|
|
|
Any and all things 3.4 DOHC........... by pavo_roddy
Started on | : 11-22-2006 12:30 AM |
Replies | : 1247 (67877 views) |
Last post by | : fliphone on 01-06-2024 02:30 PM |
|
|
|
Dec 19th, 2006
|
procarnut Member Posts: 622 From: Blum, Texas USA Registered: Mar 2006
|
You should be able to reach him during business hours. That was his work number I sent you so any time will work.
I have to step out for a while so I'll check back later.
Bob
|
01:51 PM
|
|
Emc209i Member Posts: 3091 From: Charlotte, NC Registered: Apr 2005
|
Total ratings: 225
User Banned
|
|
He had to make a run and I never could get him.
I think I may have to go with the SPEC because my project manager (father) wants me to go SPEC because of their rep for lasting. Nothing personal but I agree with him. Being that I'm trying my very hardest in school I don't have as much time to pull the transmission back out incase the non kevlar pucks wear down before the Kevlar pucks do. I'll try to call him tomorrow and ask him about what he thinks about durability.
|
04:56 PM
|
|
Dec 20th, 2006
|
procarnut Member Posts: 622 From: Blum, Texas USA Registered: Mar 2006
|
Hey, not a problem. Everyone has to decide for themself. I have gotten alot of opinions here at the forum and I would have to say I didn't follow what other people told me. Sometimes it bites me but most of the time it doesn't. In my situation its like reading a book over and over, even when you think you know all the details of a book, a second look hails more enlightenment. Although not as much as the first time, you have to keep researching even if the information is minotinous, that is where it gets harder to learn something new. I don't hold it against anyone for not listening to me, after all they may fined something new that may work better than before. In any case I try to keep my eyes open for new things and hope that someone else has already experimented with what i may do next.
|
12:25 AM
|
|
SKIDMARK Member Posts: 1350 From: Chardon, Ohio, USA Registered: Sep 2001
|
| quote | Originally posted by Emc209i:
So what's the best route of action then? Buy a bunch of pipes (bent and straight) and then have a welder simply weld the system together? I don't know how to weld like a pro, I've done it before in High School, so I would rather someone with some skill build it. I know several really good welders around here that would be glad to help me out with a favor, but is there a conclusive list of the pipes needed and lengths?
I guess I'm saying where the hell do I buy the pipes (mandrel 2.5). I'm great at reproducing things I just can't weld, so I could make all of the cuts and take the pipe to be welded together.
Where's a good place to get pipe, and how much is mandrel bent (quality, not going to rust) piping?
I want to save myself money if possible but I want good parts. Any suggestions besides where to buy the pipe?
|
|
Buy a little MIG welder and learn to use it.....it's something you'll be glad you did for the rest of your life. Another handy tool is a sawsall. You can get the stainless pipe off of ebay or here WWW.PERFORMANCE-CURVE.COM for pretty reasonable money. Total for my exhaust is less than $250 but it was a lot of work. Prior to this project I never welded stainless and I learned a lot about it just by doing it. I don't like to pay someone for something I can do for myself....that's just me. If you really don't want to take the time to do it yourself, there are many exhaust places that will fabricate a complete mandrel bent exhaust system for you but most want to do it on the car which means you have to get the engine installed first. I know of 3 up here in the Cleveland area so they must be fairly common. Hope this helps your decision. Don
|
01:06 AM
|
|
Emc209i Member Posts: 3091 From: Charlotte, NC Registered: Apr 2005
|
Total ratings: 225
User Banned
|
|
. [This message has been edited by Emc209i (edited 12-05-2008).]
|
05:53 AM
|
|
Emc209i Member Posts: 3091 From: Charlotte, NC Registered: Apr 2005
|
Total ratings: 225
User Banned
|
|
| quote | Originally posted by SKIDMARK:
Buy a little MIG welder and learn to use it.....it's something you'll be glad you did for the rest of your life. Another handy tool is a sawsall.
You can get the stainless pipe off of ebay or here WWW.PERFORMANCE-CURVE.COM for pretty reasonable money.
Total for my exhaust is less than $250 but it was a lot of work. Prior to this project I never welded stainless and I learned a lot about it just by doing it. I don't like to pay someone for something I can do for myself....that's just me.
If you really don't want to take the time to do it yourself, there are many exhaust places that will fabricate a complete mandrel bent exhaust system for you but most want to do it on the car which means you have to get the engine installed first. I know of 3 up here in the Cleveland area so they must be fairly common.
