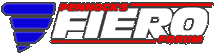

 |
F40 Shifting mechanism? (Page 1/2) |
|
cman5302
|
MAR 17, 03:31 PM
|
|
Sorry if this is the wrong place to post this, or if this isn't even worthy of a forum post.
Is there any video/explanation of how an F40 actually shifts? Me, my uncle (the fabricator/engineer), and my buddy (the robotics professional) are looking into designing a shift-by-wire mechanism that has control over both the clutch and gear shifts. But before we drop money on anything, we need to know what parts we need, and how such a mechanism would actually interact with the gearbox. Any resources?
|
|
|
fieroguru
|
MAR 17, 07:58 PM
|
|
Welcome to the forum!
Here is an old post of mine when I pulled the shifter mechanism from the F40. Basically there are two tabs that engage and disengage the shift rails for both the upper and lower main shafts. The main shift shaft rotated forward and back to select Odd or Even gears. It is pulled/pushed into and out of the transmission case to access R, 1/2, 3/4, 5/6.
quote | Originally posted by fieroguru:
Speaking of shifters, I went ahead and pulled the one in my car for inspection, to better understand how it works, and look for options to streamline the 2-3 upshift. Just put the transmission in neutral, remove 3 bolts and pull it out.
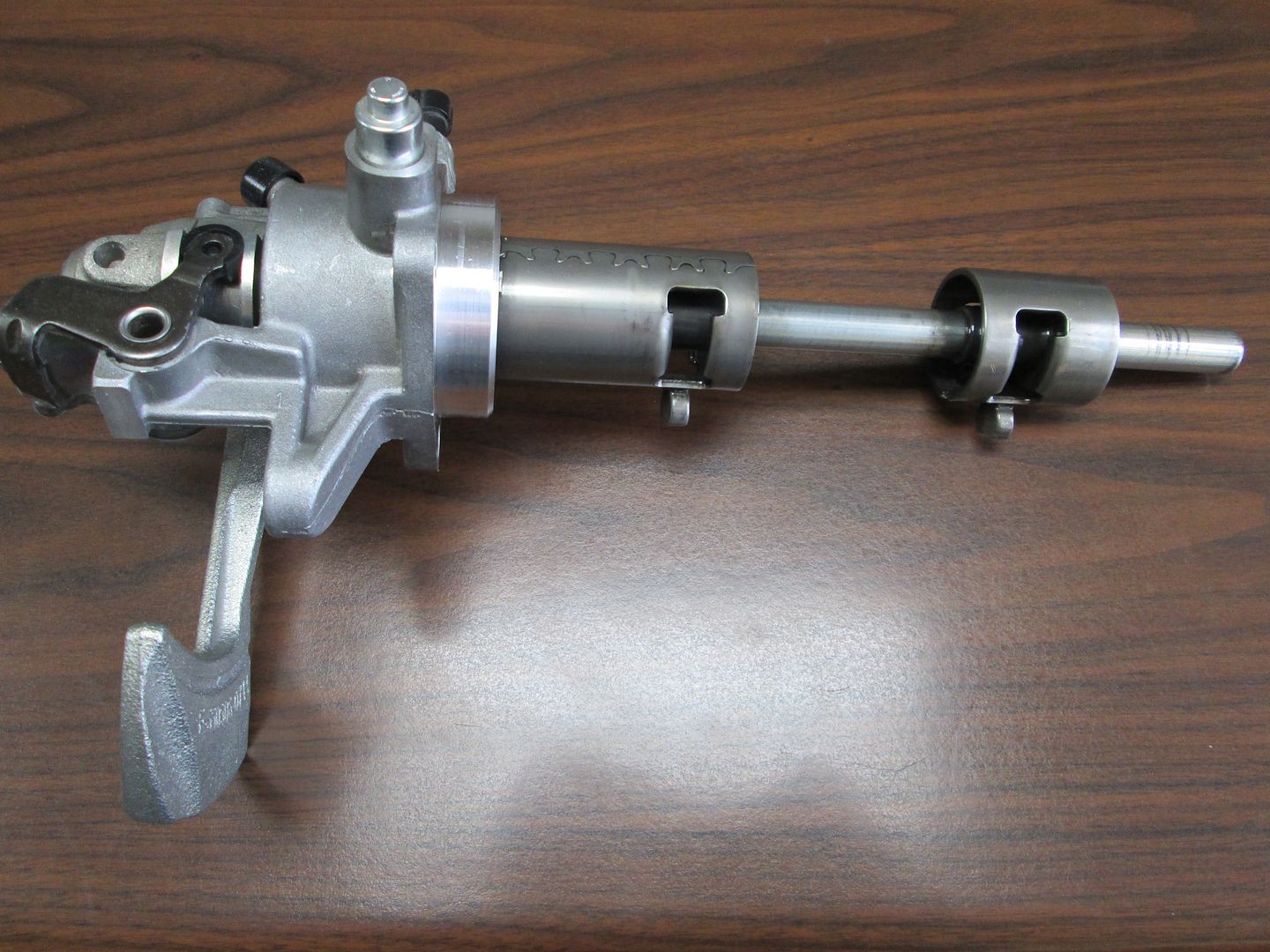
Within the shifter assembly, there is a pin that rides in a gated shift pattern:
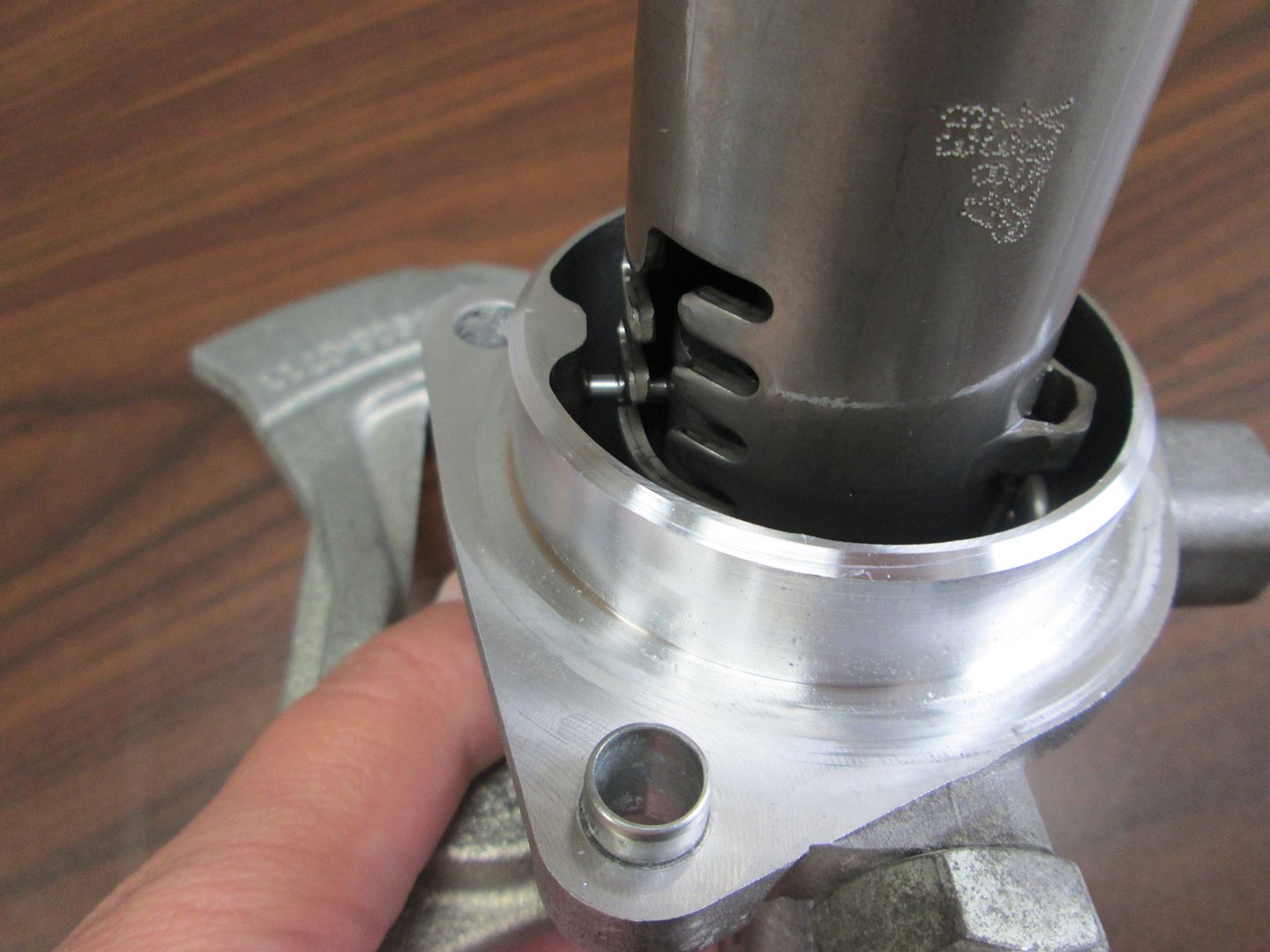
There is a ball detent that helps to self-center the shifter in the 3-4 gate, but the spring pressure to go into the 1-2 gate is less than what is needed to go into the 5-6 gate, so the self-center feature isn't as strong from the 1/2 gate as I would like. Unfortunately, its cause by the countour of the bracket the detent ball rolls around on, so not an easy fix to add more spring tension.
