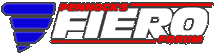

 |
PULLING OLD BUSHINGS THE CHEAP WAY... (Page 1/2) |
|
eti engineer
|
JAN 06, 09:51 AM
|
|
Gents,
After looking for a tool to remove the old bushings from the rear suspension of my '88 and finding nothing feasible, I decided to make my own. Total cost was around $30 and it can be used to pull just about every bushing in the vehicle. It consists of a regular 5-ton puller from Harbor Freight (a little over 29 dollars), which can be used on many other things after you're done with the Fiero and 4-inch long, 5'16" carriage bolt with nut. The head of the bolt is the same diameter as the bushing sleeves in the Fiero, and the squared-off piece under the head of the bolt keeps it centered while pulling. The setup can be used for larger bushings, too. Just buy a large carriage bolt.
The first thing is to center punch the head of the bolt and drill a a small dimple in the center of it. This is to keep the puller centered while the inner bushing sleeve is being pushed out of the rubber. This is all that needs to be done. See pix.
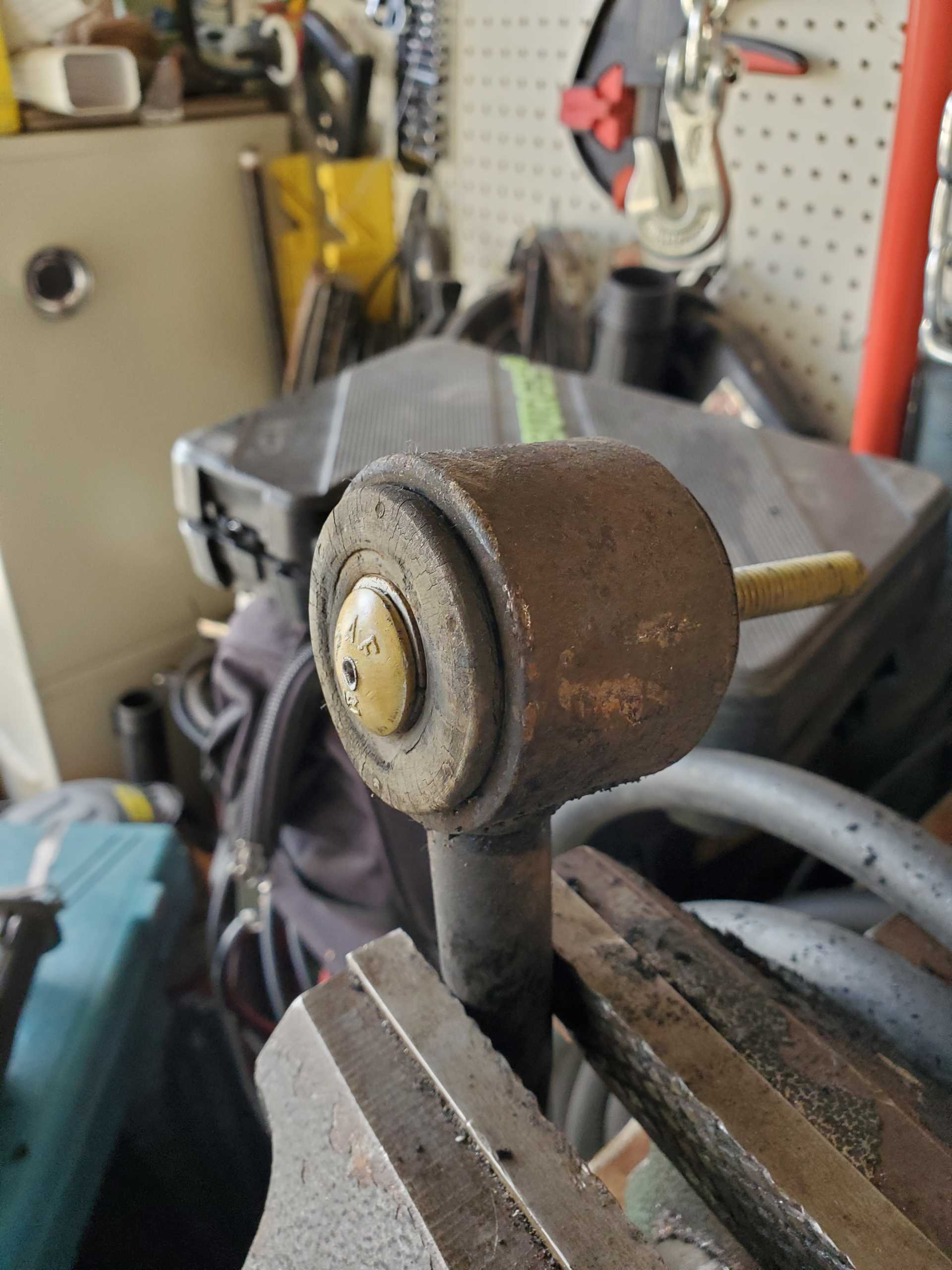
Put the item in which the bushing is installed in a vice, as shown in the pix.
