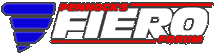

 |
Electric window motor upgrade how to. (Page 1/1) |
|
hercimer01
|
JUL 27, 10:49 PM
|
|
|
|
Dennis LaGrua
|
JUL 28, 02:27 AM
|
|
The Tahoe motor certainly helps improve the window function and that was good instruction that you posted. I am also a believer in disassembling the door skin when you replace the window motor but sometimes the quick fix by just applying Silicone spray to the window tracks improves the up down motion. The issue these days is that many of the window motor replacements are of poor quality. My son replaced one window motor recently and it had burned out within a year. That brings up the question of what brand of motor will last? ------------------ " THE BLACK PARALYZER" -87GT 3800SC Series III engine, custom ZZP /Frozen Boost Intercooler setup, 3.4" Pulley, Northstar TB, LS1 MAF, 3" Spintech/Hedman Exhaust, P-log Manifold, Autolite 104's, MSD wires, Custom CAI, 4T65eHD w. custom axles, Champion Radiator, S10 Brake Booster, HP Tuners VCM Suite. "THE COLUSSUS" 87GT - ALL OUT 3.4L Turbocharged engine, Garrett Hybrid Turbo, MSD ign., modified TH125H " ON THE LOOSE WITHOUT THE JUICE "
|
|
|
theogre
|
JUL 28, 10:49 AM
|
|
⚠️ Warning: 1. You need much "hotter" iron/gun to solder heavy wire then most have. 50-100 watts minimum to make a good joint w/o big problems that can, often will, fail later. Like "Weller type" guns have 90 to 140 watts that puts a lot of heat on/in a joint before the copper can heat sink the spot.
Also: Do Not use Lead Free Solder. Most require More Heat to melt that makes this job harder. Some areas or countries now block lead solders to sell to most to all users but can find it in flea markets etc.
2. Mashing the ends then "tying" wires like above is not correct & can Fail. More so on "cold" joints that results using under power irons/guns etc. Can twist ends to get mechanical connection then solder. Example: a Short version of this type twisting... "Western Union splice" Or Use non insulated crimps then solder.
3. Flux Core Solder often doesn't get to inner wires for big joints to work. Again more so w/ under power irons/guns. Flux core often doesn't have enough flux so needs standalone Rosin or other non-acid flux or have heat problems... flux etc too cold doesn't work, too hots & flux burns before solder works. Second issue common to torches heating whatever to solder.
You can use "tinning" flux that mixes low temp solder in a flux. This will tin fast to see when flux is working. Again, Make sure any flux isn't acid flux.
4. You need "weather/water proof" shrink tube that has "glue" inside. Doors are very wet areas & joints unprotected will corrode not only attack @ the joint but "water" will wick under the rest of insulation & rot more wire.
5. That's assuming OE & other wires can be cleaned to solder. Many OE stranded wires already have some crap/corrosion/oxides that is near impossible to remove then fluxes fail, more so flux core solder, to clean & solder doesn't work even if "Passes" a pull test right now.
Or...
● Use "water proof" crimps but need right crimper + adjusted right too so won't cut the sleeve but crimp tight to work then heat the tube to shrink & seal. Use 3M crimps or other real brands. Most don't crimp enough joints to "save money" on no-name crimps but often they are cheap for many reasons & Fail now or later because weak metal used to make them. ● Use Posi-Tite for 20-18 or 14-16 awg wires. Maybe can use Posi-Lock w/ some silicone or permatex green brake grease to keep out water since is not directly flooded.
But these 2 often hate old wires too for same reason you can't clean to solder. Posi-Lock/Posi-Tite might help because how they work & like many other connections forces the metal to metal contact to "wipe" the crap off if not badly dirty/rotten.
"Doors are Wet zones?" Yes. Even w/ brand new "dew wipes" allows the water & worse will get on most of the door parts when it rains etc. because dew wipes & other external parts don't seal very well or not @ all. Is why most doors have "water proof paper" or plastic on inner door to protect the inner trim etc.
If other plugs in a door are not "water proof" like Metripack or weather pack then use silicone, brake grease or bulb grease on them.
------------------ Dr. Ian Malcolm: Yeah, but your scientists were so preoccupied with whether or not they could, they didn't stop to think if they should. (Jurassic Park)
The Ogre's Fiero Cave[This message has been edited by theogre (edited 07-28-2024).]
|
|
|
hercimer01
|
JUL 28, 04:10 PM
|
|
quote | Originally posted by theogre:
⚠️ Warning:
|
|
With all due respect Ogre, (another name for a Troll)
I have been certified in electronic solder repairs since 1986 by the US government. (Mil Spec 2000 in the US Navy) and currently J-STD-001 for Collins Aerospace, Woodward Inc, and many other aerospace and defense companies. I am well trained in ALL types of electric repairs.
I don't appreciate you trolling my thread here and hijacking it regardless of your sentimental connection to Fieros or this Forum. If you have an input here that contradicts anything I put out publicly, I would be more than open to discuss it with you privately in a PM.
You have been less than respectful or relevant in this case, mind your own business please.------------------ Project Genisis Lo Budget 3800SC swap SOLD 12.840@104.8 MPH Intense-Racing 1.9 rockers, 3" exhaust, 3.4 pulley, ZZP tune and 18 year old tires.
88 Coupe under construction SOLD
88 formula 3.4L 4t60 swap SOLD 88GT resurrection in progress.
|
|
|
hercimer01
|
JUL 28, 07:00 PM
|
|
|

 |
|