Hope this helps your decision.
Don
|
|
I'm JUST like you, I like to do my own work... I'm having a meeting with my dad in 2 hours and I'm going to talk to him about this. How hard is to learn how to do quality welds, also what time frame? I'm REALLY quick to pick up on how to do things! I also have about a thousand other things I could do on my own with a welder...
|
05:55 AM
|
|
SKIDMARK Member Posts: 1350 From: Chardon, Ohio, USA Registered: Sep 2001
|
Since you have a little welding experience it shouldn't be too hard to learn to weld stainless. I suggest talking to people you know that weld and get some tips, read all you can, and get some scrap pieces and practice before you try your skills on an exhaust project. If you have a plan for the exhaust, cut the pieces one at a time to fit, then tack weld them in place before moving on to the next piece, you should end up with a decent exhaust system. Once a pipe is complete, take it off the car and finish welding all the joints. This is the easiest way I found to fabricate. The biggest problem I had was cutting the pipe square so that the ends butted together without big gaps but I think using a cut off saw instead of my sawsall would have solved that problem. So far as a time frame, it probably took me 30 hours or more to make the Y pipe but most of that was grinding down the welds and making it look pretty. I plan to show this car so that was important to me. If you just want a decent, functional exhaust then you could probably build it complete in about half that time, depending on your skill and level of ambition. Planning and having all the right parts is important too. Flaired ends, flanges, flex joints, O2 sensor bung, EGR tube mount, clamps and hangers should all be in your plan. Hope this helps..
|
11:02 AM
|
|
Dec 21st, 2006
|
Emc209i Member Posts: 3091 From: Charlotte, NC Registered: Apr 2005
|
Total ratings: 225
User Banned
|
|
How hard will it be to check the intermediate shaft bearing on my 3.4 when it comes in? Easy to get to or do you have to take the motor apart to get to it and or remove the parts that utilize the bearing? I was just thinking about how important it is to ensure a long life for the motor, and I know that that bearing has not been replaced. Also where can I pick up that bearing alone?
Thanks!
|
12:38 PM
|
|
Emc209i Member Posts: 3091 From: Charlotte, NC Registered: Apr 2005
|
Total ratings: 225
User Banned
|
|
Bump... Someone knows
|
03:26 PM
|
|
Dec 22nd, 2006
|
Emc209i Member Posts: 3091 From: Charlotte, NC Registered: Apr 2005
|
Total ratings: 225
User Banned
|
|
....... geee thanks.
|
10:10 AM
|
|
86GT3.4DOHC Member Posts: 10007 From: Marion Ohio Registered: Apr 2004
|
There are 4 bearings, nothing more than the cam bearings in a traditional motor, you will have to pull the timing belt and covers, which involves pulling the sprocket (not an easy task the first couple times you do it. Then removing the timing chain, which requires you take off the rear cam cover and back the cam out so that you can slip the gear off the long snout. Then remove the cam from the front.
If the bearings do need replaced, you will need to go the machine shop, it takes special tools and procedures to change them. The kit for all 4 is about $30, I think you can get it at advanced.
|
11:07 AM
|
|
PFF
System Bot
|
|
procarnut Member Posts: 622 From: Blum, Texas USA Registered: Mar 2006
|
Emc209i,
No worry's man. I'm not upset at all about your clutch choice. Everything is good. I'm sorry I didn't get back sooner. I've been unusually busy for this time of the year. I've got "alot on my plate" as they say. Anyway got to go so see ya later.
