I imagine that ‘everyone’ has heard the old cliché "there is more than one way to skin a cat".
Below is General Motors Corporation’s approach to skin *this* cat without a ‘pickle fork’ or a BFH…
BackgroundVintage-Nut is a retired manufacturing engineer
who has only one fully functional hand.
My garage purpose is pretty straightforward; to achieve quality results with the least hardships possible which includes choosing the ‘right’ tools for the job.
Clarifying Press-Fit Ball Joints I
really understand that press-fit ball joints aren’t particularly an ‘enjoyable’ chore; nevertheless I’m
also distinguishing it shouldn’t be a nightmarish experience neither!
While researching on PFF; more than a few threads about changing ball joints had major difficulties and/or frustration complaints.
It’s also worthy to note that the front lower ball joints are ‘buried’ underneath of the lower control arms in a constricted recessed area.
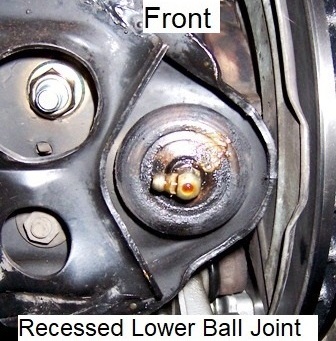
Thus, when my GT required new ball joints, the first thing I did was to get hold of the special adapters listed in the
Pontiac Fiero Service Manual to make a difficult task more manageable.
For this write-up, I’ll describe these particular ball joint adapters intended for the Fiero as ‘clamp’ adapters and ‘force’ adapters representing the two ends of a press.
In Action:
For Removal: The service manual ‘clamp’ adapter {receiver} matched perfectly into the constricted recessed area of the lower control arm and performed exemplary. The OEM joints were so easy to remove, this adapter is highly recommended! I didn’t use the manual ‘force’ adapter on the ball joint stud; I used a nut into the recess area of the step-adapter.
For Installation: The 1988 service manual requires a correction on the listed ‘force’ adapter.
The factory lower balls joints have ‘round’ base profiles which match with the service manual installation adapter; I believe MOOG K5297 likely fits on this adapter too.
Alas, factory joints aren’t available now and been replaced with GM 19463447. Since this joint has a different base profile; it will not seat correctly on the manual adapter, nor does most current aftermarket brands either.
To simplify, this photo shows the factory and present ball joint base profiles:
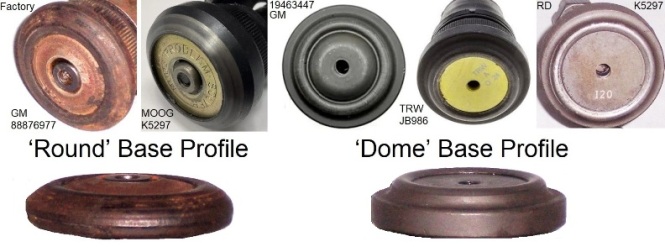
As a manual tool replacement, I used a standard 1.7-inch I.D. tube/pipe adapter what sat on the flat area outside of the ‘dome’ and worked very well. I really recommend the service manual ‘clamp’ adapter on the top of the arm as the surface is uneven. As I expected; the special adapter firmly held the press in place while the new joint was pressed in.
*Hence, the critical points at this juncture are; (A) the adapters will not interfere the recessed walls of the control arm; (B) the installation ‘force’ adapter must ‘match’ with the ‘seating’ area of the selected lower ball joint, which the results (C) will center and support the joint properly when pressing it into the control arm.
I hit my garage target and
for me; the adapters merit significantly surpassed the small expenditure.
If YOUR aim is to simplify this job, choose adapters wisely…
-------------------------------------------------------------------------------------
PrefaceThe
Pontiac Fiero Service Manual divides the upper and lower ball joints as two separate procedures.
Here, I’m blending them together as one flowing process; same manual ‘steps’, although the sequence is arranged differently.
