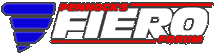

 |
2.5L Injector Flow Rate (Page 1/2) |
|
TGYK256
|
DEC 28, 01:04 PM
|
|
I have a mostly bone-stock 1985 Fiero SE equipped with a 2.5L duke. I am currently in the process of a custom ECM swap to a speeduino. I have a running base tune but would like to make sure I am building on a solid foundation. After weeks of searching, I have come up with no solid answers to the main question: What is the flow rate for the stock TBI fuel injector used in the TBI300 1bbl throttle body?
I have seen a few reports that the Fiero used a 60lb/hr injector. If this is true, is that 60 lb/hr at the 13 psi that the Fiero’s fuel pressure regulator runs at, or at some other pressure? This value is fairly critical for proper tuning, and being a TBI system, it would not be the easiest thing to measure myself without removing the throttle body entirely.
Any help is appreciated!
|
|
|
theogre
|
DEC 28, 03:08 PM
|
|
What "custom" ECM for any duke?
Duke l4 Fuel Pressure is 9 to 13 psi. And many don't see upper limit. Worse many barely get 9 often because of iffy pump and plumbing. So check actual system pressure. See https://www.fiero.nl/forum/Forum2/HTML/146121.html TBI Test Adaptor for Duke etc. https://www.fiero.nl/forum/Forum2/HTML/146240.html J30R10 intank fuel hose.
Fuel Pump Pressure Max is only ~ 15-19 psi because wants to keep just enough pressure to keep the regulator open some so has constant flow because that overflow is coolant and lube to the pump.
Don't have other data.
Unless you mod the whole engine and need more fuel/air mix at all RPM, won't get much or any more power. GM programs the ECM for nearly highest power most engine setups make.
Examples: 1 problem w/ most Fiero is TB/TBI can't reach WOT "flooring" the gas pedal. So unless you check/fix that the "speeduino" has same problem. Is bad w/ most Fiero from the factory and only gets worse as pedal, cable, and other parts wear. Often Far worse when have to add ADA equipment to drive because of a problems called Tolerance Stacking. Highlights See my Cave, Throttle Cable
Holley made TBI w/ bigger throat years ago that didn't do much w/o several other mods and even then didn't do much but take a lot of money.
Nearly all "Chips" make years ago to "Improve" OBD1 engines mostly did nothing or worse just wasted fuel because many ran super rich and adjusted O2 etc numbers to hind this. Many disabled data streams too so ECM scanners can't see.------------------ Dr. Ian Malcolm: Yeah, but your scientists were so preoccupied with whether or not they could, they didn't stop to think if they should. (Jurassic Park)
The Ogre's Fiero Cave
|
|
|
TGYK256
|
DEC 28, 03:21 PM
|
|
quote | Originally posted by theogre:
What "custom" ECM for any duke?
Duke l4 Fuel Pressure is 9 to 13 psi. And many don't see upper limit. Worse many barely get 9 often because of iffy pump and plumbing. So check actual system pressure. See https://www.fiero.nl/forum/Forum2/HTML/146121.html TBI Test Adaptor for Duke etc. https://www.fiero.nl/forum/Forum2/HTML/146240.html J30R10 intank fuel hose.
Fuel Pump Pressure Max is only ~ 15-19 psi because wants to keep just enough pressure to keep the regulator open some so has constant flow because that overflow is coolant and lube to the pump.
Don't have other data.
Unless you mod the whole engine and need more fuel/air mix at all RPM, won't get much or any more power. GM programs the ECM for nearly highest power most engine setups make.
Examples: 1 problem w/ most Fiero is TB/TBI can't reach WOT "flooring" the gas pedal. So unless you check/fix that the "speeduino" has same problem. Is bad w/ most Fiero from the factory and only gets worse as pedal, cable, and other parts wear. Often Far worse when have to add ADA equipment to drive because of a problems called Tolerance Stacking. Highlights See my Cave, Throttle Cable
Holley made TBI w/ bigger throat years ago that didn't do much w/o several other mods and even then didn't do much but take a lot of money.
Nearly all "Chips" make years ago to "Improve" OBD1 engines mostly did nothing or worse just wasted fuel because many ran super rich and adjusted O2 etc numbers to hind this. Many disabled data streams too so ECM scanners can't see.
|
|
The “Custom” ECU is just that: It is a Speeduino. A fully-mappable EMS based off of an Arduino mega 2560. It uses the same tuning software that a microsquirt or megasquirt does. My project completely replaces the antiquated 37 year old ECU with something faster and modern.