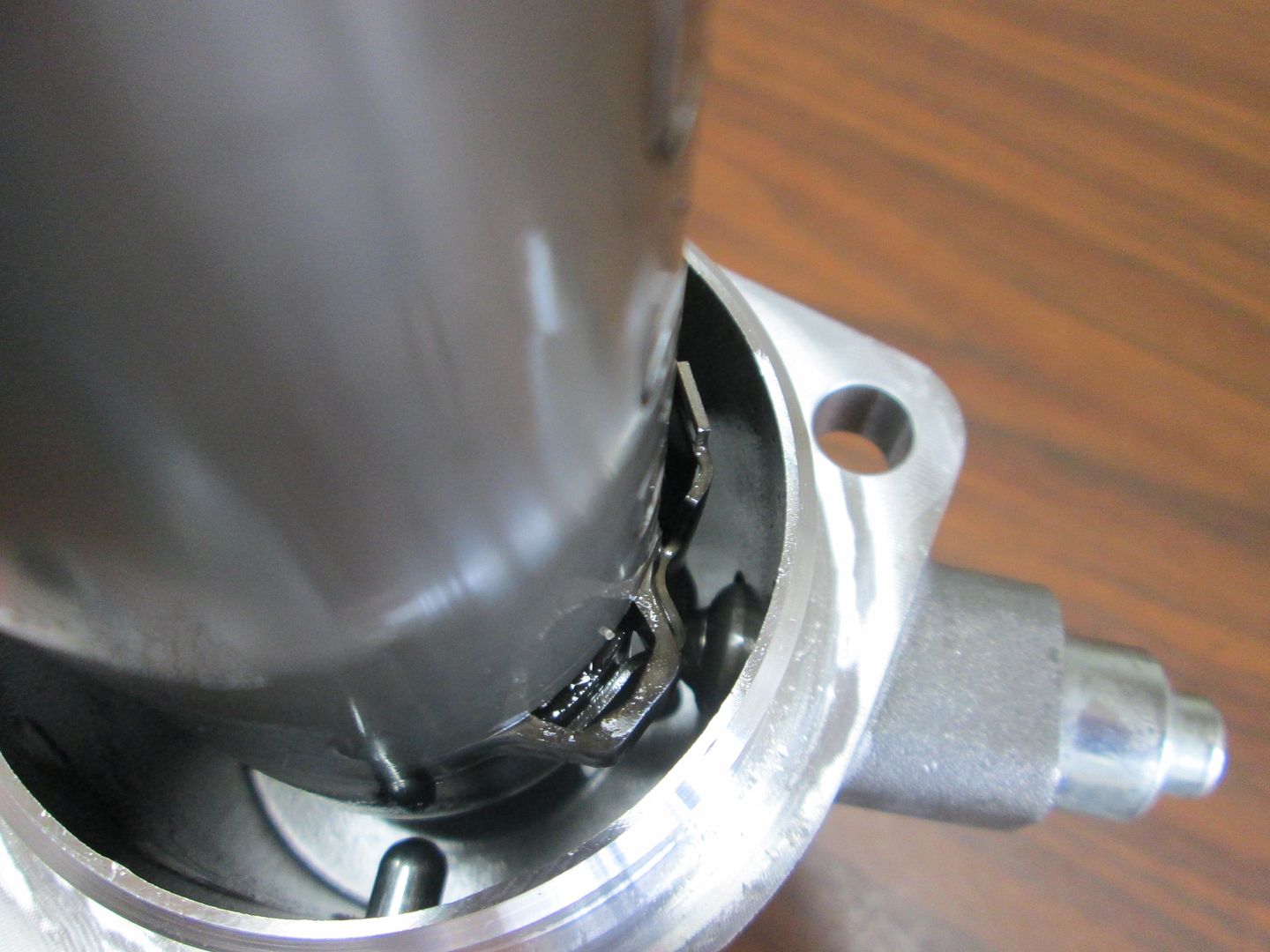
There are two of these tabs that engage the shift rails. Notice they are tapered on one side. I might want to increase this taper (and angle the gate for the pin) to allow the shifter to start sliding towards the 3-4 gate sooner (when pushed from 2nd). I may also taper the edge that could accidentally tap 5th so I wouldn't hit the edge of 5th while trying to get 3rd.