|
12:46 PM
|
|
Dec 24th, 2006
|
XzotikGT Member Posts: 897 From: Spanaway, WA, USA Registered: Mar 2004
|
I've been wanting to build a maxxed out N/A 3.4 dohc for a while. I think the time is getting closer. I dont really have any horsepower goals yet. I do know that I want this thing to spin beyond 7k. I am thinking 8-9k would be perfect. I want this thing to be dang near NSX-ish. I am thinking I should run some kind of forged rods good for high rpm useage, some fully grooved bearings, and some decent stock pistons, and some good bolts everywhere. You guys think there is anything else that I should do to make sure this thing stays together on the bottome end? The top end is a toss up. I know I will have to upgrade the springs, and I was considering the lightened lifters. Maybe if I can find them, lighter valves, but there are 24 of those...$$$$$. I will do a major port and polish Like I did on my turbo motor, and then there's the intake manifolds. I think the lower one is fine, doesnt seem to have any obvious obstructions., But I am thinking of doing a Mike Smith, and slapping a big ole box up there, or maybe saving a bit more money and make a ITB setup. I will NEED some cams, and after that I will make up a set of long ole headers, or maybe contact the people that already make some for our motor, and see what we can get done. So what am I missing? ------------------ 1987 GT 3.4 DOHC turboed Updated page 11/3/06 http://www.cardomain.com/memberpage/167457/1
|
01:41 PM
|
|
4-mulaGT Member Posts: 1210 From: Somewhere beetween raisin' hell... and saving grace. oh... and MN Registered: Jan 2006
|
| quote | Originally posted by XzotikGT:
I've been wanting to build a maxxed out N/A 3.4 dohc for a while. I think the time is getting closer. I dont really have any horsepower goals yet. I do know that I want this thing to spin beyond 7k. I am thinking 8-9k would be perfect. I want this thing to be dang near NSX-ish. I am thinking I should run some kind of forged rods good for high rpm useage, some fully grooved bearings, and some decent stock pistons, and some good bolts everywhere. You guys think there is anything else that I should do to make sure this thing stays together on the bottome end?
The top end is a toss up. I know I will have to upgrade the springs, and I was considering the lightened lifters. Maybe if I can find them, lighter valves, but there are 24 of those...$$$$$. I will do a major port and polish Like I did on my turbo motor, and then there's the intake manifolds. I think the lower one is fine, doesnt seem to have any obvious obstructions., But I am thinking of doing a Mike Smith, and slapping a big ole box up there, or maybe saving a bit more money and make a ITB setup.
I will NEED some cams, and after that I will make up a set of long ole headers, or maybe contact the people that already make some for our motor, and see what we can get done.
So what am I missing?
|
|
Individual throttle bodies?  higher compression pistons do these motors have 4 bolt mains? if not id see if you couldent machine some new ones. wouldent you want short headers for high end power? can the cam belts handle those R's?
|
03:06 PM
|
|
XzotikGT Member Posts: 897 From: Spanaway, WA, USA Registered: Mar 2004
|
Maybe not individual TB's at first but eventually. They seem to work well with the high revving NSX guys. I really need to do some research on the headers. Maybe I can do a dual exhaust setup, since I heard somewhere before that duals work on this motor. That would really simplify exhaust. I am going to have to look into the mains, that isnt the first time I have heard someone mention that for a good high RPM motor. ------------------ 1987 GT 3.4 DOHC turboed Updated page 11/3/06 http://www.cardomain.com/memberpage/167457/1
|
07:36 PM
|
|
Dec 26th, 2006
|
Fierobsessed Member Posts: 4782 From: Las Vegas, NV Registered: Dec 2001
|
|
08:51 AM
|
|
FieroWannaBe Member Posts: 2292 From: USA Registered: Oct 2004
|
| quote | Originally posted by XzotikGT:
I've been wanting to build a maxxed out N/A 3.4 dohc for a while. I think the time is getting closer. I dont really have any horsepower goals yet. I do know that I want this thing to spin beyond 7k. I am thinking 8-9k would be perfect. I want this thing to be dang near NSX-ish. I am thinking I should run some kind of forged rods good for high rpm useage, some fully grooved bearings, and some decent stock pistons, and some good bolts everywhere. You guys think there is anything else that I should do to make sure this thing stays together on the bottome end?
The top end is a toss up. I know I will have to upgrade the springs, and I was considering the lightened lifters. Maybe if I can find them, lighter valves, but there are 24 of those...$$$$$. I will do a major port and polish Like I did on my turbo motor, and then there's the intake manifolds. I think the lower one is fine, doesnt seem to have any obvious obstructions., But I am thinking of doing a Mike Smith, and slapping a big ole box up there, or maybe saving a bit more money and make a ITB setup.
I will NEED some cams, and after that I will make up a set of long ole headers, or maybe contact the people that already make some for our motor, and see what we can get done.
So what am I missing?
|
|
I think the stock oiling system would be a big hurdle, the pump has been known to starve the bottem end of oil, also a crankscrapper could help, but i think the oil passages can be enlarged; I remeber hearing about that from some perfomance book.
|
11:31 AM
|
|
4-mulaGT Member Posts: 1210 From: Somewhere beetween raisin' hell... and saving grace. oh... and MN Registered: Jan 2006
|
what about a dry sump oil pan?