Then install the puller so that the nipple on the threaded piece sits in the dimple you made in the head of the bolt and so the claws of the puller jaws are firm on the edge of the circular area in which the bushing is installed. Using a drill, preferable a rattle gun type as they are called, in the thread tightening direction, keep threading the puller into the head of the bolt. This will force the bushing sleeve out of the rubber insert. Once the sleeve is out, cut the rubber with a knife or like I did with a SawzAll and using a screwdriver and long-nosed pliers to peel it out of the piece in which it is installed, pull the rubber out and toss it.
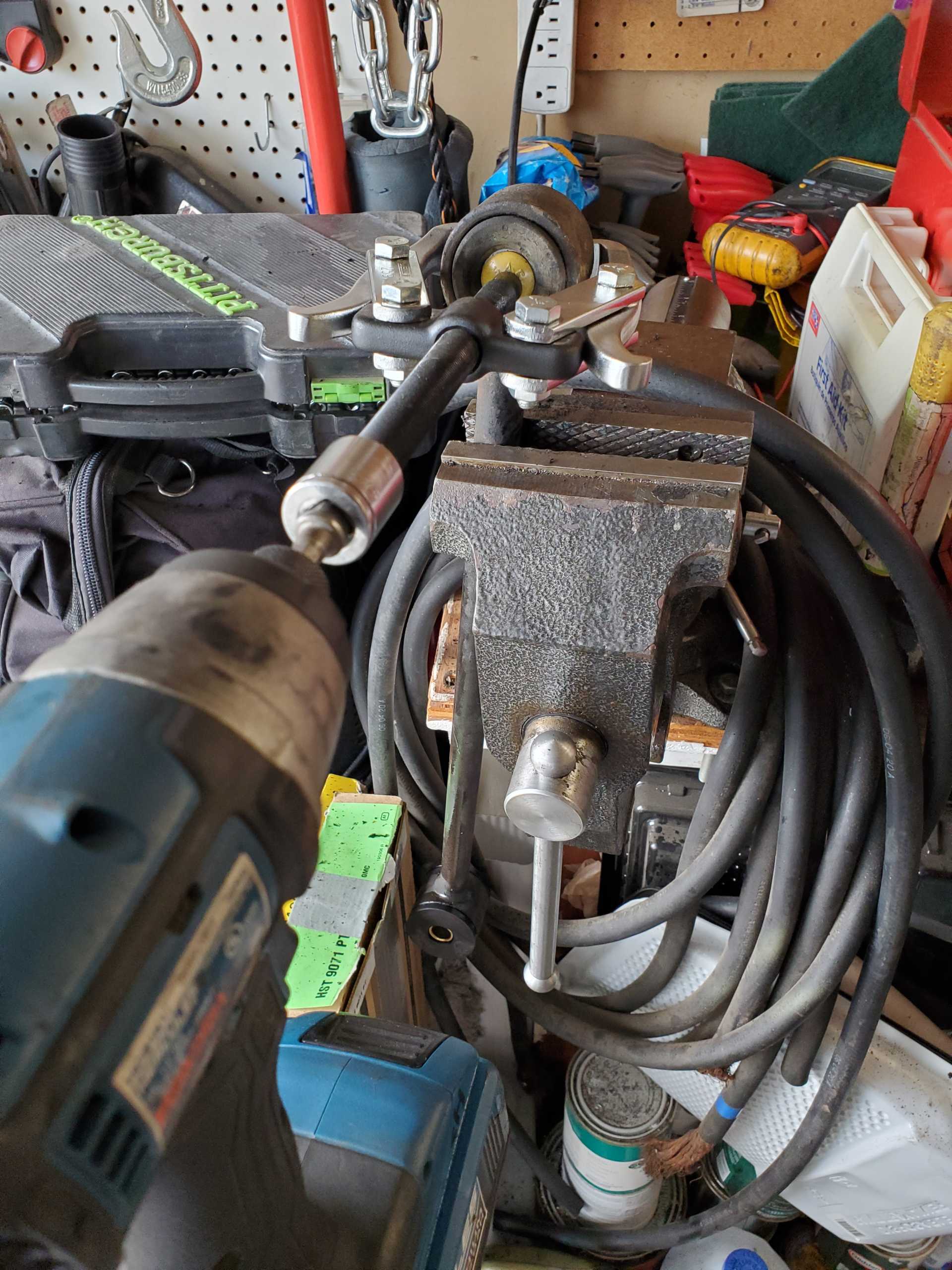
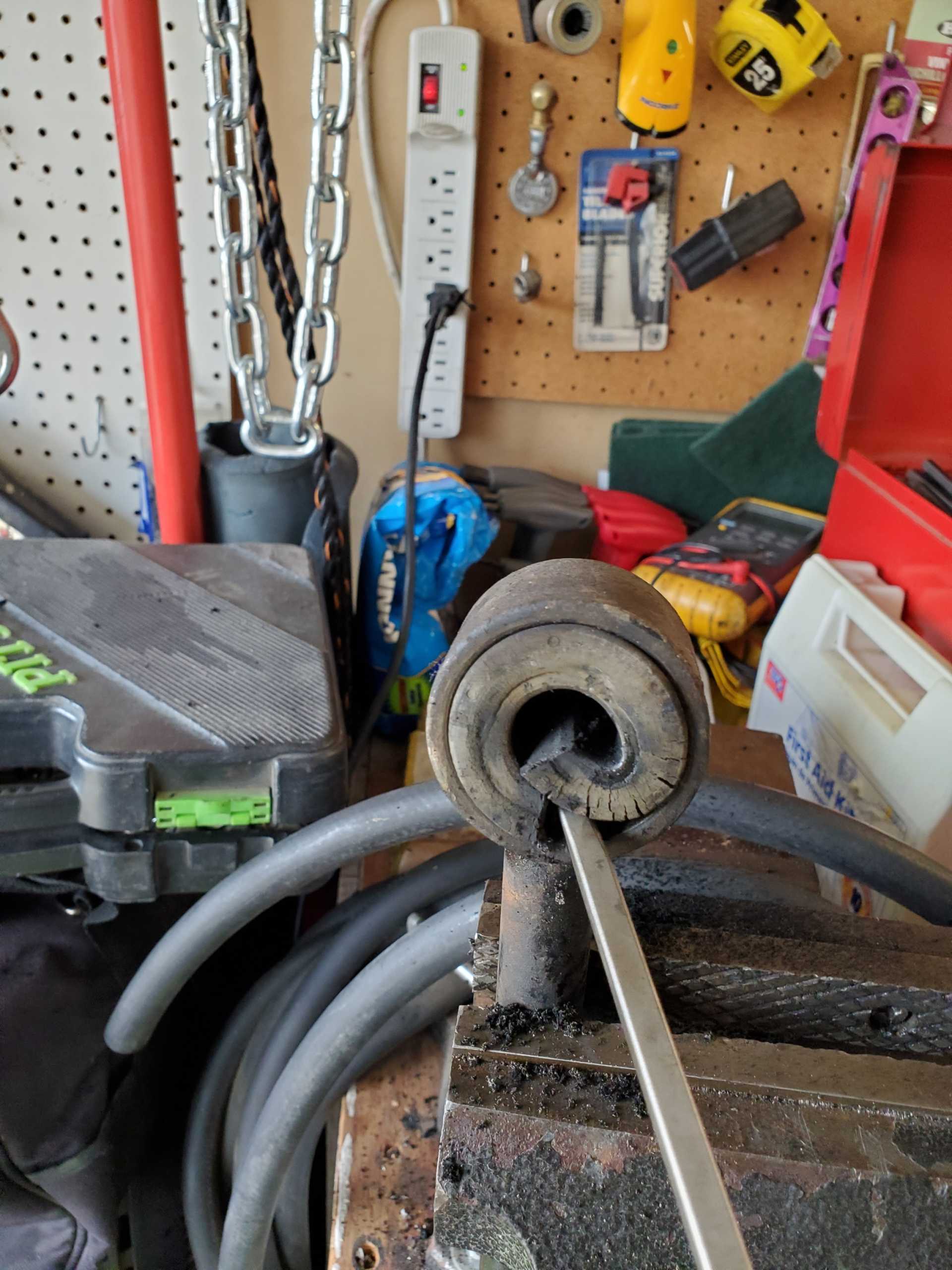
|
|
|
eti engineer
|
JAN 06, 10:10 AM
|
|