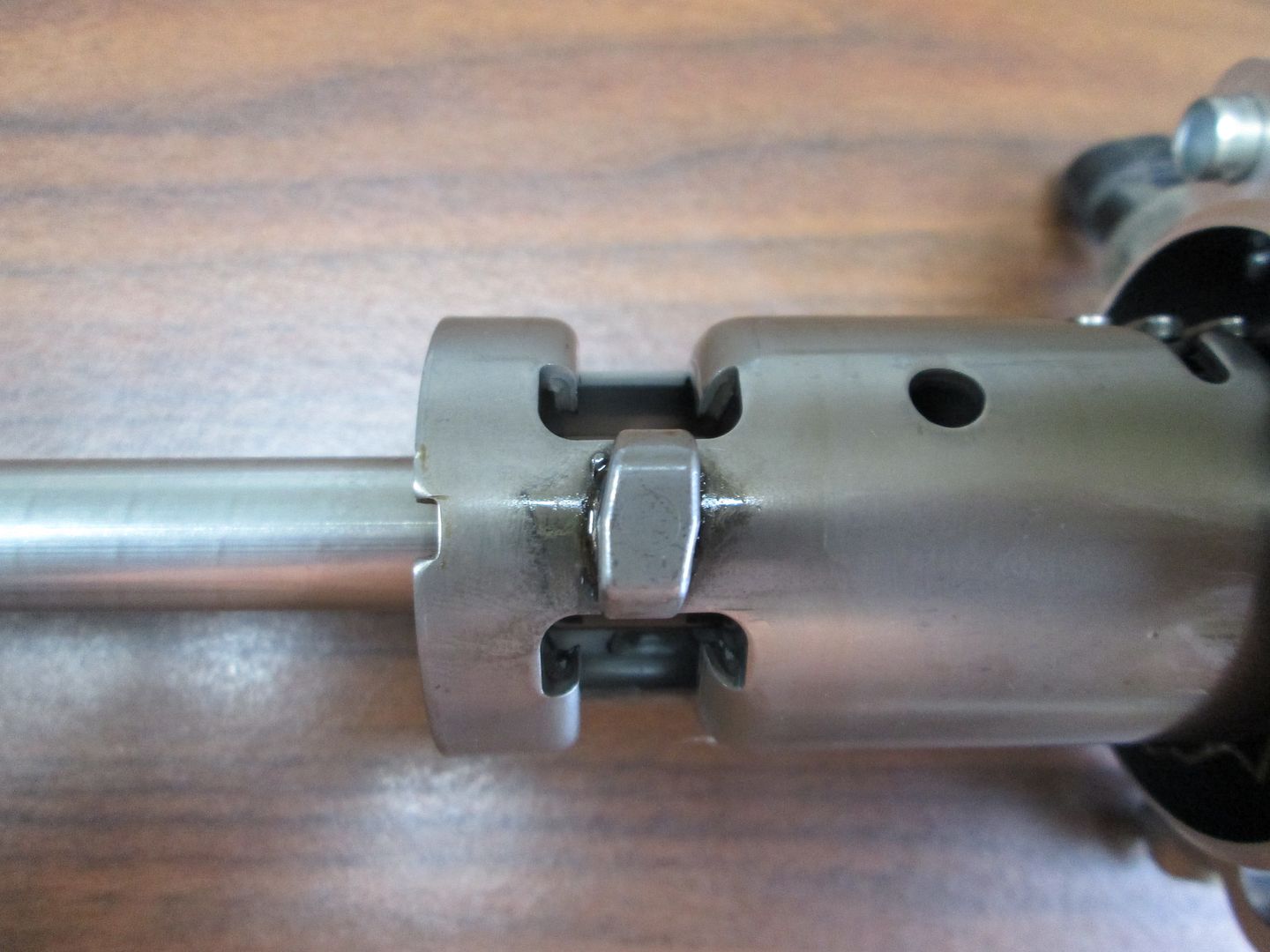 |
|
|
|
|
fieroguru
|
MAR 17, 08:29 PM
|
|
Here is another post that shows how much the ball end of the shift arm has to move to engage both odd and even gears. I never measured the other lever range of motion (or I can't find a post about it).
