where I'm going to put the turbo, and I'll start tacking pipe together and working on the rest of the hotside. I have the basic idea of what I want to do for the hotside, unfortunately, I don't have the pipe yet, hopefully it gets here soon.




 ------------------ "I am not what you so glibly call to be a civilized man. I have broken with society for reasons which I alone am able to appreciate. I am therefore not subject to it's stupid laws, and I ask you to never allude to them in my presence again."
cognita semper
http://www.fiero.nl/forum/Forum2/HTML/119122.html
|
|
|
ericjon262
|
MAR 27, 11:25 AM
|
|
Here's a link to the file for the header flanges, please read and understand the notes in the drawing. if you want to produce these commercially, please contact me first. When I get around to it, I'll draw up other port dimensions, these are for 1.5" primaries, or face welding pipes to the flange. there are 3 files, one DXF, one DWG, and one PDF. they are all the same drawing, if you need another file type, LMK and I'll see if I can make it happen.
https://drive.google.com/dr...RS4fHD6r?usp=sharing------------------ "I am not what you so glibly call to be a civilized man. I have broken with society for reasons which I alone am able to appreciate. I am therefore not subject to it's stupid laws, and I ask you to never allude to them in my presence again."
cognita semper
http://www.fiero.nl/forum/Forum2/HTML/119122.html
|
|
|
ericjon262
|
MAR 28, 12:52 AM
|
|
what a day... Called my metal supplier about the pipe for the rest of the hotside:
"it'll ship out sometime late next week..."
WTF. I ordered it last week. I called around, and Online metals, which has a warehouse about an hour and a half from me had it! I placed the order for pickup, and they said they would email when it was ready.
1 hour, nothing...
2 hours, nothing...
3 hours,... OK I'll call them...
We're having trouble locating all of the order, we'll call you when we find all of it.
an hour later, I figure I better start on the way to pick whatever they do have up so I can get SOMETHING done this weekend.
hour and a half later, as I'm pulling up to the warehouse, I get an email:
"Hey, we don't have any of it..."
!
Keep in mind, I drove the pig rig over there, so there goes 3 hours of driving, and a 1/2 tank of gas... I emailed them back, telling them I just canceled an order because it would take too long, and now (4:00 PM) even if I could find someone else kinda local, there's minimal chance I'll get there before doors close. thankfully they were understanding of my frustration, and they offered to overnight my order to me from one of their east coast warehouses. unfortunately, I still won't have any material until Wednesday, because their office was closed over there, so the order has to be placed, then get to shipping, then to me... DOH.
tomorrow, I plan to work on a mount to hold the turbo, I plan to bolt it to the top of the trans on the ecotec front mount boss, and maybe make a trip to the junkyard to try and find a better pedal for the DBW throttle. I might also notch the front engine crossmember to allow more clearance for the exhaust. the other big ticket I need to tackle is the shifter, my current one won't work with the new turbo kit, but that's ok, because it was kinda ugly anyways. the new one will have the cables approach from outboard on the driver's side, so they allow a ton of clearance, instead of my old setup that cut down the middle.------------------ "I am not what you so glibly call to be a civilized man. I have broken with society for reasons which I alone am able to appreciate. I am therefore not subject to it's stupid laws, and I ask you to never allude to them in my presence again."
cognita semper
http://www.fiero.nl/forum/Forum2/HTML/119122.html
|
|
|
ericjon262
|
MAR 29, 11:38 PM
|
|
I did almost nothing to the car yesterday... today I made decent progress though.
Turbo is mounted, the oil feed is threaded, so I don't need a flanged fitting, I'll just thread in a AN adapter and call it good.

The turbo will be pretty much right behind my head, before I go any further, I need to make sure it will clear the decklid there, or only require a tiny notch.

I did a mock up of the front bank up pipe, it'll need more tape to keep the exhaust in there...


The rear bank will be a pretty straight shot to the turbo

Other than that, My carbide burrs came in, so I got the manifolds hogged out, that took a good bit longer than I expected. tonight I'm going to work on a drawing for the new shift mechanism, and the plan for tomorrow is to mount the flexfuel sensor like I said I would the other day.
------------------ "I am not what you so glibly call to be a civilized man. I have broken with society for reasons which I alone am able to appreciate. I am therefore not subject to it's stupid laws, and I ask you to never allude to them in my presence again."
cognita semper
http://www.fiero.nl/forum/Forum2/HTML/119122.html
|
|
|
ericjon262
|
MAR 30, 04:36 AM
|
|
some of the night's progress on the shift linkage (after I said 5 more minutes for the past 3 hours...)

The idea is that this will replace the stock F23 shift mechanism entirely with the exception of the select arm, I still need to draw the shift arm, and nail down the cable dimensions. if anyone didn't know and needs to, the select movement at the shifter, is approximately 50mm, and the shift movement is approximately 90mm, and the stock F23 select arm is about 45mm from fulcrum to input.------------------ "I am not what you so glibly call to be a civilized man. I have broken with society for reasons which I alone am able to appreciate. I am therefore not subject to it's stupid laws, and I ask you to never allude to them in my presence again."
cognita semper
http://www.fiero.nl/forum/Forum2/HTML/119122.html
|
|

 |
|