I dont know if theres somthing more complicated than having a very hight oilpan, pickup and reservoir. if sombody could find/fab a pan and pickup you could get everything else from a racing catalog
|
11:55 AM
|
|
Emc209i Member Posts: 3091 From: Charlotte, NC Registered: Apr 2005
|
Total ratings: 225
User Banned
|
|
|
01:07 PM
|
|
XzotikGT Member Posts: 897 From: Spanaway, WA, USA Registered: Mar 2004
|
Dry sump? Imma have to go and get more info on this. Maybe I can make a larger capacity oil pan. Add a quart or two of capacity. You guys think stock rods will hold up to 8k? I think I will push it to 8k, and get the rest of the parts to get it to make power so the rpms will be useful, and not just make more noise. What parts you think will fail first on a stock motor? ------------------ 1987 GT 3.4 DOHC turboed Updated page 11/3/06 http://www.cardomain.com/memberpage/167457/1[This message has been edited by XzotikGT (edited 12-26-2006).]
|
01:58 PM
|
|
Emc209i Member Posts: 3091 From: Charlotte, NC Registered: Apr 2005
|
Total ratings: 225
User Banned
|
|
. [This message has been edited by Emc209i (edited 12-05-2008).]
|
02:52 PM
|
|
PFF
System Bot
|
|
|
Dec 27th, 2006
|
Emc209i Member Posts: 3091 From: Charlotte, NC Registered: Apr 2005
|
Total ratings: 225
User Banned
|
|
I got back from the garage today at 9:30PM. It took 4 hours of our conversation rich efforts to: Pull out cradle; Engine, Transmission, all wiring. Drain all fluids Discuss how we were going to route fuel lines Talk about why the GTP outside was pushing 300 HP (45 mins of talk and no work)  I'm tired! Pictures tomorrow!
|
12:50 AM
|
|
Fierobsessed Member Posts: 4782 From: Las Vegas, NV Registered: Dec 2001
|
| quote | Originally posted by Emc209i:
WHOA! I am mega mega impressed! 2.5 pipe right? Did you do your own welding in the garage? You are INSPIRING!!! =D |
|
Yes, it is an all stainless 2.5" system, I made the crossover using the cut up parts of a stock one (2.25"). The "Y" joins two 2.25" pipes togather and increases to 2.5" at the same junction, the WBO2 and normal O2 sensor bungs are just after the "Y". Then there is a donut joint, followed by the 2.5" cat, to the modified Flowmaster 80 series. The outlets are 2.25" to the tips which are recycled Fiero GT tips. Well, the parts picture explains most of it. 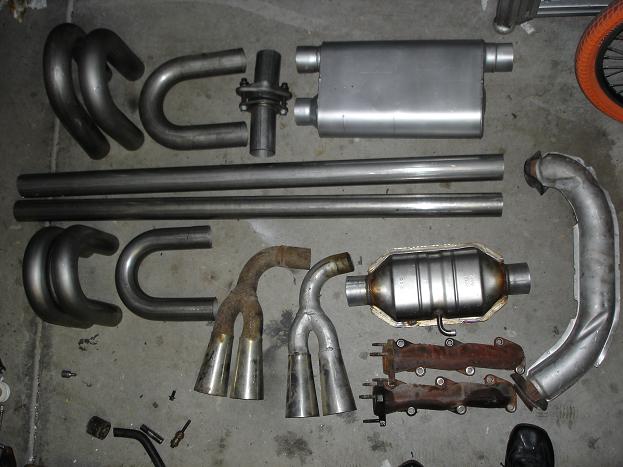 In reality, I was pretty efficient with my pipe usage, I used: 3, 2.5" stainless U bends 3, 2.25" stainless U bends 1, 2.5" Donut joint, 1, Flowmaster 80 series 2.25" outlets 2.5" inlet 1, 2.5" Catalytic converter 2, Factory stock Fiero GT tips 2, O2 stainless sensor bungs I did order two 4' lengths of pipe, 2.25" and 2.5". I wound up using NONE of it, the tails on the U bends was enough to do the whole project. My welder, a Millermatic DVI, (Dual Voltage Input, runs on 120 or 240!) with a .030" wire, was almost too powerful to weld this exhaust with. On its lowest setting I had to pulse the welder to not burn through. Honestly, a small 120V MIG (Gas) unit with .025" Stainless wire would have been perfect. Because of the big MIG that I was using, I will probably have to break out the even bigger TIG to clean up some of the messy welds I made with the MIG. It's not that bad, but it does have a few leaks I will find and fill. The foggier the helmet got, the welds got worse that's for sure  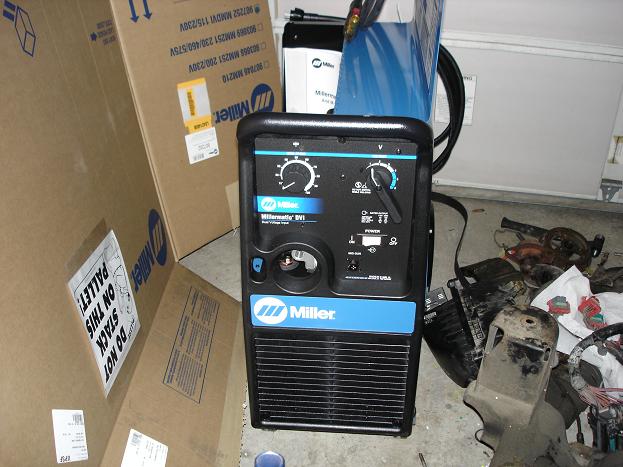 Did I mension stainless welds funky anyway?