In addition; the lower ball joint procedure states that the entire caliper/rotor/knuckle assembly stays ‘on’ the vehicle. For me, that statement is false
just because the knuckle hindered the use of my chosen ball joint press.
Obviously, the ‘easiest’ ball joint time is when the brake hydraulic system isn’t working, but with a ‘live’ system; either remove and suspend the caliper, or ‘suspend’ the
entire knuckle assembly in the wheel well. The latter is faster than the former and was doable, but a bit awkward…
SO, before jumping in; you’re required to read and comprehend this write-up all the way through to honestly analyze and evaluate the skills, tools and requirements; particularly the risk assessment.
General Motors Corp’s professional procedures; appropriate tools and illustrations are established in the 1988 Pontiac Fiero Service Manual. I merely contributed further details plus the supporting photos.-------------------------------------------------------------------------------------
Step-by-Step 1988 Fiero Ball Joint Replacements “On the Car” using
*Pontiac Fiero Service Manual {PFSM}
*Appropriate Ball Joint Adapters
*Additional Special Tools
Essential Special Tools Removal ‘Clamp’ Ball Joint Adapter: Kent-Moore J-37161-1 {highly recommend}
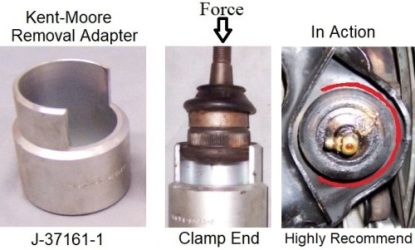
Removal ‘Force’ Ball Joint Adapter: Kent-Moore J-37161-3 {or equivalent}
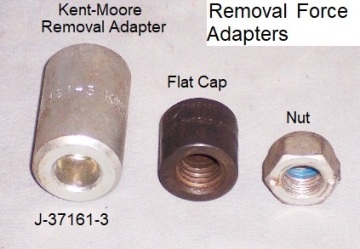
Installation ‘Clamp’ Ball Joint Adapter: Kent-Moore J-37161-2 {recommend}
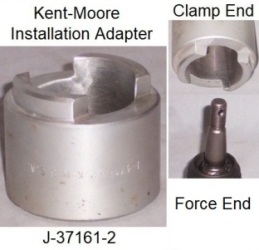
Installation ‘Force’ Ball Joint Adapter:
Round Base Profile: Kent-Moore J-37161-4
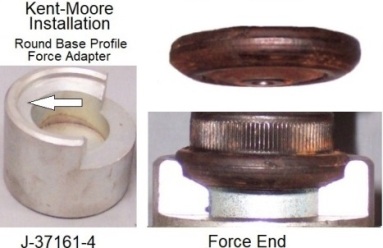
Dome Base Profile: 1.7-inch I.D. Tube/Pipe {or equivalent}
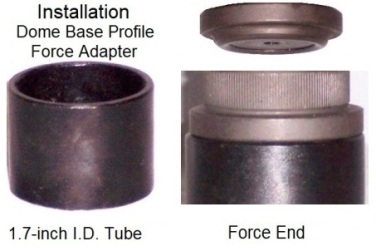
Please Note:
These Kent-Moore adapters were designed for the J-9519-10 Ball Joint Press; which is infrequent found nor ‘cheaply’. Notice the ‘special’ reduced tip of the forcing-screw and the welded adapter ‘holder’ at the base of the clamp.
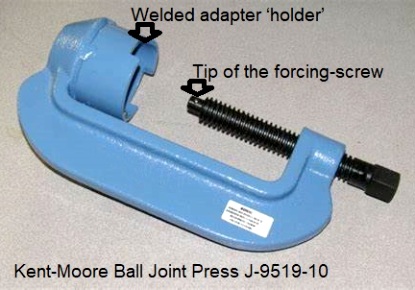
Kent-Moore ball joint adapters are easily ‘adapted’ with additional common adapters to fit them on a typical C-Frame Ball Joint Press, but with a larger throat.
