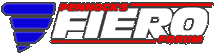

 |
Brakes for a freewheel conversion (Page 1/1) |
|
MidEngineManiac
|
APR 07, 05:09 PM
|
|
I am giving up on this sub-assembly.
3 days in an electrolysis tank. A week and can worth of PB Blaster poured into it. One destroyed deadblow hammer.
It aint coming loose. It is so rusted from years outside that it is now one solid hunk internally. Even the freewheel is now a solid piece.
OK, I can easy convert the back hubs to freewheel. Grind off 3 little drive nubs, 4 new bearings, and thats the end of that problem. Wheels spin freely. Since the bike has a front-drive hub motor I dont really NEED a powered rear axle. It was just a "nice to restore" item. Not ging to bother trying to find another one since it's just another 40-year-old assembly with likely the same problems. And it's cheaper to just buy a whole new trike than to get a replacement rear.
The problem I now need to solve, is rear braking. From the factory it had a band brake with a drum on the axle, which equally stopped both wheels. That wont work anymore and there just isnt enough stopping power on front alone.
Can anybody think of a way thats NOT butt-ugly to get some sort of structure around the wheel so can use regular rim brakes via an equalizer cable ?
Thats what I have to start with. Grind off those 3 nubs, and any structure has to be based around that bracket (with some sort of top brace as well, of course) and an axle mount on the outside.
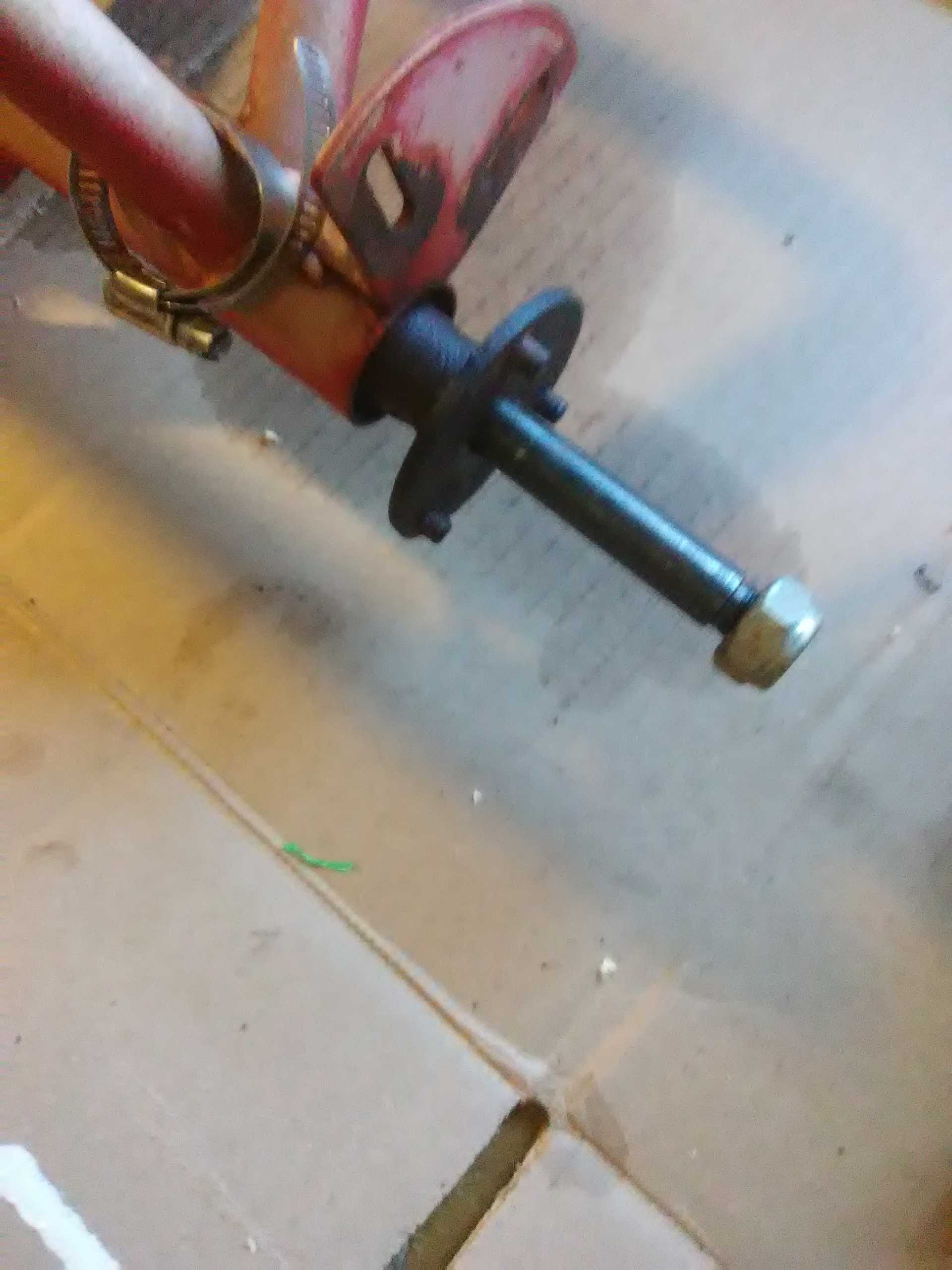
|
|
|
theogre
|
APR 07, 07:52 PM
|
|
Use some heat to expand outer tube. Don't heat to burn paint off or even hotter.