My question is less about running fuel pressure but more about the flow rate of the injector. In order for the EMS to do proper calculation of base pulsewidth for required fuel from the injector, an accurate maximum flow rate must be known. All other fuel mapping and corrections are based off of this base pulse width - I can “make it work” with an inaccurate guess, but it would not be a good tune.
|
|
|
pmbrunelle
|
DEC 28, 03:45 PM
|
|
I don't think it's of utmost importance, but if you're wanting a precise value, you'll only have confidence in the number if you measure it yourself with the TBI over a measuring cup.
Perhaps more critical than static flow rate is to characterize the dead time of the injector. With different electrical pulse widths, you can work out the dead time. Do this at a normal running voltage and at battery voltage.
|
|
|
theogre
|
DEC 28, 05:09 PM
|
|
The system Pressure affect Flow Rate. If injector tested for flow on a bench @ 13psi but car only makes 9... hope the new code can handle the low pressure causing low flow.
TBI can run w/ pressure out of range but ECM and Engine will have problems...
Example: Having system pressure > 13psi for problems like block/crushed return line then ECM pegs BLM and Integrator and often trips DTC 45 Engine Rich because O2 sensor stay above 0.5v too long or all the time. You can watch all that happen on an ECM scanner.
|
|
|
TGYK256
|
DEC 28, 05:29 PM
|
|
quote | Originally posted by pmbrunelle:
I don't think it's of utmost importance, but if you're wanting a precise value, you'll only have confidence in the number if you measure it yourself with the TBI over a measuring cup.
Perhaps more critical than static flow rate is to characterize the dead time of the injector. With different electrical pulse widths, you can work out the dead time. Do this at a normal running voltage and at battery voltage. |
|
Characterizing injector dead time is on the list of things to do but at this time I need to know the flow rate of the injector for the BPW to build off of in the tune. It is one of the constants that are needed for proper control of fuel delivery and correction.
quote | Originally posted by theogre:
The system Pressure affect Flow Rate. If injector tested for flow on a bench @ 13psi but car only makes 9... hope the new code can handle the low pressure causing low flow.
TBI can run w/ pressure out of range but ECM and Engine will have problems...
Example: Having system pressure > 13psi for problems like block/crushed return line then ECM pegs BLM and Integrator and often trips DTC 45 Engine Rich because O2 sensor stay above 0.5v too long or all the time. You can watch all that happen on an ECM scanner. |
|
The ECM that I am using does not operate with traditional INT/BLM or fuel trims. It can operate using EGO corrections but that doesn’t fix a bad tune. This ECM can also adjust the pulse width of the injector based off of fuel pressure by way of a pressure sensor, but it can only do so accurately and precisely when the flow properties of the injector(s) are known. This is exactly why within my original question I asked for flow rate of the injector and the pressure that rating is for. I can calculate the flow rate the injector will be operating at if I have a known rating to work from.
That being said, the fuel pump has been replaced and I am getting an accurate 13 psi across all RPM ranges- The pump itself is rated at 20psi static pressure and the regulator internal to the TB is returning everything above 13 to the tank.
|
|
|
TGYK256
|
JAN 06, 10:17 PM
|
|
SO! I did some programming to add an injector test-mode to my ECM. Through my testing, I found the injector dead-time to be at about 9ms @ 11.943v and 7ms @ 14.943v (My battery charger runs a bit high on the voltage side of things.)
I then performed a flow-test with these parameters: 1000 pulses at 10ms on-time, 2.5ms off-time for an 80% duty cycle. I didn't want to push it much higher for fear of damage to the injector.
I measured 83-84 ml of fuel flowed during these tests, consistently..
Doing the math, this comes out to a 1660 cc/min or 152 lb/hr injector. It doesn't seem likely, but I have gone over my code as well as the math multiple times, and can find no errors. The math is as follows:
10ms on-time - 7ms of dead-time = 3ms of fuel flowing 1000 pulses * 3ms of fuel flowing = 3s total fuel flowing 83ml of fuel collected / 3s of flow = 27.67ml/s of flow 27.67ml/s of flow * 60s (one minute for cc/min rate) = 1660 ml/min
1cc = 1ml, so my flow rate is 1660cc/min
I can also report that using these numbers in my tune makes the car much easier to start, as well as much more responsive and stable with changes to the VE map. Unless someone can provide rated numbers for what these injectors actually provide for flow rate at pressure, I am forced to embrace the results of my test. If anyone programming-savvy goes through my code and can spot any errors, I am open to feedback! It certainly would help solve the mystery of such a highly-rated injector.