|
04:19 AM
|
|
Chicken McNizzle Member Posts: 1310 From: Valencia, CA Registered: Jan 2004
|
Stainless is only "funky" because of its low surface tension, much like aluminum and other non-ferious metals. What you will want to do is increase the flow rate AND the post flow on the gas ( min 20 cfm and 10 seconds post flow ) at the given amperage ------------------ Former West Coast Fiero Employee New and Pre-Owned Auto Sales Consultant Power Ford Valencia
|
01:07 PM
|
|
Fierobsessed Member Posts: 4782 From: Las Vegas, NV Registered: Dec 2001
|
I didn't know that. Too bad my MIG has no post flow. I've never seen a MIG with it. My TIG how ever has it. The problem I had was mostly that the welds were a bit runny, kind of like paint, I would start in one spot, pull the trigger and move the gun. All the metal deposited ran to the point where I started, I found slowing the wire feed rate helped, but that made welding a little more difficult. But this is a little off topic. so...
Computers? Anyone have opinions?
|
05:20 PM
|
|
CommanderKeen Member Posts: 651 From: WA Registered: Sep 2004
|
3.4dohc questions. Ive got a completed swap car going into storage for a year or more. Motor is 100% stock. I want this engine to haul ass, and haul it with a turbo. Can someone give me a list of everything, and I mean EVERYTHING that can be done to the motor for power/reliability/turbo. 4-10lbs of boost is fine, but I want to know everything that i can have done to this motor. Cost is not an issue, I just need a list of thing for the motor.
|
05:39 PM
|
|
Emc209i Member Posts: 3091 From: Charlotte, NC Registered: Apr 2005
|
Total ratings: 225
User Banned
|
|
. [This message has been edited by Emc209i (edited 12-05-2008).]
|
05:58 PM
|
|
Dec 28th, 2006
|
CommanderKeen Member Posts: 651 From: WA Registered: Sep 2004
|
Actually, Im gonna leave the 3.4 alone, Im gonna have a 1970 Mustang Convertible in the next two weeks, and its costing me close to the same amount Ive put into my Fiero.
|
06:18 PM
|
|
Dec 31st, 2006
|
Emc209i Member Posts: 3091 From: Charlotte, NC Registered: Apr 2005
|
Total ratings: 225
User Banned
|
|
To The Very Top and that much farther away from an archive... Any new developments?
|
01:48 AM
|
|
Jan 1st, 2007
|
procarnut Member Posts: 622 From: Blum, Texas USA Registered: Mar 2006
|
bump
|
06:30 AM
|
|
Emc209i Member Posts: 3091 From: Charlotte, NC Registered: Apr 2005
|
Total ratings: 225
User Banned
|
|
Alright so I was going to PM some people, but I'd rather get this thread going again.
If I try to wire the entire car at the garage and do everything short of having Ryan reburn the PROM, will the car run well enough to drive it home (5 Miles)? I know it will throw a trouble code, maybe a stall once or twice, but will it be drivable?