If have a Dif or Chain drive 1 real wheel? 1 wheel then have 1 long axle and can jam whole thing or only part of outer tube. Plus may have 4 bearing at ends and middle fighting you trying to beat the axle out.
⚠️ Warning: Front hub motors can break the fork for bike not made for them or even getting "BMX" and other abuse. More so w/ tric's because have more total mass.------------------ Dr. Ian Malcolm: Yeah, but your scientists were so preoccupied with whether or not they could, they didn't stop to think if they should. (Jurassic Park)
The Ogre's Fiero Cave
|
|
|
williegoat
|
APR 07, 08:42 PM
|
|
quote | Originally posted by MidEngineManiac:
The problem I now need to solve, is rear braking.
|
|
Use disk brakes. The caliper mount would be so mush easier to fabricate.
Just google: "bicycle disk brake kit"
 [This message has been edited by williegoat (edited 04-07-2023).]
|
|
|
MidEngineManiac
|
APR 07, 08:43 PM
|
|
The forks are 30", made from 2 sets of MTB forks, inner sleeved then mig-spliced together, PLUS one hell of a hefty (1/4" plate) brace between the 2 sets. Plus dual torque arms going on. Plus 1/8 angle-iron "fairings" as reinforcements going on before it all gets leather wrapped. That part of the project I am not to worried about. I actually overbuilt for the weight to help with traction on the front drive. I'm NOT into burning off a tire every 2 weeks because it's too light up front.
I've ridden a few factory front-drive and that was the biggest problem. They are a hoot especially off-road on fields, but unless you are constantly leaning forward the drive wheel just wants to slip.[This message has been edited by MidEngineManiac (edited 04-07-2023).]