Common Step-Adapters
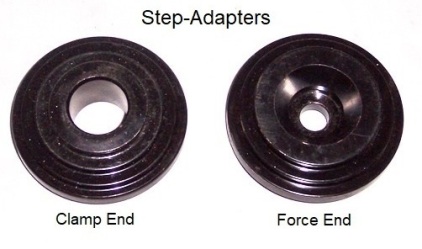
C-Frame Ball Joint Press, 9-inch throat
Additional Extremely Helpful ToolsTo disconnect the outer tie rod from the steering knuckle: Kent-Moore J-6627-A {or equivalent}
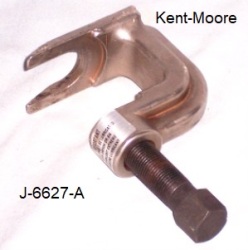
To disconnect the ball joint studs from the steering knuckle: Kent-Moore J-26407 {or equivalent}
’88 Ball JointsUpper:
There is not much choice; GM discontinued, Moog/TRW didn’t make them, members report that TFS part won’t fit properly, Rare Parts #10722 is big bucks, and Rodney Dickman is closing his doors soon…I brought Rodney’s Upper Ball Joints
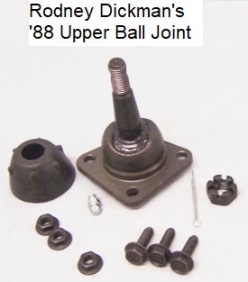
Lower:
MOOG K5297 and TRW JB986 will shortly be gone, however GM 19463447 {ACDelco Silver 46D2138A} and GM 88911632 {ACDelco Gold 45D2138} are still available, plus aftermarket choices like Dorman.
*An Interesting Note:
The pressing area of the Fiero lower ball joint has a series of narrow splines to ‘bite’ into the control arm to prevent movement. The O.D. of the factory splines measured 1.630-1.635”. I measured a couple of aftermarket joints; identical O.D. However, GM measured 1.640-1.645” which means more ‘grip’ to prevent movement.
I brought Genuine GM/ACDelco Silver Lower Ball Joints
PreparationIf raising only the front; engage the parking brake, chock the rear tires and then loosen the lug nuts on the front wheels.
Using the lifting points in section 0A page 11, raise and support the vehicle; I’m using a two-post electromechanical auto lift. Since the lower ball joints are recessed; I raised the bottom of the lower control arms two-feet from the ground to create additional working space.
If raising the vehicle with a hydraulic jack, ALWAYS use jack stands to support the car!
NEVER work under a vehicle which is only supported by a hydraulic jack -
never.
Remove Both Front Tires/Wheels
⚠ INJURY / DAMAGE CAUTION:
Support the lower control arms effectively under the coil springs on a firm surface which will NOT move.
This keeps the front coil springs compressed while the steering knuckle is disconnected.
IF this support shifts - personal injury and/or property damage can occur!
Please Notice: The coil spring support surface beneath the arm is uneven because the shock and mounting bolts. I used a piece of 1.625-inch I.D. pipe on a jack stand; this pipe sat around the shock and between the mounting bolts.
My Set-Up:
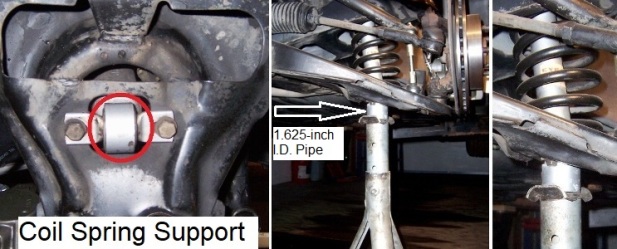
Unbolt the brake hose retainer from the upper control arm for more knuckle movement.
*If the job includes replacing the outer tie rods;
first measure from the outer tie rod grease fitting to a fixed reference point on the steering rack on both the driver’s and passenger’s side. These references numbers are to set the toe alignment close as possible when changing out the outer tie rods. Then before disconnecting each outer tie rod from the steering knuckle; clean the inner tie rod threads and then loosen the jam nut.
