I think it would be a great idea to make a legitimate F40 shift cable! Many of us running the Getrag Select cable as an F40 shift cable have broken them, so something sturdier is certainly needed.
But that brings up another question... Do you make them for replacements for those people who have used Getrag Select Cables as F40 shift cables, or do you make them to eliminate the need to cut the shifter base to relocate the cable sleeve stop. One group would get you immediate orders for replacement and the other will save people from additional work doing the F40 swap.
Now if you look at making them for replacement purposes...
On my F40 swap, I am running 2 getrag select cables - so they are the exact same length, but they shouldn't really be the same length. One of the aspects I don't like about my shifter cable setup is the "Shift" cable is too long and doesn't flow nicely with the select cable. I have tried to mask this excessive length as much as I can, but would love to have a proper length shift cable.
Here is why the shifter cable can be shorter than it currently is:
Once the shifter is modified, the "shift" cable sleeve stops behind the "select" cable sleeve, so that would imply the Shift cable (sleeve and overall cable) could be shorter by the amount seen here:
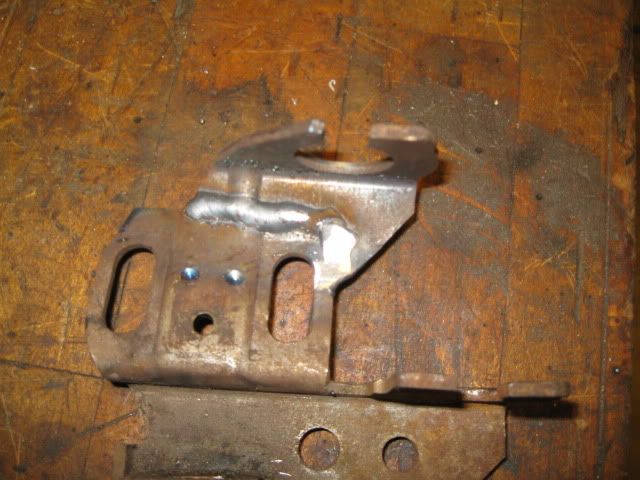
Likewise, as the transmission side, the "Shift" cable is also further back from the select cable, so its length could be reduced even further.
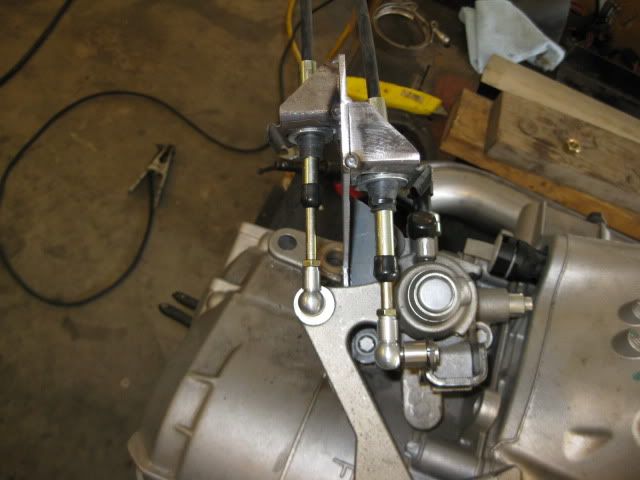
I can get a more accurate dimension, but I would suggest making a new F40 shift cable that is 3-4" shorter (sleeve portion and overall length) than the current Getrag Select cable.
The other area of concern is the range of motion of the cable. The Getrag Select cable has a range of motion of 1 3/4" and the F40 needs 1 3/4" to work the shift arm at the transmission. For my swap, I removed about 3/8" from the support sleeve to get some additional travel.
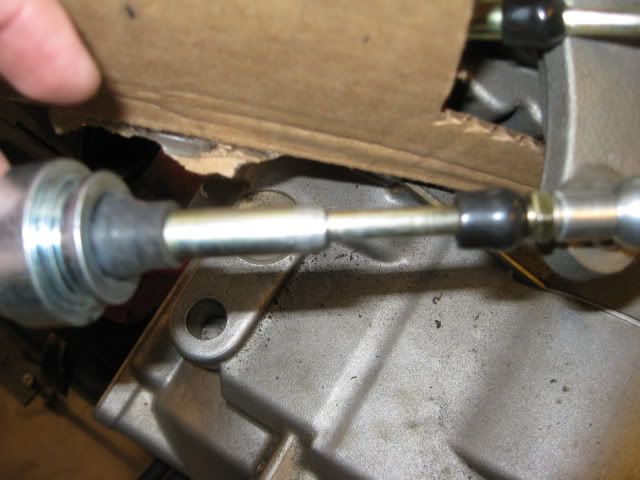
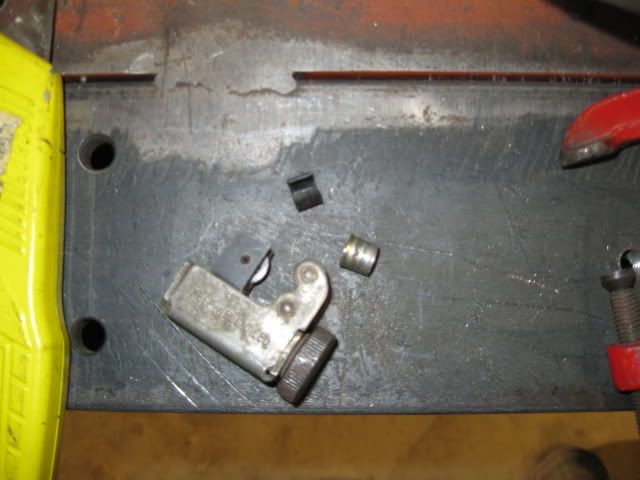

The issue with this modification is that with the cable fully extended (engaging 1st, 3rd or 5th), the rigid portion of the cable is nearly to the end of the support sleeve and allows the cable to buckle under aggressive shifting. The buckling is what eventually breaks the cable. Here is my broken cable that shows the relative placement of the end of the rigid cable.