|
|
|
MidEngineManiac
|
APR 07, 08:52 PM
|
|
Caliper mount would Willie, but not the disk. bearings are 6202 for the wheels. I'd have to get REAL funky for some kind of disk mount that would fit the hub and still clear the bearings. I was already playing around with the idea since I got a couple disks kicking around. OTOH, I dont happen to have a lathe or mill 
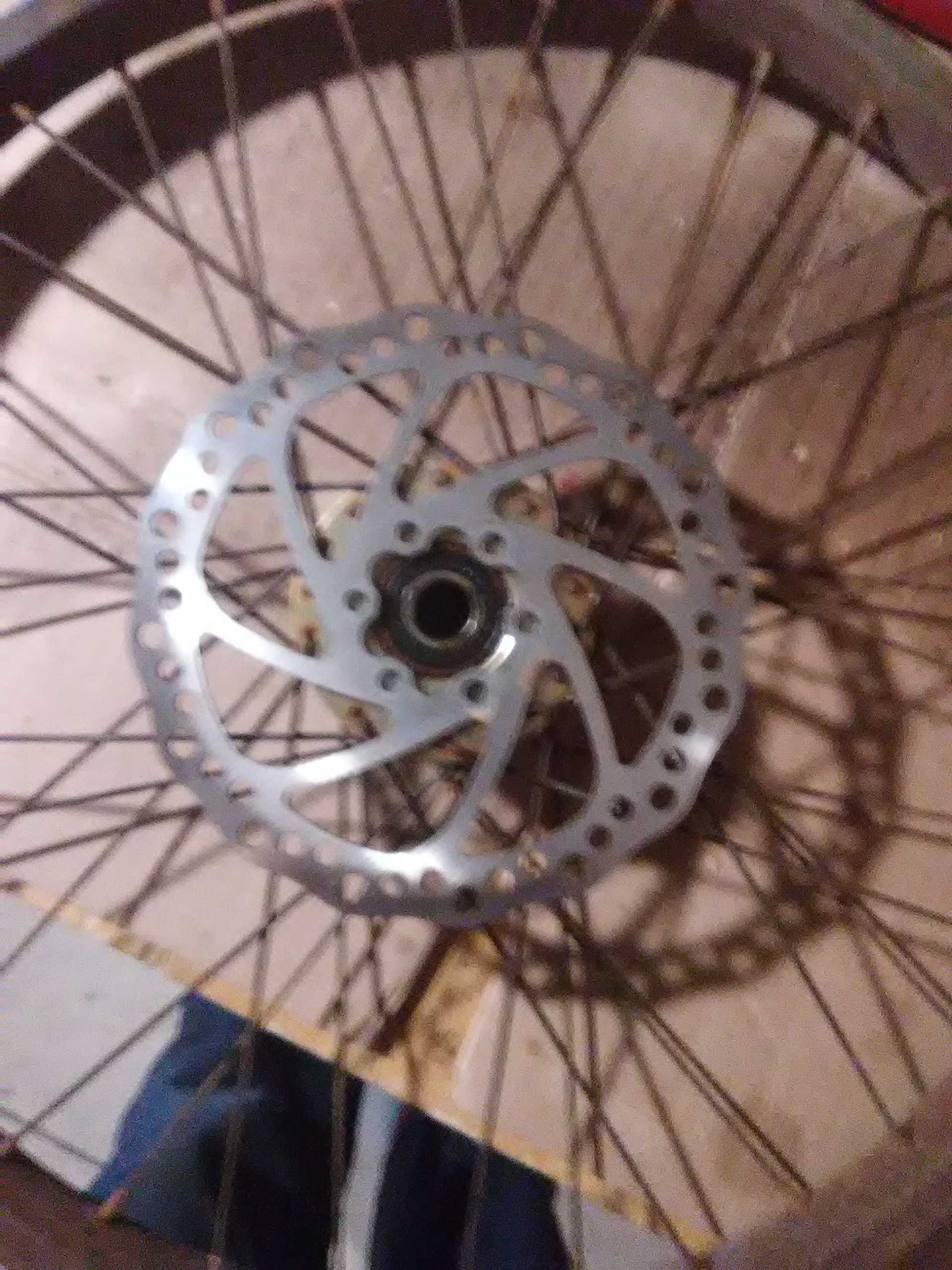 [This message has been edited by MidEngineManiac (edited 04-07-2023).]
|
|
|
williegoat
|
APR 07, 09:01 PM
|
|
quote | Originally posted by MidEngineManiac:
Caliper mount would Willie, but not the disk. bearings are 6202 for the wheels. I'd have to get REAL funky for some kind of disk mount that would fit the hub and still clear the bearings. I was already playing around with the idea since I got a couple disks kicking around. OTOH, I dont happen to have a lathe or mill 
|
|
There are plenty of cheap hub conversion kits, flanges and complete hubs.[This message has been edited by williegoat (edited 04-07-2023).]
|
|
|
MidEngineManiac
|
APR 07, 09:15 PM
|
|
|
|
cliffw
|
APR 08, 10:11 AM
|
|
quote | Originally posted by theogre: Use some heat to expand outer tube. Don't heat to burn paint off or even hotter.
|
|
Ding ding ding, we have a winner ! As usual.