Remove the cotter pin and nut from the outer tie rod.
Apply penetrating oil at the outer tie rod connection at the steering knuckle.
Disconnect the outer tie rod from the steering knuckle with Kent-Moore J-6627-A tool {or equivalent}
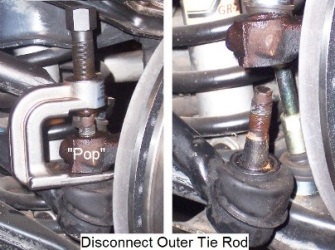
Turn the knuckle, remove both cotter pins from the ball joints and loosen the nuts.
Apply penetrating oil:
@ the lower ball joint connection which is pressed into the control arm
@ both ball joint stud connections in the tapered bosses of the steering knuckle
Upper Ball Joint / RemovalFactory upper ball joints have flat head rivets and were deformed from underneath, while new joints will include new hardware. If the joints are secured by bolts/nuts; please ‘skip’ the rivet steps and jump to: “
With the factory upper ball joint rivets gone” below.
Remove the grease fitting from the upper ball joint.
The PFSM recommends center punch; pilot hole; drill the rivet heads, then punch out the rivets.
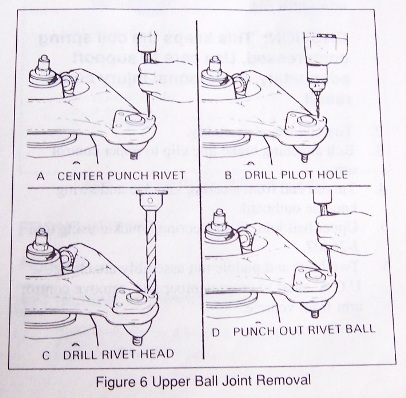
Note: If you’re thinking to ‘grind-off’ the rivet heads; please reflect on my experience…
The depth of the factory rivet heads were 0.10-inch, so I set the depth of the pilot holes at 0.20-inch.
I drilled the pilots with a 0.062-inch drill bit, on low speed plus cutting oil to keep the friction/heat low as possible. Then, to minimize any significant drill bit wander, I used 1/16-inch increments {0.125” / 0.187”} and ended on a 0.234-inch drill bit.
With a chisel and a hammer, I eliminated the heads; however the rivet remnants were firm and
impossible to punch out. So, I drilled 0.40-inch deeper from the top of the joint {.125”/.187”/.234”} to remove more rivet material, making it easy to punch them out from the arm. If you have compressed air; blow out the chips and clean the entire area.
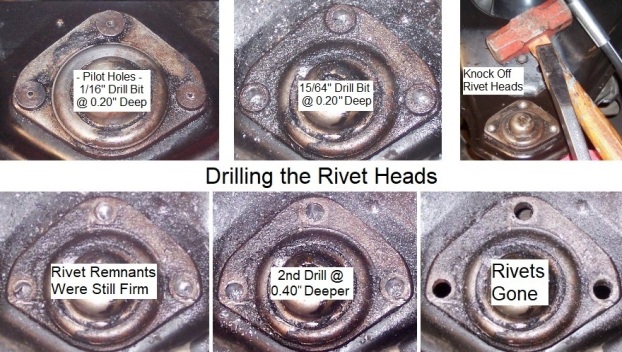
With the factory upper ball joint rivets gone; reapply penetrating oil at both ball joint stud connections in the tapered bosses of the steering knuckle.
Remove the lower ball joint nut and disconnect the stud from the tapered boss in the knuckle using Kent-Moore J-26407 tool {or equivalent}. Remove the tool and loosely thread the nut back on lower ball joint stud.
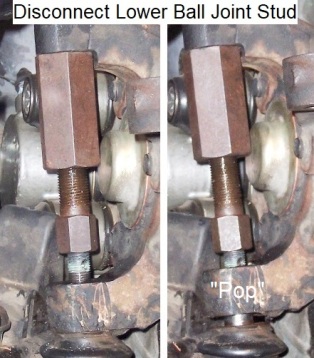
Remove the upper ball joint nut and disconnect the stud from the tapered boss in the knuckle using Kent-Moore J-26407 tool {or equivalent}.