I hope that these results can help someone else out there!
|
|
|
sanderson231
|
JAN 08, 02:37 PM
|
|
The GM part number for the Duke throttle body injector is 17068993. Contact Motor Man Fuel Injection Supply and they can tell you the capacity if you can't find it elsewhere:
https://www.motormanfuelinj...on.com/web_page.html
As a sanity check, the heating value of gasoline is about 17,500 btu/lb and the Duke makes about 92 hp. 1 hp-hr is 2544 btu's. So 92 hp * 2544 btu/hp-hr = 234,048 btu/hr. 234,048 btu/hr / 17,500 btu/lb = 13.3 lbs/hr. The thermal efficiency of the engine is probably no better then 25% at full throttle, so 13.3 / 0.25 = 53.5 lbs/hr.
Another way to look at it is that a 4.9L Cadillac makes 200 hp and uses eight 19 lb/hr injectors. So ratioing to 92 hp - 92 / 200 * 19 * 8 = 70 lbs/hr
An injector capacity of 152 lbs/hr sounds high
------------------ formerly known as sanderson 1984 Quad 4 1886 SE 2.8L 1988 4.9L Cadillac 1988 3800 Supercharged[This message has been edited by sanderson231 (edited 01-08-2023).]
|
|
|
edfiero
|
JAN 10, 08:42 AM
|
|
Here are some flow rates of all the GM TBI injectors. Note the Fiero injector is missing. As I recall the Fiero injector is about 60 as you have guessed. If there in any doubt, you can always get a new 5.7 injector as a replacement and then tune as needed.
xxxxxx - color / color - 33pph - 2.8l and 3.1l
xxxxxxx - color / color - 45pph - 4.3l engine NOTE: Some came with 2 differant size injectors?
5235279 - White / Green - 54pph - 5.0L / 305 Cars/Trucks
5235206 - Orange / Black - 61pph - 5.7L / 350 Cars/Trucks
17084327 - Yellow / Brown - 65pph - 5.7L / 350 Police Package
17084304 - Black / Blue - 74pph - 7.4L / 454 - 91-93
5235231 - Red / Blue - 80pph - 7.4L / 454 - 88-90
17104288 - Pink / Purple - 46pph @13psi - 7.4L / 454 - 94-95 *NOTE: Came with 30 PSI regulator used @ 26-32psi for 67-72pph
|
|
|
TGYK256
|
JAN 10, 01:55 PM
|
|
quote | Originally posted by sanderson231:
The GM part number for the Duke throttle body injector is 17068993. Contact Motor Man Fuel Injection Supply and they can tell you the capacity if you can't find it elsewhere:
https://www.motormanfuelinj...on.com/web_page.html
As a sanity check, the heating value of gasoline is about 17,500 btu/lb and the Duke makes about 92 hp. 1 hp-hr is 2544 btu's. So 92 hp * 2544 btu/hp-hr = 234,048 btu/hr. 234,048 btu/hr / 17,500 btu/lb = 13.3 lbs/hr. The thermal efficiency of the engine is probably no better then 25% at full throttle, so 13.3 / 0.25 = 53.5 lbs/hr.
Another way to look at it is that a 4.9L Cadillac makes 200 hp and uses eight 19 lb/hr injectors. So ratioing to 92 hp - 92 / 200 * 19 * 8 = 70 lbs/hr
An injector capacity of 152 lbs/hr sounds high
|
|
You are likely right. I believe my timing may be off by an order of magnitude. Re-doing the calculations with 100ms pulsewidth instead of 10ms and a dead-time of 70ms instead of 7, I get a flow rate of 15.99 lb/hr. Adjusting to rated pressure of 3 bar gives a rated flow rate of about 53 lb/hr.
This does raise the question: why is the injector dead time so high? I tested at what I thought was 6.9ms but what might have been 69 ms, and got no flow, but at 7.0 (possibly 70) it flowed fuel.
I will be digging into the test mode code and debugging later this week.
|
|

 |
|