Bob I know you didn't even get the chip burned right? And you're not having too many troubles, what do you think?
|
12:51 PM
|
|
PFF
System Bot
|
|
procarnut Member Posts: 622 From: Blum, Texas USA Registered: Mar 2006
|
I'm running a 96 computer which is obd 2. I know that the SES light is out in the car but I did have a trouble code for the automatic transmission. i am running a getrag so naturally it will set codes. As far as drivability it works great. Definatly hook up the VSS signal to the PCM, it's important for the idle air control to maintain idle and keep from stalling on decelleration. At first I was only hooking the vss to the speedometer and skip the imput to the ECM. Once I spoke to Loyde (FASTFIERO) he reminded me it affects the RPMs when stopping. THANKS LOYDE! He has been very helpful with all of my questions. If you are going with a Pre-95 computer you will need to do the same thing as the obd2. I am planning on buying a computer from Loyde, reprogramed for my applicaton later when I have the money. Right now I'm trying to paint my car and hopefully get the interior done in time for a car show in Feburary. I have alot to do.
Good Luck
|
08:05 PM
|
|
formulamoe Member Posts: 126 From: Waipahu, HI Registered: May 2005
|
I am in the process of putting 3.4 in my 328 rebody. I did not get a AC compressor with the engine but I notice the 87 duke I pulled out had the right pully on its compressor. Can I use the compressor on the 3.4? It worked when I pulled it. Thanks
|
10:40 PM
|
|
Emc209i Member Posts: 3091 From: Charlotte, NC Registered: Apr 2005
|
Total ratings: 225
User Banned
|
|
^.- I'm not positive, but I don't know why it'd hurt. The belt should be spining the compressor wheel at the same speed right?
|
10:45 PM
|
|
formulamoe Member Posts: 126 From: Waipahu, HI Registered: May 2005
|
yes it should be, I just wasn't sure about all the pressure switches that are needed for the ECM. I will study the schematics some more
|
10:47 PM
|
|
Emc209i Member Posts: 3091 From: Charlotte, NC Registered: Apr 2005
|
Total ratings: 225
User Banned
|
|
. [This message has been edited by Emc209i (edited 12-05-2008).]
|
11:20 PM
|
|
Jan 2nd, 2007
|
86GT3.4DOHC Member Posts: 10007 From: Marion Ohio Registered: Apr 2004
|
Yes you can use a Fiero compressor if you want, but the DOHC compressor is the better one. 1: Its (newer years) designed for R134A, no worries about seals and orings inside the compressor 2: Its a variable displacement, more efficient and no clutch slapping 3: Being vd, you dont need the mess of switches and pressure sensors The dohc compressor just needs one sensor, a high pressure reading to the ECM. This tells the ECM if the system is over pressure or under filled to shut off the compressor for saftey. Other than that the compressor runs all the time, just lowers displacement when less is needed. You can actualy just hotwire the compressor to be on all the time with the AC on if you want, and leave the ECM out of the mix, but its not reccomended in case you have a leak or something. If you're going to use the Fiero compressor, you just need the pressure and cycle switches like before, the DOHC ECM needs not know about it. [This message has been edited by 86GT3.4DOHC (edited 01-02-2007).]
|
11:59 AM
|
|
Emc209i Member Posts: 3091 From: Charlotte, NC Registered: Apr 2005
|
Total ratings: 225
User Banned
|
|
Cool thanks! I absolutly HATE the fiero compressors anyway. Mine was always low on coolent and so the cycle switch would throw the compressor on and off, on and off.
|
12:41 PM
|
|
Jan 8th, 2007
|
olaf_fiero27 Member Posts: 967 From: winnipeg,manitoba,Canada Registered: Oct 2004
|
K guys got lots of work done on the TwinCam last night. Took off the oil pan, windage tray and oil pump. Popped out 4 pistons and working on the other two. But Im going to send the crank out to get mic'd and ground if need be and looked over for stress cracks etc. But In order to do so I need to removed the timing chain but it looks like you have to take the timing sprocket off of the intermediete shaft.. How do you go about doing this?
|
09:06 AM
|
|
Emc209i Member Posts: 3091 From: Charlotte, NC Registered: Apr 2005
|
Total ratings: 225
User Banned
|
|
Punch the intermediate shaft all the way through the block. There's a freeze plug on the tranny side of the block that comes out and the shaft follows suite. Take a good sized hammer and hit the intermediate shaft, it'll pop out the back.
|
02:19 PM
|
|