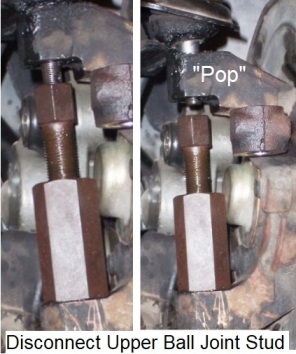
*If the upper ball joints are secured on the arm by bolts/nuts; lift up the upper arm to remove the ball stud from the knuckle; then swing the knuckle assembly out of the way, and then remove the hardware.
Remove the upper ball joint; push the knuckle assembly out of the way, and clean the mounting surfaces.
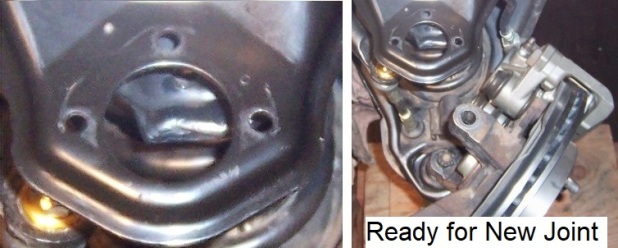
Inspect the control arm for any damage…if so; repair/replace the arm as required.
Upper Ball Joint / InstallationA Note on the Upper Ball Mounting Torque; the PFSM says:
“
Install [the]
upper ball joint to [the]
control arm with nuts and bolts. Torque to specifications provided in service repair package” which is a mystery…
Rodney didn’t include a torque specification and his bolts are steel, black oxide finish; class 10.9 and size M6x1.0 with metal locknuts.
Lacking an ‘official’ torque spec; I turned to the internet….
The Fine Print:
There are numerous "real world" factors can alter the torque-tension relationship; however, the material, diameter, fine/course threads and lubricated or dry threads are the main concerns.Given that; a few sites showed the ‘ideal torque’ for class 10.9 / M6 x 1.0 as:
Bolts: Dry: 11.1 ft-lbs / Lubricated: 8.3 ft-lbs
Locknuts: Prevailing-on torque (1st installation) 3 ft-lbs
11.1 + 3 =
14 ft-lbsI’m used threadlocker as well, so the hardware was cleaned with Acetone first.
Install the new upper ball joint onto the upper control arm ensuring that it is seated properly.
I applied blue threadlocker on the bolts; installed them on top, with the locknuts below.
I adjusted my torque wrench at 5 ft-lbs first, then 10 ft-lbs, and at the final setting of 14 ft-lbs.
Thread the grease fitting in the joint and secure it being careful to not over tighten it.
*
Rodney included a straight grease fitting; I’m reusing the factory 90-degree Zerk fitting pointed at the original inward position.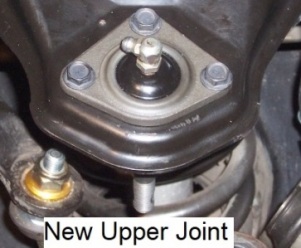
Rodney’s upper ball joints included separate protective boots which I installed them later.
Lower Ball Joint / RemovalPrepare a raised surface in the wheel well to place the entire brake hose/caliper/rotor/knuckle assembly
{OR remove the caliper from the knuckle and then suspend the caliper out of the way} Remove the lower ball joint nut from the stud; lift up the knuckle assembly from the lower ball joint stud, I sat it down on the raised surface in the wheel well.
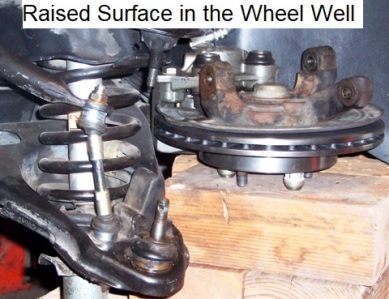
Note: The factory lower ball joints didn’t have a snap ring to hold the joint into the arm. Double-check if your lower ball joint has a snap ring or not…if so; remove the snap ring from the groove with snap ring pliers.