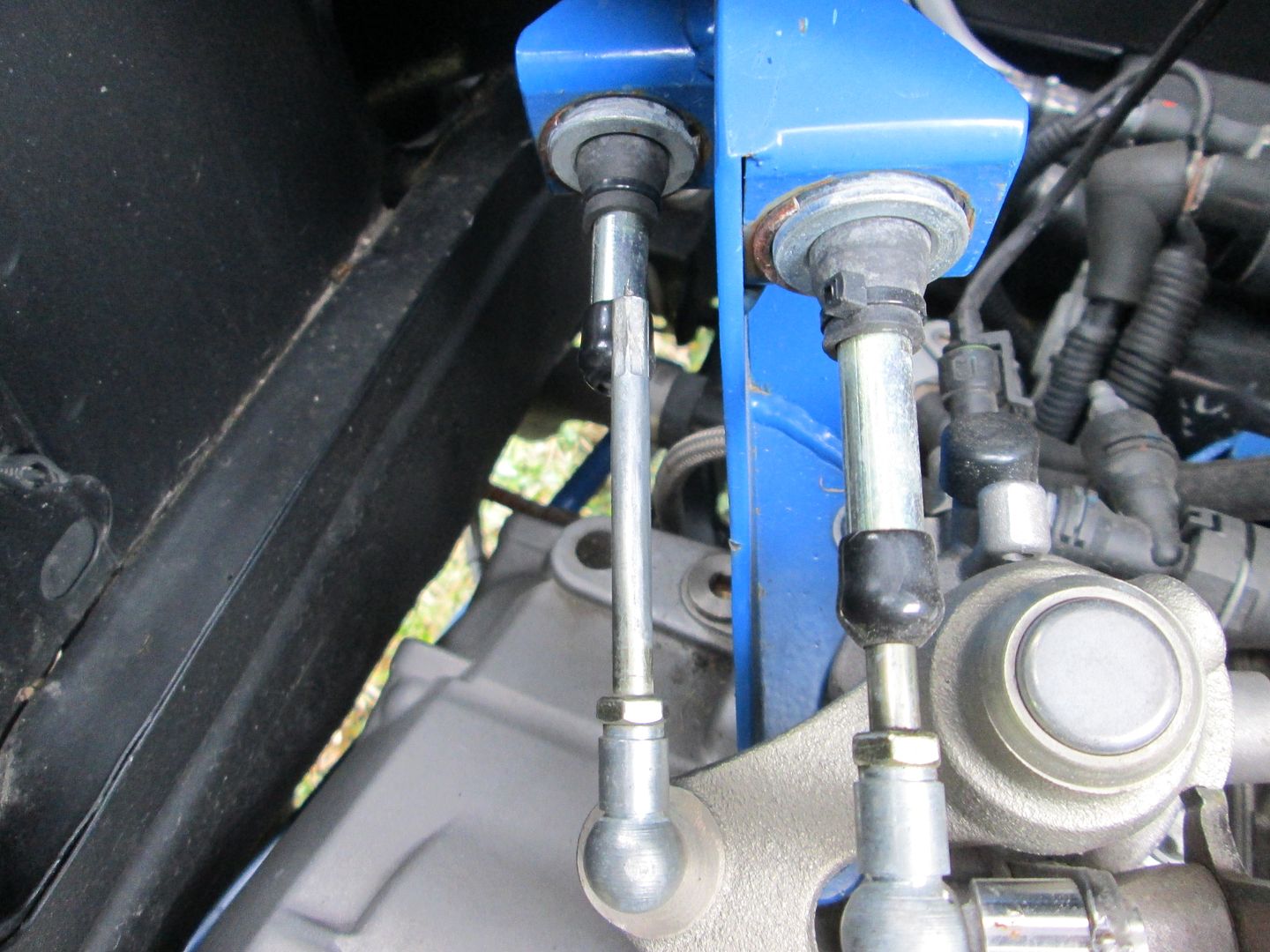
My suggestions for the range of motion changes is to give it 2" of travel at a minimum, extend the rigid portion of the cable at the transmission, and reduce the ID of the metal support sleeves so they can do a better job of supporting the rigid portion at maximum extension.
I haven’t started looking at the needed modifications to make a cable w/o needing to relocate the cable sleeve.
[This message has been edited by fieroguru (edited 05-16-2014).]