quote | Originally posted by fieroguru: Since the Getrag Select cable only has 1 3/4" range of motion, I went and checked the needed range of motion on the F40 (the one for the 4.3) and got 1 3/4" as well, but I need to take it again in a more precise manner.
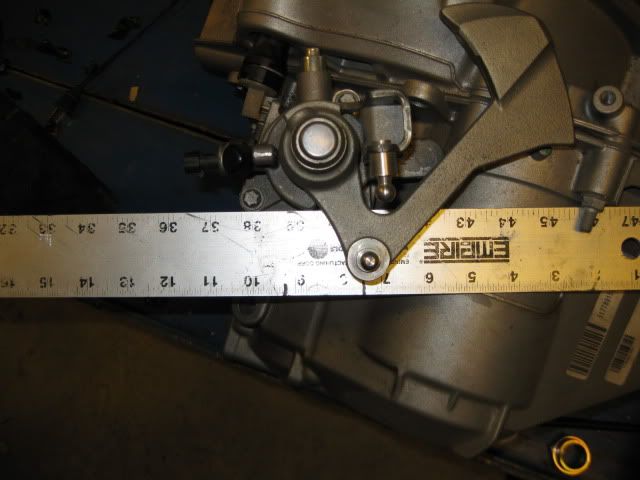
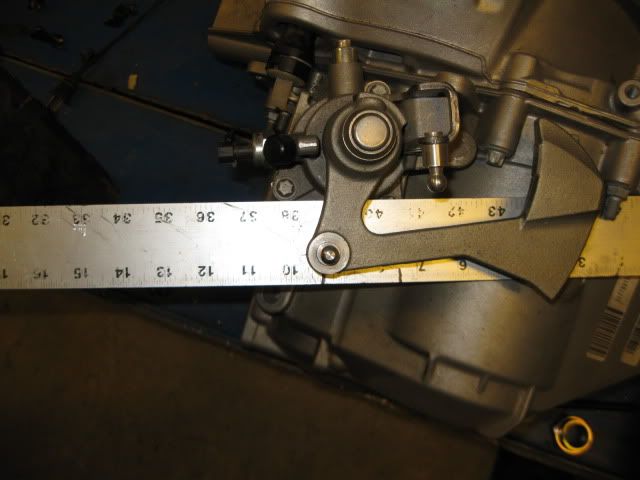
|
|
|
|
|
cman5302
|
MAR 17, 08:35 PM
|
|
quote | Originally posted by fieroguru:
Welcome to the forum!
Here is an old post of mine when I pulled the shifter mechanism from the F40. Basically there are two tabs that engage and disengage the shift rails for both the upper and lower main shafts. The main shift shaft rotated forward and back to select Odd or Even gears. It is pulled/pushed into and out of the transmission case to access R, 1/2, 3/4, 5/6.
|
|
This will be very useful, thank you!
|
|
|
pmbrunelle
|
MAR 17, 10:26 PM
|
|
Wouldn't it be better to take direct control of the shift forks, versus going through the XY gating mechanism?
|
|
|
cman5302
|
MAR 17, 10:31 PM
|
|
quote | Originally posted by pmbrunelle:
Wouldn't it be better to take direct control of the shift forks, versus going through the XY gating mechanism? |
|
Possibly. This is ultimately why I posted this question, to spitball for possible better ideas.
|
|
|
pmbrunelle
|
MAR 17, 10:40 PM
|
|
My opinion is that the direct control method will be easier to implement, in the sense that you won't have to deal with lining up with a pre-existing shift pattern.
With less slack, things work better as well.