Mid Engine Maniac, your assembly is "rust welded" together. I worked the oil fields on BIG metal parts which sometimes got rust weld. We used to call out professional welders to heat parts with a rose bud.
I am not sure why theogre suggested mere warming. Using heat is an art. Heating the inside component will make it "tighter". theogre is correct. Do not over heat.
Also, it is not a task where you heat it up and whaa-laa. It is a step by step process. Best interrupted by a few blows with a hammer, removing the shaft a little bit, and sinking it back in. Repeat as needed, including heat. PB Blaster applied between steps may not help, but it sure won't hurt, . Be patient. Give the PB time to work.
I am not sure what tool one might use to ... A hammer drill with the right "bit" would drive it way in there. Removing it, ?
In the oil fields, we also un-welded rusted various stuff by leaving it "marinating" in diesel for ...
|
|
|
theogre
|
APR 08, 08:01 PM
|
|
quote | Originally posted by cliffw: I am not sure why theogre suggested mere warming. Using heat is an art. Heating the inside component will make it "tighter". theogre is correct. Do not over heat.. |
|
Because above pics doesn't show big outer "pipe" use for axle support on most tric's. Not just Diam but long Length can hurt you. Big tube is often 10" or more long x 2 for both sides. So if 1 or both outers are rust welded to the axle your heating a big area.
Just warming to 200-250°F on the outer tube can expand enough to loosen. Note: If is powder coated then 250°F may melt it again while Commercial paint may survive. Then heated tube can suck oil in far deeper as it cools. If needed just repeat a few times over a weekend or more time to allow the oil to work.
Very easy to over heat and wreck the whole rear. Many Tric's have same design w/ rear section as 1 welded part bolted to a "normal" bike. Many fronts are normal bike while others have mod's to last longer as a Tric.
Could be "just" the Bearing are jammed and holding the axle... If true then maybe have clips etc to restrict axle and/or bearing moving at different spots on the axle or outer tubes.
|
|
|
MidEngineManiac
|
APR 09, 12:10 PM
|
|
Thanks Ogre. Yeh, that pic doesnt show it all
Cliff the way these things are built, is the 2 outer tubes on the spreaders for a frame. Into that goes 2 slightly smaller tubes (1 each side) with those engagement drive hubs. Through the center of that goes a 5/8" x 30" keyed solid shaft (the actual axle). It's all centered with bearings (2 or 3 each side) and spacers, plus assorted keys and freewheel mechanisms.
So actually, there could be (depending on the unknow arrangement inside) up to 20 individual "rust welds' holding that long axle in there. TBH in the past I would have solved it by zip-wheeling the outer tubes, rebuilding the innards, then welding the tubes back together for assembly. One of those job types that's now a no-no with a spare-bedroom shop space. In theory I suppose I could do that quietly-dont-get-caught-like with a dremmel wheel and JB weld to put it back together, then some stainless clamps to reinforce but I dont really trust the epoxy for that.
Already solved the brake-mount problem. There is a guy on another forum that built one with a back "bumper" going full width. Doesnt look bad at all, can double as a trailer hitch point, and would work perfect to mount calipers too. One of these lets me pull 2 calipers with one handle. That puts a little weight where I dont want any (behind the axle) but only 3-5 pounds or so.
https://www.saccon.it/index...LGIDC=55&CTLGIDP=161[This message has been edited by MidEngineManiac (edited 04-09-2023).]
|
|

 |
|