Remove the grease fitting from the lower ball joint.
Reapply penetrating oil at the lower joint connection in the control arm to reduce friction and resistance.
To press-out the old ball joint from the lower control arm; assemble the ball joint press and the adapters referring in the PFSM illustration “Figure 8 - Remove”
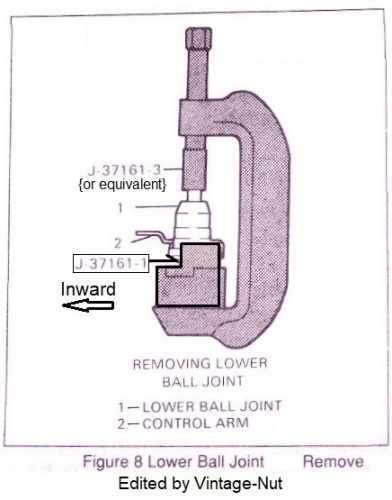
My Set-Up:
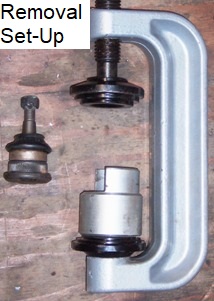
Place the removal force adapter on top of the lower ball joint stud; put the removal ‘clamp’ {receiver} adapter in the bottom of the lower control arm observing ‘inward’ side, and snug the press.
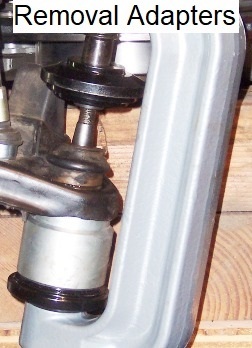
With the press and adapters aligned; maintain the positions and turn the ball joint press's hex end with a heavy-duty breaker bar to press-out the ball joint from the lower control arm.
With the lower ball joint removed, clean the recessed mounting area where the joint’s surface meets the arm opening; inspect for any damage…if so; repair/replace the arm as required.
Lower Ball Joint / InstallationGM joints come with preinstalled protective boots; some aftermarket joints have separate boots which are installed later.
Lube the lower control arm opening and the mating area of the new ball joint with a thin layer of grease.
To press-in the new ball joint into the lower control arm; assemble the ball joint press and the adapters referring in the PFSM illustration “Figure 8 - Install”
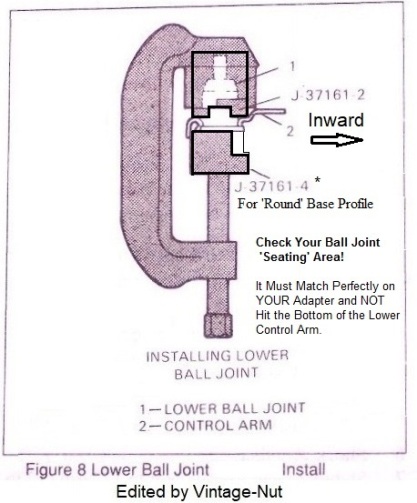
My Set-Up:
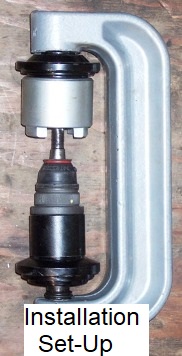
Now is the tricky part to assemble the parts on the arm; this is the method I found the best:
*Center the ball stud in the joint so it won’t hit the ‘clamp’ adapter
*Place the clamp adapter on to the top of the control arm observing ‘inward’ side
*Situate the step-adapter on the clamp and put the press on the pair, holding them on the arm
*Place the step-adapter on the press’s forcing-screw, then the force adapter plus the ball joint
*Slowly turn the press’s forcing-screw to elevate the joint into the bottom of the arm opening
*Align the parts, check that the ball stud is still centered with the top adapter, and snug the press
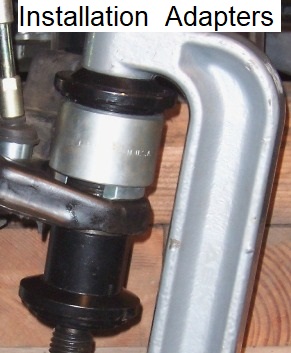
Pay close attention to keep the press/adapters/ball joint/control arm aligned and everything in a straight line. Maintaining the positions correctly; slowly and carefully turn the press’s forcing-screw in.