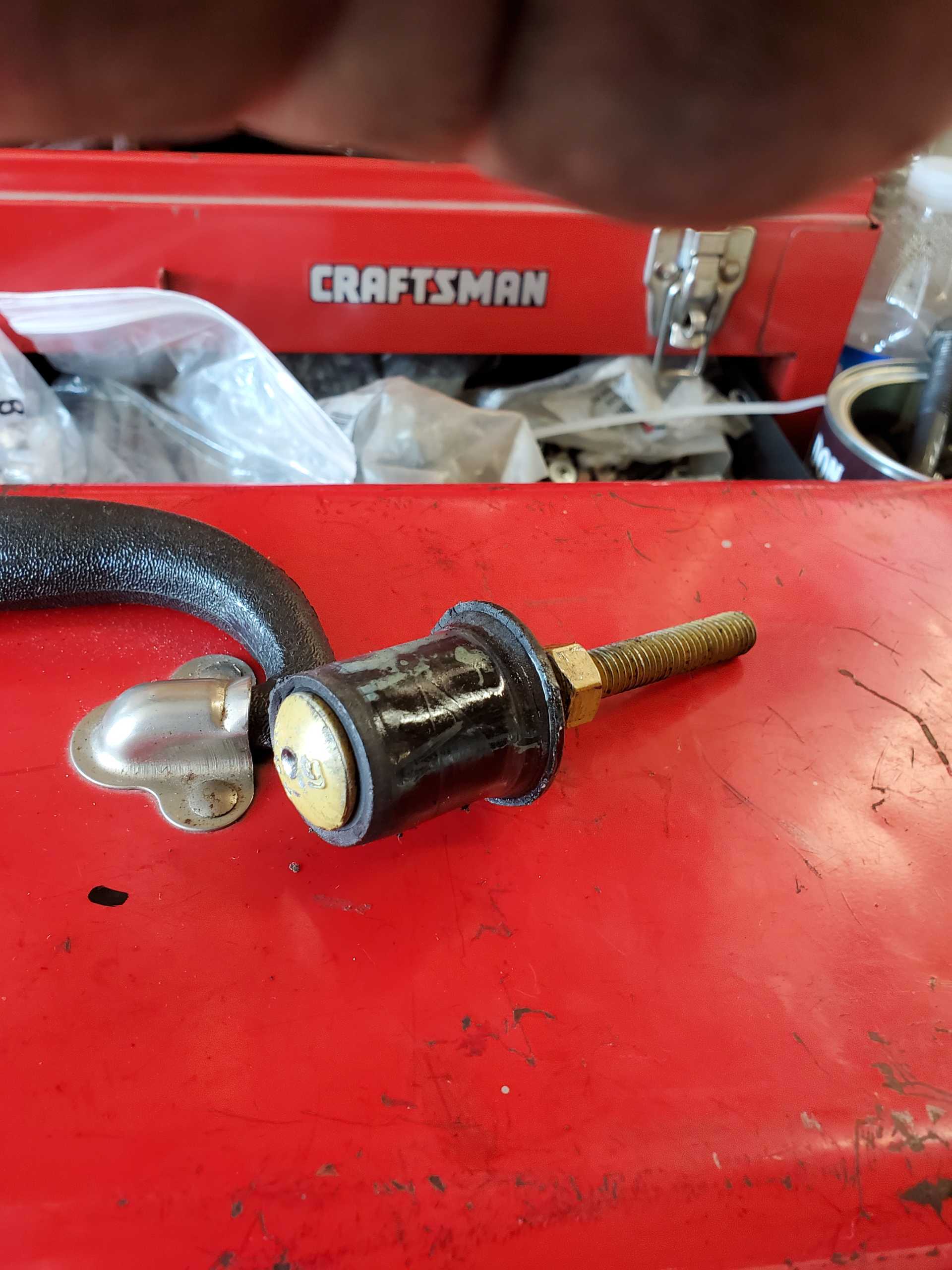
I should have included this pix to show what the nut was for. This is a shot of the carriage bolt with the inner sleeve of the bushing which was pushed out, still intact. Unthread the nut, and either keep the metal sleeve to be used elsewhere (I never throw away any free hardware), put the nut back on the bolt so you don't lose it and you're done.
