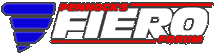

 |
Stripped V6 Main Bearing Bolt Hole: How screwed am I? (Page 1/2) |
|
reinhart
|
FEB 07, 12:54 AM
|
|
Weird. A engine main bearing bolt must have stripped the block on removal because when I went to tighten it never got past about 20 lb-ft. Several of the main bolts (not the one that has a stripped hole) was so tight I sheared off a 3/8" extension bar trying to loosen it. Not sure what was going on when GM built this particular engine.
88 V6
The bolt in question tightens to about 15-20 ft-lbs then loosens again so it keeps spinning forever.
Question,
Can I do a drill and helicoil a main bearing bolt hole? The threads are recessed about half an inch from the opening for these does that make the job more difficult? I've never done a drill/helicoil on any bolt hole. But anything different with this one than a standard bolt hole? Or what should I do? If it weren't such a critical bolt I would just red thread lock it.
Any advice appreciated.
|
|
|
Will
|
FEB 07, 10:14 AM
|
|
High tension fasteners are better off with solid-shell inserts like Time-serts ( https://timesert.com/ ) Time-serts use the same tap as the same size helicoil. There are also Keenserts and other thread repair insert technologies.
Helicoils do better with high *cycle* fasteners like thumb screws.
|
|
|
pmbrunelle
|
FEB 07, 12:48 PM
|
|
Since the original threads of the bolt reach down below the surface, whatever repair you make should ideally duplicate that; the repair threads should not be at the surface, but down at the same depth as stock.
|
|
|
reinhart
|
FEB 07, 05:10 PM
|
|
Looked into time-sert....Was watching a comparison video of timesert vs helicoil. Helicoil performed better than time-sert on that video but granted it was aluminum.. Also time-sert apparently needs me to drill an oversized hole which could make problems with the threads already being recessed in a slightly larger hole. If I go with helicoil and it fails when I'm tightening it, I suppose I can always then go to a larger hold for time sert.
If I go with helicoil, and I get the torque up to 70 ftlbs (as required), am I home free? What I mean, is it fairly certain the repair will hold through use? Or is this the type of repair that might fail later on even if I get it locked down to 70?
It looks like I should be able to get the thread down a half inch under the surface with a helicoil?
|
|
|
fieroguru
|
FEB 07, 06:53 PM
|
|
I would figure out how the lifter bore looks before getting too deep in hole repair. If the lifter bore is scarred, then you have to tear it down to fix the bore.
Drilling/tapping a bolt hole for the main cap will have lots of metal debris 1/2" from disaster upon reassembly so it will need to be done with extreme debris control.
|
|
|
pmbrunelle
|
FEB 07, 09:20 PM
|
|
quote | Originally posted by reinhart:
Looked into time-sert....Was watching a comparison video of timesert vs helicoil. Helicoil performed better than time-sert on that video but granted it was aluminum.. Also time-sert apparently needs me to drill an oversized hole which could make problems with the threads already being recessed in a slightly larger hole. If I go with helicoil and it fails when I'm tightening it, I suppose I can always then go to a larger hold for time sert.
If I go with helicoil, and I get the torque up to 70 ftlbs (as required), am I home free? What I mean, is it fairly certain the repair will hold through use? Or is this the type of repair that might fail later on even if I get it locked down to 70?
It looks like I should be able to get the thread down a half inch under the surface with a helicoil? |
|
Being cast iron, these threads should be more forgiving than aluminium.
I do not have the competence to make a judgement on the durability of the proposed repair, besides to say that the proposed helicoil/timesert solution seems OK. I have tried heli-coils for exhaust manifold bolts, and intake manifolds, but that's not the same.
Yes, to position the threads deeper with a helicoil, you drill/tap deeper than normal. Then, during coil insertion, rather than stopping once the coil is just below the machined surface, you keep turning until it is at the correct depth. If you're unsure about the depth, stop and check! It is easy to keep turning a helicoil deeper into its hole, but impossible to unscrew it if you've gone too far.
If you've never used a helicoil, then I suggest you practice on some scrap metal first. A common problem is to make the hole chamfer too large; the consequence is that the wire won't feed easily into the hole when you try to screw it in.
I am not sure if a timesert can be installed in a manner to only have threads deep down in the hole. With the flange, it does not look like it is meant for that, unless the hole is counterbored deeper than usual. For this reason, I would favour the helicoil solution.
quote | Originally posted by fieroguru: Drilling/tapping a bolt hole for the main cap will have lots of metal debris 1/2" from disaster upon reassembly so it will need to be done with extreme debris control. |
|
It would be a good idea to completely disassemble the engine.
Normally engine block machining is done on a bare block. Then, washing can proceed.
|
|
|
skywurz
|
FEB 08, 01:25 AM
|
|
quote | Originally posted by pmbrunelle:
It would be a good idea to completely disassemble the engine.
Normally engine block machining is done on a bare block. Then, washing can proceed. |
|
I would agree with this. But If you are going that far may as well take it to a machine shop and have them do that repair and a magnaflux inspection.
|
|
|
Mike in Sydney
|
FEB 08, 07:52 AM
|
|
I've been following this thread with interest. Just my two cents, if you decide to pull the engine for repairs, it would seem like a good time to find 3.4L to rebuild using the bits from your 2.8. You can get a get a short block from JEGS for under $2000.
|
|
|
Will
|
FEB 08, 03:57 PM
|
|
quote | Originally posted by reinhart:
Looked into time-sert....Was watching a comparison video of timesert vs helicoil. Helicoil performed better than time-sert on that video but granted it was aluminum.. Also time-sert apparently needs me to drill an oversized hole which could make problems with the threads already being recessed in a slightly larger hole. If I go with helicoil and it fails when I'm tightening it, I suppose I can always then go to a larger hold for time sert.
If I go with helicoil, and I get the torque up to 70 ftlbs (as required), am I home free? What I mean, is it fairly certain the repair will hold through use? Or is this the type of repair that might fail later on even if I get it locked down to 70?
It looks like I should be able to get the thread down a half inch under the surface with a helicoil? |
|
Who made the video? What was "performed better"?
Helicoil and Time-sert are installed with the SAME TAP... so there's no additional cutting for a Time-sert.
You can get 1d, 1.5d and 2d (d = diameter) helicoils... If you want to go helicoil, get 2d helicoils. They're certainly cheaper to install than Time-serts.
|
|
|
Notorio
|
FEB 09, 12:06 AM
|
|
I had to heli-coil two different cylinder head bolt holes. Very easy process and no problems torquing to higher level than the main bearing caps. Since I later had to trouble-shoot a leak-down issue I had the heads off/on two more times and no issues with torquing up to specs again (yes, with new bolts.)
|
|

 |
|