Generally, the turning force will be constant when the joint is aligned correctly as the splines are pressed into the opening. Be attentive and ‘feel’ if the joint is moving into the control arm opening steadily.
*IF you feel the travel is unyielding; double-check that your adapter isn’t hitting with the recessed sides of the control arm.
A Tip:
Because it is hard to see; I removed the press/adapters once the joint has a ‘grip’ into the arm and inspected if the joint is pushing in evenly and uniformly.
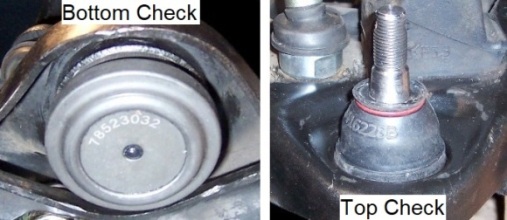
*IF you see that the joint is crooked; pull it out and start again
*IF the joint get wedged - use the ‘Remove’ adapters to ‘push’ the joint out from the lower control arm.
Continue to turn the forcing-screw, check that the joint stud isn’t striking the ‘clamp’ adapter, until the joint is fully pressed into the control arm.
With the new lower ball joint firmly seated; remove the press/adapters and examine that it is fully against on the arm.
The majorities of lower ball joints includes snap rings; check that the snap ring groove is level with the control arm surface, and then install the snap ring in the groove with snap ring pliers.
*If the snap ring groove is below of the arm surface; the ball joint need to be pressed further into the arm.
*SIDEBAR: Snap Ring Location ------------------------------
Of all the pressed ball joints that I have installed; the bottom of the snap ring grooves has
always been level with the supporting surface to prevent joint movement. Regrettably, the bottom grooves on this installation were
higher than the supporting surface with a 0.07-inch gap.
Obviously, this snap ring location doesn’t assist to prevent joint movement. To me, this isn’t proper, so I added a 1.64-inch I.D. snap ring
around the joint base, which were 0.062-inch thick, and removed the ‘slack’ from the arm to the joint’s snap ring. Problem Solved.
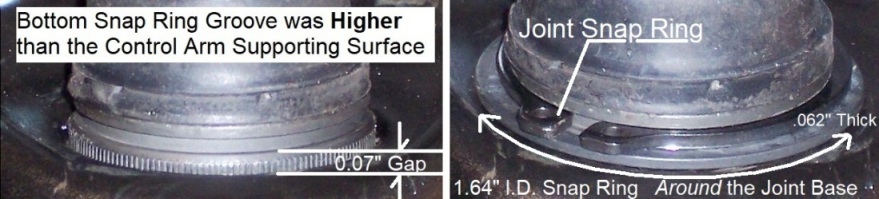
---------------------------------------------------------------------
*If the lower ball joints included separate protective boots; install them at this time.
Thread the grease fitting in the joint and secure it being careful to not over tighten it.
*GM included a straight grease fitting; I’m reusing the factory 90-degree Zerk fitting pointed at the original inward position.
Button It Up!*If the job includes replacing the outer tie rod, this is the ‘perfect time’ before knuckle installation;
thread off the old ends and thread on the new, using the driver’s and passenger’s toe alignment references numbers, then snug the jam nuts. Inject grease into the new ball joints; rotate the studs to completely lube the balls, and then position the cotter pin holes as front-to-rear for easier installation.
Clean and inspect the three tapered bosses in the steering knuckle that they aren’t out-of-round, deformed or damaged…if so; STOP and replace the part!