|
|
|
Raydar
|
JAN 06, 02:08 PM
|
|
Pretty cool! I started out, years ago, burning the bushings out. We all know what a mess that is. Most recently, I used a 1/8 bit, and drilled around the inner sleeve, and then drilled around the outer sleeve. (If you hold the drill just right, it will "walk around" the sleeve, and maybe won't even break. ) But this looks to be even less trouble. Good show!
|
|
|
Patrick
|
JAN 06, 02:33 PM
|
|
I imagine this would work with lower control arm bushings as well. Hmmm... simple yet effective.
Do you also have a "cheap" way (that doesn't require a press) to install the new bushings? Could the puller also push the new bushings in with the addition of a large "washer"?[This message has been edited by Patrick (edited 01-06-2021).]
|
|
|
ragoldsmith
|
JAN 06, 10:42 PM
|
|
quote | Originally posted by Patrick:
I imagine this would work with lower control arm bushings as well. Hmmm... simple yet effective.
Do you also have a "cheap" way (that doesn't require a press) to install the new bushings? Could the puller also push the new bushings in with the addition of a large "washer"?
|
|
Man that’s a great idea. Looking at the picture, it looks like there might be enough space to fit the bushing in there to press it through...
|
|
|
eti engineer
|
JAN 07, 10:23 AM
|
|
quote | Originally posted by Patrick:
I imagine this would work with lower control arm bushings as well. Hmmm... simple yet effective.
Do you also have a "cheap" way (that doesn't require a press) to install the new bushings? Could the puller also push the new bushings in with the addition of a large "washer"?
|
|
I suppose it could. I just used the vice itself to push the new bushings in place. Just grease them up and push them in. Put grease on the inner sleeve, too. One thing you need to do, and I have seen this on a post in here, is to cut a piece of pipe to put in-between the lips of the control arm so when you press the new bushing in place, you don't crush the opening where the bushing fits[This message has been edited by eti engineer (edited 01-07-2021).]
|
|
|
Notorio
|
JAN 08, 08:13 PM
|
|
Bravo, Engineer. A very nice method
|
|
|
dremu
|
JAN 08, 08:38 PM
|
|
quote | Originally posted by eti engineer: I just used the vice itself to push the new bushings in place.
|
|
I find that a vise is very much like a small, manually operated press. Not as much force as a hydraulic press, but less chance of crushing thumbs, or breaking things that then fly across the garage. (Can still happen, just not as often and hopefully with less force.)
A vice is like a flathead screwdriver, so many uses other than the intended. (There's a joke there about having a vice of vises...)
-- A
|
|
|
eti engineer
|
JAN 09, 11:20 AM
|
|
quote | Originally posted by Notorio:
Bravo, Engineer. A very nice method  |
|
Desperation is the mother of invention, moreso than necessity... Thanks...
|
|
|
eti engineer
|
JAN 09, 11:25 AM
|
|
quote | Originally posted by dremu:
I find that a vise is very much like a small, manually operated press. Not as much force as a hydraulic press, but less chance of crushing thumbs, or breaking things that then fly across the garage. (Can still happen, just not as often and hopefully with less force.)
A vice is like a flathead screwdriver, so many uses other than the intended. (There's a joke there about having a vice of vises...)
-- A |
|
I have used my vice, sometimes with home-made attachments to do a lot of things. I once had copper covers for a vice I had that I could use to keep the jaws from marring things as I applied pressure. I don't know what happened to them. Probably in storage back in Virginia with a lot of other stuff I would like to have out here in CA, but don't have the room. My wife is a retired teacher and let's just say she has made major infringements on MY garage space....
|
|

 |
|