For instance, you'll want some sort of position feedback corresponding to the movement of a shift fork. When you are "in-gear" or in neutral, you'll know if it's safe to re-engage the clutch. In the in-between zones, you should not engage the clutch.
If you can get direct measurements of the shift fork movements, your position feedback will be more accurate.
With the direct control method, some form of interlock should be implemented, to prevent two forks from being shifted out of neutral simultaneously (due to a software error). If this happens, you lock up the transmission.
With the XY method, you don't have the risk of a shifting into two gears at once.
Nevertheless, I would still lean towards the direct fork control method.
With a 6-speed, you have to manage alignment with four different gates... sounds like a challenge.[This message has been edited by pmbrunelle (edited 03-17-2022).]
|
|
|
Will
|
MAR 18, 04:20 PM
|
|
By manipulating the shift shaft outside the transmission (X-Y method), you keep all the internal components designed to prevent the transmission from going into two gears at once.
In using the X-Y method, you need two (maybe three for reverse) actuators. Since the shift shaft is spring loaded to center itself in the 3-4 gate, you only need a solenoid to pull it over to the 1-2 or 5-6 gates. Either a solenoid on the shift lever or a stepper on the shaft would then handle shifting into gear.
For the "direct acting" method, you'd need fairly specialized actuators (like two step solenoids) to be able to stop each shift collar in neutral when executing the 2-3 or 4-5 upshifts or downshifts.
In either case, shift mechanism position needs to be instrumented for feedback. The C7 Corvette does this, as the ECM knows which gear the transmission is in just from shifter position, without the vehicle in motion.
I always thought solenoids would be more appropriate for synchronized transmissions than hydraulics, as solenoids would apply force to the synchros, which would then work as normal until the transmission went into gear. Hydraulics like the OEMs use have to be carefully timed in order not to hammer the synchros and shift forks too hard.
|
|
|
pmbrunelle
|
MAR 18, 10:58 PM
|
|
quote | Originally posted by Will: I always thought solenoids would be more appropriate for synchronized transmissions than hydraulics, as solenoids would apply force to the synchros, which would then work as normal until the transmission went into gear. Hydraulics like the OEMs use have to be carefully timed in order not to hammer the synchros and shift forks too hard.
|
|
So, a human driver's muscular exertion is a quasi-constant force, but as the transmission drops into gear, force is reduced as the arm doesn't quite keep up.
Compressed air kind of mimics the human driver.
Downsides of compressed air are large piston areas (hard to package), and you don't normally have compressed air available on a passenger car.
I don't know about solenoids; I suppose that one would have to study the necessary shift force and travel to see if solenoids are a viable option.
quote | Originally posted by Will: For the "direct acting" method, you'd need fairly specialized actuators (like two step solenoids) to be able to stop each shift collar in neutral when executing the 2-3 or 4-5 upshifts or downshifts.
|
|
On the Eaton Endurant, double-acting air cylinders are used to push the shift rails either way. The air cylinder as such has no specific feature to define neutral.
Each shift rail has a spring+ball detent (as typically found in standard transmissions) to define the gear-neutral-gear positions.
By cutting off the air supply as the shift rail reaches neutral (see the importance of position feedback as already mentioned), it is enough to prevent going to the other side, in conjunction with the detent. I did study the possibility of discrete three-state rail position sensors, but it was preferred to use rail position sensors with a continuous reading.
Blocking rings give you some "insurance" against accidentally falling into the other side. A synchronized transmission cannot shift instantly, so as long as you don't keep pushing for too long on the wrong side, you won't fall into the wrong gear.
I don't know how things could/should be with hydraulic actuators.
********************************************************************************
The clutch is much more position-controlled, and not force-controlled.
This lends itself more to hydraulics, or an electric motor + ballscrew. Continuous position feedback is really needed here.[This message has been edited by pmbrunelle (edited 03-18-2022).]
|
|
|
fieroguru
|
MAR 19, 08:24 PM
|
|
Here are a couple more pictures to show the dual sets of shifter shafts:
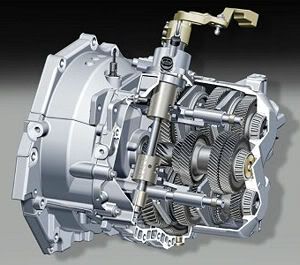

|
|

 |
|