Lube the tapered studs on both ball joints and their mating tapered bosses in the steering knuckle with a thin layer of grease, and then slide the upper ball joint’s protective boot on the stud.
Lift up the steering knuckle assembly; guide the tapered boss in the knuckle onto the lower ball joint stud; then raise the upper control arm and guide the knuckle under the upper ball joint stud into the tapered boss, and then spin the two nuts on.
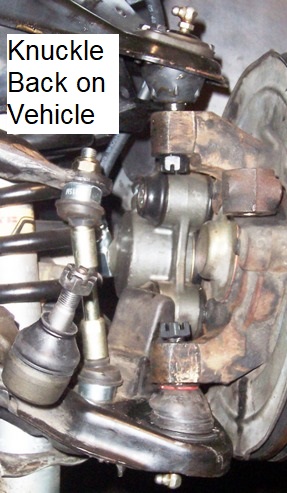
*If the upper control arm tension from the rubber bushings won’t reach the knuckle’s upper tapered boss; lift up the knuckle onto the upper ball and spin the nut; then using the weight, push the arm/knuckle onto the lower ball joint and spin the nut.
Torque the Upper Ball Joint Nut at the Knuckle
30-40 ft/lbs {Maximum 1/6 turn to align cotter pin; Not to exceed 55 ft/lbs}
Install a new cotter pin
Torque the Lower Ball Joint Nut at the Knuckle
26 ft/lbs + ½ turn {Maximum 1/6 turn to align cotter pin}
Install a new cotter pin
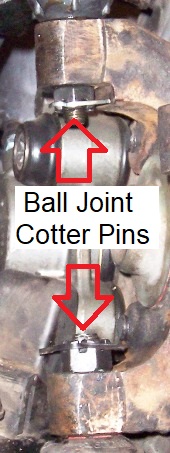
*If the brake caliper was suspend; reinstall it on the knuckle and torque the hardware at this time.
Lube the tapered stud on the outer tie rod and the mating tapered boss in the steering knuckle with a thin layer of grease.
Align and guide the outer tie rod tapered stud into the mating tapered boss in the steering knuckle, and then spin on the nut.
Torque the Outer Tie Rod Nut at the Knuckle
15 ft/lbs + ½ turn {Max 1/6 turn to align cotter pin}
Install a new cotter pin
*If the outer tie rods were replaced; tighten and torque the jam nuts.
Secure the brake hose retainer on the upper control arm
Final lube on the steering knuckle connections {upper/lower ball joints and outer tie rod}
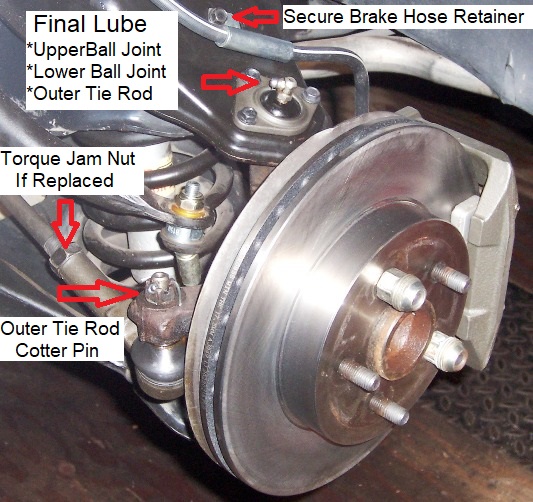
Remove the coil spring support underneath the lower control arms
Secure Both Front Tires/Wheels
Lower the vehicle to the ground
Torque the Front Lug Nuts
Dry: 100 ft/lbs
Torque the Plastic Lug Nut Covers {if used}
15 in/lbs
Schedule a Wheel Alignment Appointment before putting the vehicle back in service.
Voilà, pour your favorite adult beverage and relax – good job, well done!
------------------
Original Owner of a Silver '88 GT
Under 'Production Refurbishment' @ 136k Miles